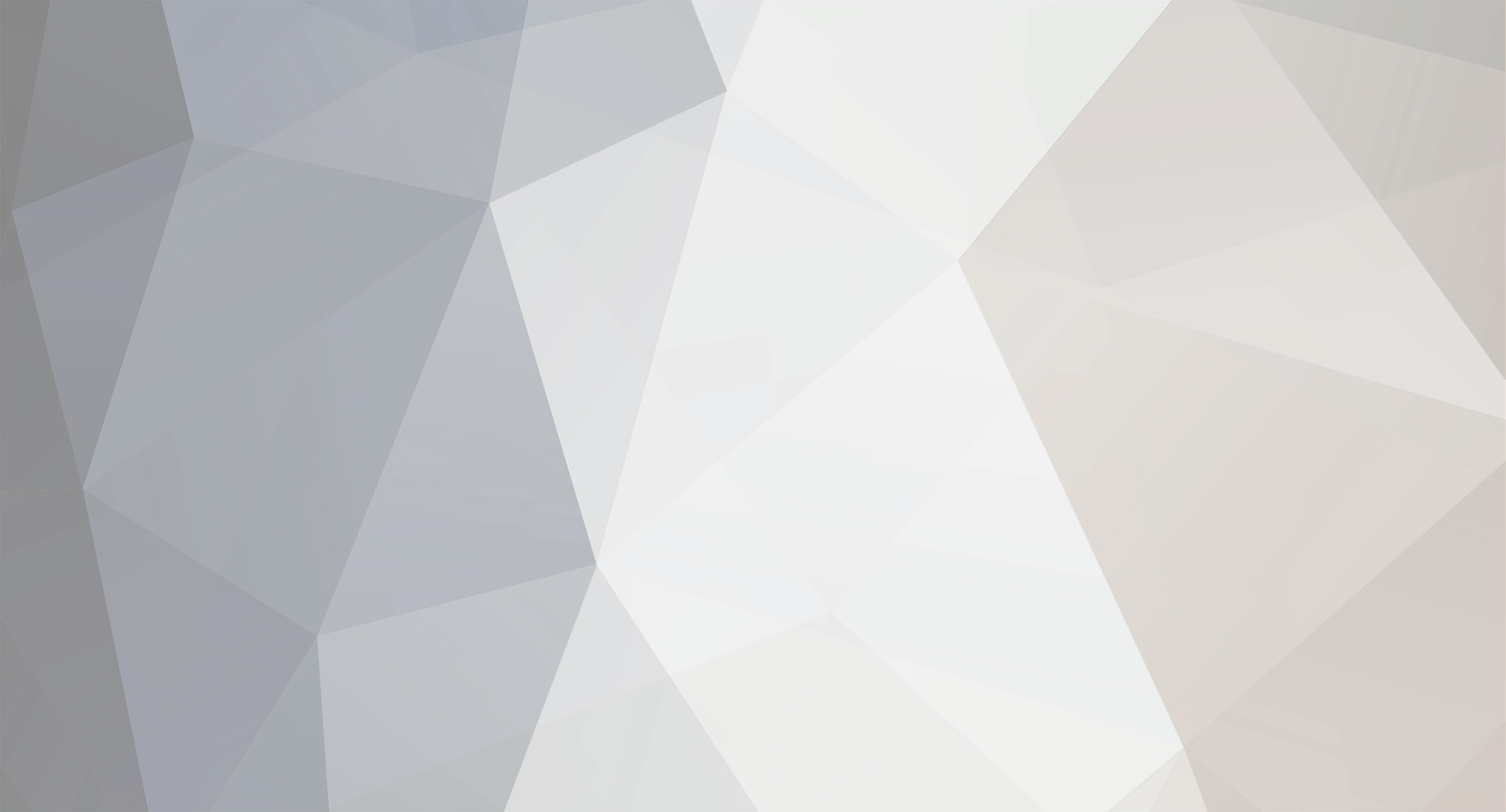
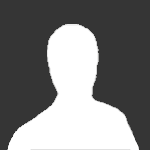
Gadroc
Members-
Posts
1060 -
Joined
-
Last visited
-
Days Won
1
Content Type
Profiles
Forums
Events
Everything posted by Gadroc
-
I'd be interested.
-
Caution panel is finished! Here it is all lit up and purtie! Here is the nasty rat's nest inside. Now I need to get access to that CNC machine and get my consoles cutout so I can mount it up.
-
LOL. I knew that would be coming up ;P. Yea I have a bunch of fixes about ready to go out the door. I delayed them to get BS2 working. This last past weekend I had earmarked time to work on BS2... but unfortunately my downloads where corrupted and I had to redownload which made me miss my "productive time" window.
-
Added link in OP to my sketch up files. Will post up my corel draw files for caution panel and electric power panel tonight.
-
Upload your profile on the SCSimulations forums and I'll look into creating a background image for you.
-
The paint was not wet to the touch but it probably was not fully dry. I put 4 coats on about 45 mins apart and then had about 2 hours to dry after last coat. There was some dust but not much. I did pull the trigger on the upgraded controller for the laser cutter. The export for engrave was crash moshidraw and I'm tired of remembering to fiddling with the manual power control before each cut. New controller can do engrave and cut in one job as well as digitally control the laser power. New parts have shipped today... whee.
-
I got the caution panel finished from a fabrication stand point last night. Here is the backplate after painting. And here is the faceplate after painting and then after engraving. And finally here it is with a few indicators lit. Sorry it's a little fuzzy. I'll try and retake one tonight, but it's hard to get my phone to focus on the lit areas. Tonight I have to solder another 32 LEDs and mount the Phidgets board on the standoffs.
-
Agggh... Getting paint down in all those crevasses = not fun!
-
Caution Panel Next up is working on my caution panel. Again many thanks to pibldr for inspiring me. I've drawn up my own panel this time, but the green acrylic and design are cribbed from his posts. Here you can see the parts I've cut out to make it. Top Left - Backplate which holds the LEDs, bolts the panel to the console and bolts the standoffs that hold the electronics. 1/16th Black Translucent Acrylic Top Middle - Light grid spacer. This gives some distance from the LEDs and the diffuser panel to help get a bigger lighted area. 1/8th Black Translucent Acrylic Top Right - Diffuser bezel. This surrounds the diffuser panel preventing light leak. 1/16th Black Translucent Acrylic Bottom Left - Diffuser panel. Diffuses the LED light from a point light so the full text can be read. 1/16th White Translucent Acrylic Bottom Middle - Indicator Grid. This lets me align the indicators better as well as helps stop light leak between indicators. 1/16th Black Translucent Acrylic Bottom Right- Bezel and Indicators Light Plates. Surrounds the grid and brings the bezel up to the same height as the indicator. Indicator Light plates will be engraved with the indicator text. Bezel - 1/8th Black Acrylic, Indicators - 1/8th Green Transparent Acrylic Step 1 - Glue Diffuser plate into diffuser bezel. Step 2 - Glue grid onto diffuser Step 3 & 4 - Glue Bezel onto of diffuser bezel and grid and glue indicators into grid. Glue spacer onto backplate. Once the glue dries I will mask off the backplate/spacer and paint the interior silver to act as a reflector for the LEDs to shine through the diffuser and indicator. I will also paint the indicator/bezel piece black and then engrave the indicator text through the black paint. Hopefully I'll be able to get that done this evening after work.
-
Another quick laser cutter update. I noticed last night that the panels where not coming out square. The upper edge of a square was offset to the left. I took a closer look and sure enough the X arm was angled so the laser cutter was closer to the front when moved all the way to the left. I pulled the whole x/y gantry out and finally figured out what was wonky. There are belts on both sides of the Y movement and when they but the bracket on the right side they screwed up the belt. It was two or three teeth off from the left side which pulled the right side of the X arm towards the front of the machine. I disassembled that side and got it straightened out. Again for those considering the cheap laser make sure you're ready to fix little things like this.
-
CNC machines make a mess and lasers make a smell ;). When a CNC router is cutting it chips through the material just like a saw and showers the area with dust / chips. Laser melts through the material but has fumes instead of dust/chips. Check out some of oakes videos on cutting out gauges with his CNC machine. CNC machines can not do inner corners as well as laser cutters. They can never cut a sharp angle as their cutting bit is round so inside corners will always be radius of your bit. Your cut depth is limited by your bit width (wider the bit the deeper it can cut) so to get tighter corners you are going to make many shallow passes with a small bit. Lasers do not suffer from this problem. In general the laser engraver is simpler for a few reasons. First it's only 2 dimensional in most cases while cutting. Second because the laser doesn't exert any force / pressure / tension on the actual piece being cut you don't have to worry as much about fixing the piece down or generating tabs so inner cut outs don't jam the machine. I personally have not tried to engrave panels using a CNC machine but the common things I've heard are people being happier with the results from a laser. Things that are harder to do with a Laser: Accurate 3D relief or pocket cuts where you want to have a nice shape cut out x depth but not all the way through. Example you want to gut a gauge plate with a lip on it. You can do the g-code and use the right cutting bit on CNC machine, where on a laser you would have a really hard time dialing in the power and engrave to git a nice smooth pocket cut out.
-
Kurt, Few consumer / desktop engravers run off of g-code, although all of them can be converted to do so by replacing their control boards with a Mach3 compatible one. Epilog and other name brands come with software that plugs in to Corel Draw or works as a printer driver. For the higher end ones the software will cut or engrave based on color and line thickness in the drawing. The lower end ones like I have are much simpler and you either engrave a bitmap image or export vectors from Corel Draw to cut. In general the laser engraver is simpler for a few reasons. First it's only 2 dimensional in most cases while cutting. Second because the laser doesn't exert any force / pressure / tension on the actual piece being cut you don't have to worry as much about fixing the piece down or generating tabs so inner cut outs don't jam the machine.
-
You need to create background graphic for the CDU that has a transparent window where the CDU screen can show through. My profile was made before it was possible to export the CDU screen.
-
Helios does work with the latest DCS A-10C patch, except for the radio controls which are broken in patch 1.1.9. Helios functions on Triggers and Actions. Triggers are raised when things happen in the simulations like altitude changes or when you touch a control on the Helios screen. Actions allow you to change the state of either the simulations, send a key or change the state of a Helios control. The input tab shows you the triggers which are "bound" to actions that affect the currently selected item. The output tab shows you the actions which are "bound" to triggers that the currently selected item can raise. For example lets take the "0" button on the CDU. if you select the zero button you should see in the output tab all the triggers it raises. Pressed - Raised when the users finger is on the touch screen. Released - Raised when the users finger is lifted from the touch screen. Closed - Raised when the button is "closed" or "on". (Used with toggle buttons) Open - Raised when the button is "opened" or "off". (Used with toggle buttons) If you want to have Helios push the CDU 0 button in game when you press the "0" button in Helios you open the actions list and find the press 0 button action under DCS A-10C -> CDU and drag it onto the pressed trigger. Then repeat that for the released trigger. Hope that helps get you started.
-
Awesome! Good luck on your adventure to become a professional pilot. Afraid I'm probably not going beyond sims in the basement. Thanks again for sharing your work with the community it's definitely allowing me to move much faster on my pit.
-
I've been toiling away in both improving my laser cutter and figuring out the right process for making my panels. Thanks every so much to pitbldr for sharing his hard work on the panel layouts. First up a status on the laser cutter. I've got it working pretty well now. A couple things to keep in mind if your going for a cheap one line like this. It essentially didn't come with a cutting bed. It came with a worthless clamp system which was only good for tiny pieces. I pulled out the existing bed and mounted a set of rails for a new bed. I then made a new cutting bed out of some anodized aluminum sheet cut in a lincane pattern and some .5" c channel aluminum. I'm going to order a sheet of .5" honeycomb aluminum shortly to make it even better. I also cut out a set of shims which go under the bed which allows me to adjust for the focus length and the depth of the piece. This setup is good for me right now as I only deal with 1/4", 3/16", 1/8" and 1/16" acrylic. I just have the bed itself set for 1/4" and have a set of 1/8" and 1/16" shims which let me raise i up for the other depth pieces. I am planning on home to get it setup for a motorized lift for the bed. With the bed in place I have a cutting area of 300mm wide by 190mm tall. The cast acrylic I got cut beautifully and I had no problem engraving the Rowmark Lasermax for the panel tops, but I was having a hell of a time cutting the lasermax. It would always flame up unless I used a cut speed so fast that the cuts got really rough. I went out and got a air brush compressor ($90) and rigged up a quick air assist. Currently I don't really have a nozzle (waiting for them to come back into stock) so the air is not really strong, but it's enough to keep the laser mark from flaming up to bad and I can cut it at a reasonable rate. This brings the total up on the laser to about $900 which is still about half anything else so I'm very happy. I'm probably going to retro fit the controller withe one of digital controllers which cost me another $700 (have to get stepper drivers as well with it) even after that I'll be about half the cost of other comparable models. If you are not up for this type of tweaking and hacking I'd tell people to take a look at full spectrum engineerings deluxe hobby laser. It is what mine after upgrades would be equivalent to. On to actual pit building. I have build my first panel and I'm pretty happy. In this first picture you see the reflector / light plate. This mounts onto of the back/switch plate. I don't have a picture of it but I painted the inside of this plate silver to reflect more light through the diffuser and engraved top plate. The trick I've found so far to get even lighting is to have this 1/8" air gap between the LEDs and reflector and the diffuser which create a light box effect and evens out the light. Next up is the completed panel minus switch plate (switch plate didn't fit after fixing my laser focus I needed to widen a few holes and have not re-cut it yet). On top of the reflector plate is a 1/16" white acrylic diffuser panel and then the engraved top plate which is 1/16th lasermax black/white. This was my first attempt at raster engraving and I'll be able to improve on the text now with better laser focus and knowing how to tweak the settings after more test cuts. Finally here it is with backlighting on in the dark. I had to remove the 1/8" green I had in before as it cut down the light a little to much, but I am ordering some 1/16" green transparent. I'm on the hunt for some 1/32" green transparent cast acrylic, if anyone knows of a decent priced supplier in the US let me know. This green will go between the diffuser and the lasermax to tint the backlight like an NVIS filter. I'm damn happy with the results so far.
-
Couldn't pass up a panel with a buy it now less than the value of the switches in the panel. Assumed you weren't getting it as you had already posted a response when I hit e-bay.
-
I got my acrylic in today and started some test cuts and immediately noticed that the exhaust fan that comes with the machine is not up to the task. Ran out to the local home improvement store and picked up a $30 70CFM bathroom fan and constructed a quick shroud to hook it up. Easily 3 times the airflow and I'm not going to kill myself with fumes anymore. I did use vent tape to seal up the fan housing as well so all airflow heads outside. I'm still fiddling with cut speed and power. At 5ma and 8mm tool speed I get a good cut on 1/16 cast acrylic but the edges are a little rough, but that might be the lower quality steppers. If anyone has recommendations on how to dial in cutting speed and power let me know. Next up is figuring out the engraving for the lettering. I've got 1/16 rowmax to try out next.
-
Excellent. Can't wait to see it come together.
-
Got CorelDraw installed and linked into MoshiDraw and it works even better! Moshidraw rasters EVERYTHING which means a long cut process for a simple rectangle. When you're using CorelDraw you can export as a PLT file which will to a vector cut or export as BMP if you're engraving text or other graphics. I should get my shipment of acrylic tomorrow and I can start figuring out the right power settings and making stuff.
-
Day 1.5 - Success. The software works under windows XP.... much fun to come.
-
Laser Engraver Day 1 - Having software issues. Every time I try to output something MoshiDraw errors out. it will drive the engraver no problem, but only to cut out the outline of the page. I've seen some posts about it having problems under windows 7 I'm installing XP on the engraving computer. Hopefully that solves the problem. Might have to resort to a 3rd party controller card sooner than I had hoped if that does not work. I was expecting the software to suck so not a big surprise.
-
That is just awesome. Can't wait to see some video of it in full action! :pilotfly:
-
Dimebug, My laser engraver got here yesterday. Mechanically it looks fine, very very well packed for shipping. Box, in a box and about 4" of bubble wrap which took me about a half hour to unpack. As expected some of the quality is not great (exhaust fan not a great fit and doesn't duct fully, but I'm going to cut an 1/8" plate between it and the cutter to seal it just to the opening in the cutter body. What setup are you guys using? Every time I try and output to the laser it errors out with "data conversion error". I was able to click fixed position and cut out the outline of the drawing and the machine itself worked perfect (albeit just cutting plain white paper).
-
I've got the first round of Kink's worked out on my IO controller. The EOS Bus Interface shield is now functional. It boots up scans the EOS bus for active controller boards, polls them for input and relays commands to them. You see in the video EOS Interface shield on top of an arduino UNO and a bread board version of the gauge controller board. The shield is designed to be able to stack three bus interfaces onto one host arduino. The host is being driven by a command line utility for the time being, but will be integrated into Helios. The gauge controller board is a bare bones arduino which handles the backlighting and alpha/numeric displays and controls an easy driver board to run the stepper motor. Right now I'm using an arduino to prototype but the gauge board itself will be slightly smaller than the arduino board and be self contained.