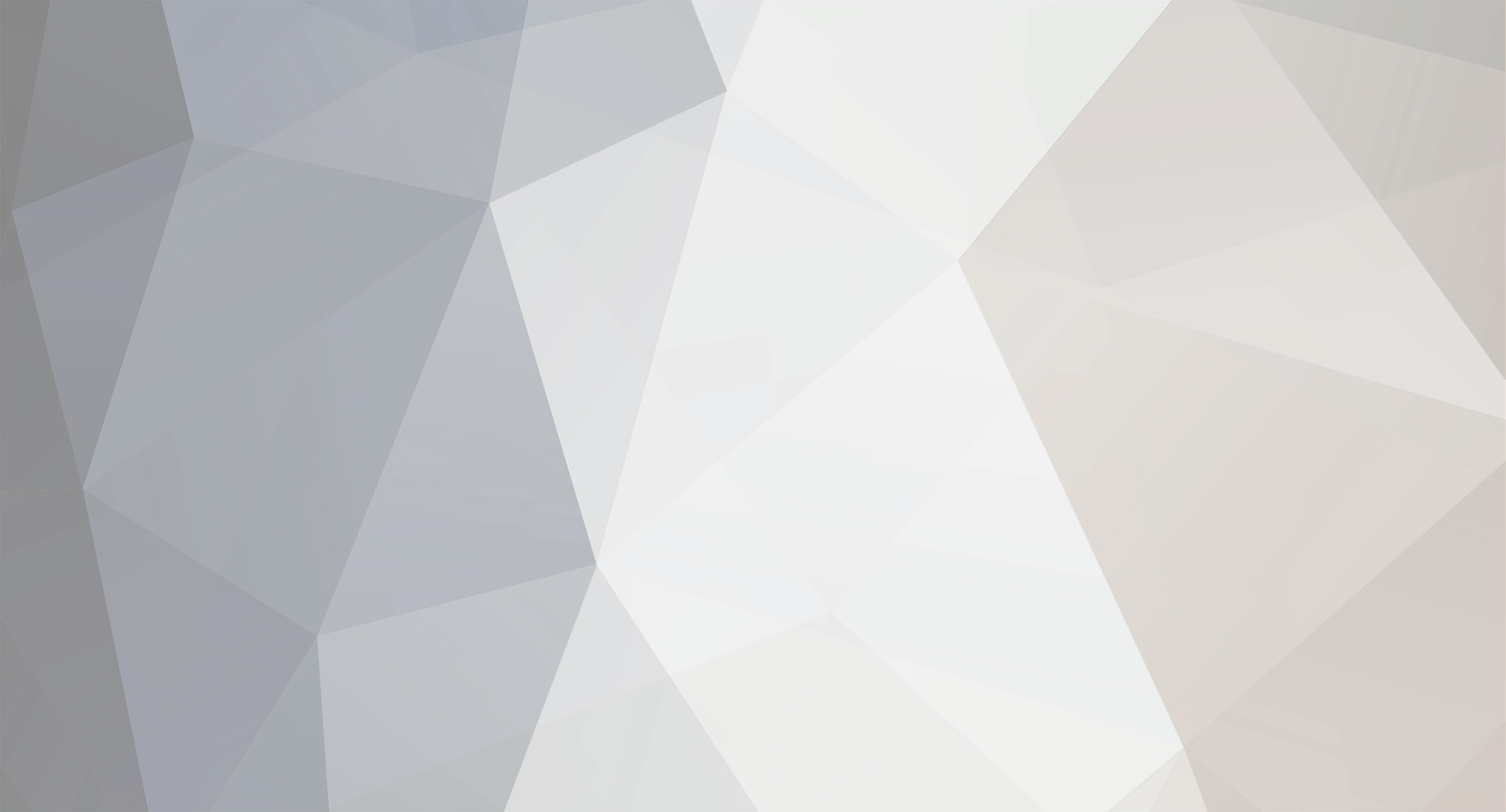
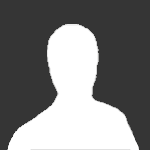
RJLee
Members-
Posts
6 -
Joined
-
Last visited
Content Type
Profiles
Forums
Events
Everything posted by RJLee
-
Yes. But I do think you do need to ask yourself how much risk tolerance you have for this upgrade. If you are unlucky and get a bad unit, fixing it will at a minimum require some mild DIY tinkering (e.g., opening things up with the included allen wrench, plugging/re-plugging cables, etc.), and possibly might involve substantial cost and delay which could make it cheaper to write off the whole thing. You might end up with none of these problems, but there isn't any way to know whether you're going to get a lemon -- if you do, the safety net is small. For me, the tradeoff is worth it. I like their design innovation, their iterative improvements, and the fact that they are committed to exactly my niche of interest. Their price point is certainly not cheap, but is competitive -- and even with the QA question mark, really is not so expensive that it represents a huge risk based on my overall investment in the hobby. Most of all, I like that they are continuing to release new improved products and seem committed to building stuff that I've only dreamed of. Though the analogy isn't perfect, I think that my view is similar to that of any early adopter -- there are going to be bugs and you may end up eating some costs as a result, but I will pay the price because I like the overall direction that they're taking things and I'm willing to gamble on not getting a bad unit. Even while I was suffering stick disconnects (and who knows, may still in the future), I still would consider spending more money with Winwing. This is obviously not going to be true for everyone, and you have to decide on what you want. Frankly, if you fly DCS every day, this would be your only HOTAS option, and having a plug-and-play unit with zero downtime is a very important priority, then I'd advise against buying Winwing. But if you have more patience, maybe have been doing this for a long time and are used to "cockpit maintenance simulator" as an unofficial mini-game, and have an old Warthog or X52 in the closet that you can use as a temporary backup, then I think you should give it a look. I've bought quite a lot of their stuff in the last 18 months, had some ups and downs (not perfect, not terrible), and don't regret anything.
-
I have the same (Orion 1 base and F-16EX grip) and was having intermittent stick disconnects, occasional disconnects of the grip only (but not the base), and periodic lagginess/latency in the main stick axes when I moved the stick "aggressively" in circles while in the SimApp Pro status screen. After changing USB cables and hubs, reseating the DIN connector in the grip, and doing a bunch of other random things, I finally opened the base, peeled off the hot glue from the two main connectors, and reseated them. It's been about a week and I haven't seen any problems since, so hoping that fixes it. I examined the base while the cover was off and suspect that the cables were a little short and/or the connectors weren't fully seated when they were glued in place. With nothing to relieve the strain, certain stick movements were pulling on the cables enough to break the connection. But we will see.
-
So far I'm in love with mine. Sometimes I just like to gaze at it, even when the rig is shut down, while it winks greenly at me. It's unseemly. I wouldn't describe anything that I've experienced as a quality control problem (no defective parts or the like). It's more that the assembly process can be a little bit finicky. The fixes mostly amount to tightening or loosening screws to one degree or another, which is something that I can handle (I am not very handy and would be unhappy if it required much more). But of course I can't speak to the non-responsive idle button that Paschon reports (though if EXPENDTripwire is right about this being another screw alignment issue with the finger lifts, it would not surprise me). Oddly enough, I was expecting the biggest problems to be with SimAppPro, and it's been fine for me.
-
I just received my Orion 2 throttle base + F/A-18 handles (part of an F-16EX stick bundle that was pre-ordered 4/11, paid for 5/4, arrived 5/18-19). I'm coming from an early-batch Thrustmaster Warthog with stick extension, and so far I am thrilled. That said, in the beginning I did run into some annoying issues, most of which had to do with the new finger-lift/detent assembly. Just thought I'd share in case it's helpful to anyone (this mechanism is new to the Orion 2 and I wasn't able to find a lot of guidance outside this thread): 1. Squeaky afterburner entry. In the beginning mine was just as bad as Paschon's video. As mentioned above, loosening the large screw that holds the noisy finger lift to the throttle arm solves this problem (mine was mostly on the larger starboard-side throttle handle). Some trial and error is necessary -- too loose and the finger lift "striker" will rotate crookedly, and this will affect how it goes over the afterburner detent. 2. Inconsistent push-through force for the afterburner detent. With the screw in (1) properly loosened, each individual throttle handle passed pretty smoothly over the AB detent. However, moving both throttle handles together sometimes required a lot more force (in some cases I found it nearly impossible to engage afterburner). I think this has to do with the odd angle of pressure applied when your hand is on both throttles, combined with the loosened screws in (1). What happens is that the finger-lift striker does not always hit the detent striking surface in the exactly the same way. If you hit it just right, it goes over relatively smoothly. If you don't, it jams. The simple solution that seemed to work for me was to put a small piece of Scotch tape (ordinary non-glossy stuff found in office desk drawers everywhere) on the detent striking surface. This reduced the plastic-on-plastic friction between the finger-lift striker and the detent plate so that it now doesn't matter if the striker hits it "wrong" -- it still slides through smoothly. Now the motion is very similar to the 3D-printed push-through detent that I had on my Warthog throttle. No doubt there are better approaches (silicone tape, plastic-safe lubricants, etc.) but this one is cheap and not very messy so I will try it for now. 3. Jammed sync lock. The sync lock is a small magnetic rod that you slide over to connect the two throttle handles together (for use in single-motor airplanes). I understand that a common complaint with the Orion 1 was that the sync lock was too loose, leaving some annoying play between the connected throttles. The Orion 2 may overcompensate a little bit by making the sync lock (which is built into the finger-lift assembly) very, very, very tight. When I first assembled the throttle, the sync lock slot was slightly misaligned; it was very difficult to engage and very nearly impossible to disengage. The WinWing assembly instructions tell you to engage the sync lock first before you attach the finger lifts to the throttle arms, but this understates the process. I had to take everything back apart, loosen both finger lifts, hold them in alignment, and gradually tighten one screw by a little bit, test the sync lock, tighten another, test again, loosen the first, test again... It's like attaching a cabinet door so the hinges line up. When properly aligned the sync lock will still be tight, but it will engage and disengage fine. Bonus tip: When you first attach the Orion 2 detent plate to the throttle base, the instructions tell you to loosen the idle detent block and move it forward along the detent arc (in its natural position it is blocking one of the attachment screw holes). I suggest not leaving the idle block loose in the detent arc -- tighten it in place right away. The issue is that it is held in place with a very, very short screw and a very, very tiny square nut. If you leave the idle block loose, that square nut literally hangs on one thread, and if you are unlucky it may come loose and fall into the throttle well. If you are very unlucky, it will then roll into a round hole at the bottom of the well that is just large enough for it to fit, and disappear into the interior of your throttle base never to be seen again. Keep a sharp eye on these tiny parts any time you are moving the detent blocks or attaching the space-sim center detent!
-
Hi all-- Decided to try my hand at shipboard operations with the PFM Su-33. I ended up collecting a fair number of replays to figure out what I was doing wrong, and put together a short video. These are still not very good landings, but they are much less dangerous than all of the deckspotting I was doing a day or two ago. If nothing else, both the Flanker-D and Kuznetsov are very pretty to look at in 2.5! Hoping for a carrier update sometime in the future (hopefully with a working ball)...
-
I registered in these forums to express my gratitude to the developers of this wonderful software! I am converting over to DCS after many years with Falcon BMS, and Ikarus has provided a near plug-and-play solution for my triple-monitor/touchscreen setup with very little (if any) lag that I can see. I did notice a few glitches in the full-featured F-5E-3 profile that comes packaged with the software, and I tried to fix them as best as I could (you will want to check my work before doing anything important with it, as I am not a programmer and also was relying on Google Translate for the Ikarus documentation). 1. The airspeed indicator (instrument #5) had a bug that caused the IAS needle to become erratic between 250 and 300 knots (the needle would suddenly jump to about 400 knots). I traced this back to a typo in the input field, and in doing so I also found that the latest input/output values in the F-5E export script had been updated to include 20 data points (rather than 16). So I updated everything and the IAS needle now appears to work properly. 2. The fuel autobalance switch (switch #11) was mispositioned, appearing several inches to the right of the proper panel location. This switch is rotated 90 degrees and Ikarus seems to have trouble with positioning rotated switches properly in editor mode. I was finally able to fix it by moving the switch only while it was at 0 degrees rotation, then rotating it to 90 degrees (this took some trial and error since the center of rotation is not in the middle of the switch). 3. A similar problem appeared with the nav mode selector switch (switch #81), which is the other switch in this profile that is rotated 90 degrees. Things that I tried to fix but could not: a. Mach speed indicator -- I can't find the texture for the mach placard, and in any event I don't know how to translate the behavior of this instrument into Ikarus' input/output fields. As I understand it, the mach placard rotates based on barometric altitude and shares the same needle position as the IAS needle. But the mach dial increments are also nonlinear in a different way from the knots dial, so...? Sad face with hurting head for me. (As I understand that some people have reported to Belsimtek that the mach-meter is currently implemented incorrectly, it might be best to wait for the update before spending too much effort trying to fix it.) b. The whiskey compass is currently stuck. I tried to at least fix the heading by tying the value to the HSI heading indicator (DCS ID 32), but no matter what values I placed into the input/output fields, the compass would always rotate half as fast as it should (i.e., when at 060, the compass would indicate 030), and at compass heading 180 would snap back to 000. I eventually gave up on this one too. I have attached my F5E.ikarus file with my small fixes in case it is useful. Keep up the good work! F-5E-3-fixed.ikarus.zip