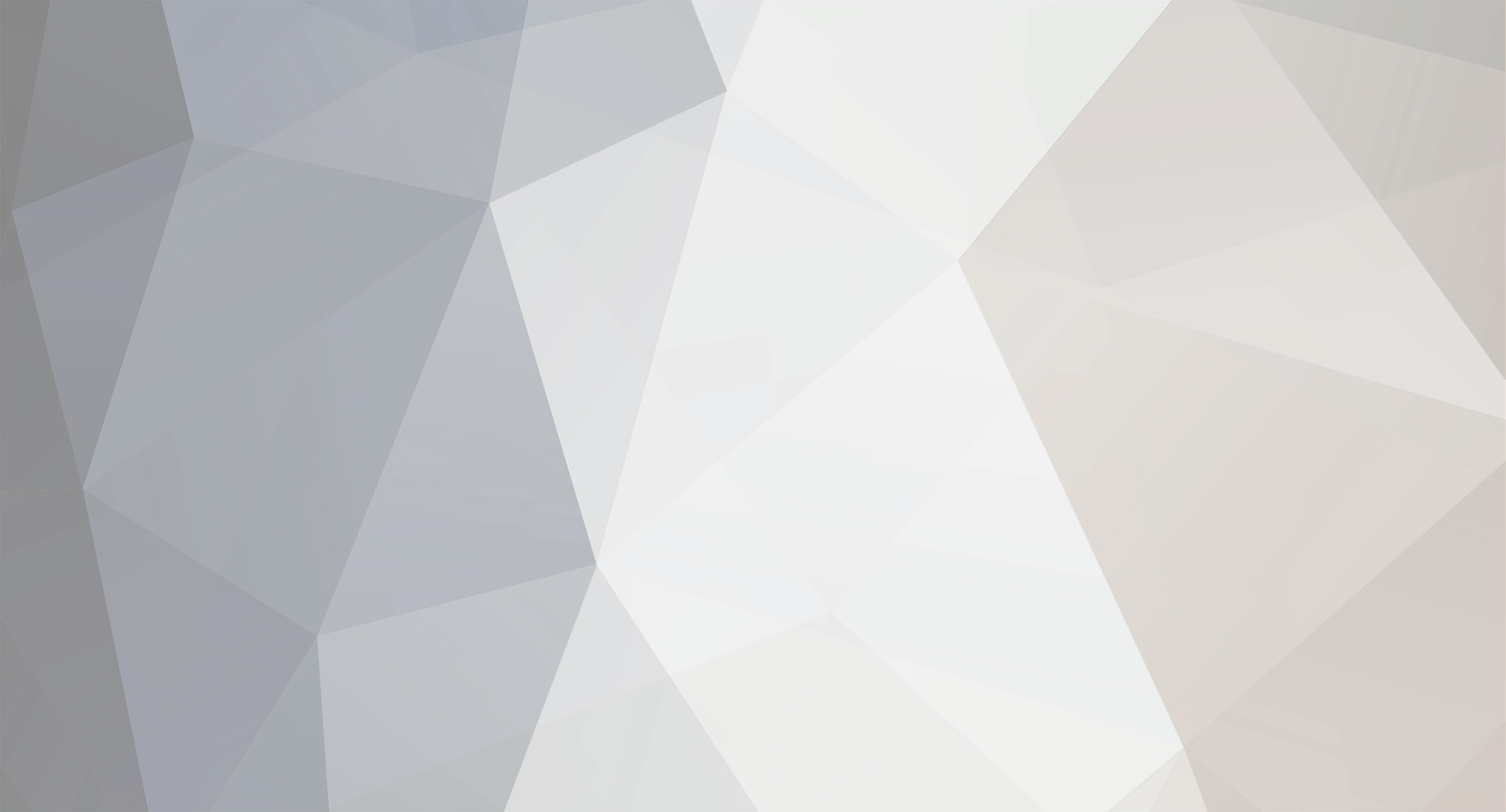
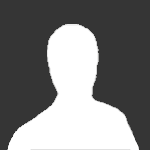
Feed
Members-
Posts
322 -
Joined
-
Last visited
Content Type
Profiles
Forums
Events
Everything posted by Feed
-
Depending on what the bottom is like, you could make new holes. Is there a mounting plate on the bottom you can get to?
-
I'll be doing some pestering of my own, I'm sure. And yes, I'll be keeping good notes!!! :D I have only just begun poking around with this stuff. The basics seem reasonably easy, but I'm sure going to be leaning on folks around here for getting this stuff all talking to each other and working to control the sim.
-
Okay, I think I'm done with my basic testing of the OC cards ... today I figured out the last piece of the puzzle, how to hook up rotary encoders and get them talking like I want them to. It was a little fiddlesome getting them to register just one increment at a time, but I got it. With news that the new stick is supposed to be arriving today, I can start making final measurements and laying out permanent panels (or at least permanent until I start trying to add backlighting and that sort of fun stuff). I figure I'll make an order for more knobs from Allied (thanks Rocketeer!), and this thing might actually start taking shape. I suppose it needs a paint job before too much longer, too. HWhheeee!
-
See, that's the kind of thinking I need - glue before you cut - simple! :) That panel looks good - I am thinking more and more that I need my own mill!
-
I haven't taken it apart yet, but they appear to be VERY close to the knobs on a real panel I just picked up for parts. The ones I have are push on-push off, and turn like pots, as well. If only the push on-push off function is useful in-game, that makes things simpler.
-
Ambitious, but workable, I'd imagine - are you one of these folks with your own CNC? nvrmind - I see that you are! I only wonder if it would be easier to cut the buttons out of a single sheet, instead of having to weld all those little buttons together.
-
There's a few different ways to do backlighting, and it's really too big a topic to address in a single note. Commonly, real aircraft panels have a metal plate where the switches (and backlighting, whether that;s LEDs, EL film, or standard lamps, are mounted. Then a translucent layer is on top of that, and the lights illuminate this layer, while there are openings for switch tops, etc. Then that translucent layer is painted/enameled/whatever - covered with an opaque coating. Lettering/lines are then etched through this final layer, letting the illuminated, translucent material show through. I have absolutely NO experience with backlighting, so I'm probably not a great source of information on DIY backlighting ... but there are lots of threads around here that have information about how folks have done it. Good luck! :)
-
OpenCockpits no longer supports the use of a parallel port direct connect, anyway ... not saying it's impossible, just that their manual assumes you're using a USB expansion. If you're asking about the little connection cards they offer, the answer is no, you do not need them. You can use an old 40-pin IDE hard drive cable, and wire that to terminal blocks, modular jacks, D-sub connectors, or directly to your switches (be sure!). The cards they offer are a nice tidy solution to make wiring easier, but they are not the only option.
-
Absolutely fantastic ... I guess I'll just have to bite the bullet and buy, then cast as many as I actually need. I guess I'm just lazy ... AND cheap. :)
-
I believe the toggle in your picture is a standard on-on SPDT mini toggle switch. That type has 2 positions, either of which can be "on" - it's very versatile. It's somewhat smaller than standard toggle switches, but still usable. I have a bunch of that size as well, but did decide to go with several of the somewhat larger, standard toggles. The width of all the individual panels will be 5.75 inches wide, and with the mounting rails, the width of each side area (2 panel widths + a little due to the rails) will be very close to 12 inches. I'm SURE there is better information in some of the other posts, but that's very close to the real thing. Keep us posted!
-
I agree 100% with Triggerhappy. Two points I might add - For the panels that switches and buttons are actually mounted in, thickness is a consideration, since the switch/button posts are only so long, which is one reason acrylic sheet makes a good choice. I might suggest stealing a page from Rocketeer and mocking up the panels in cardboard first, or masonite (fiberboard), which is what I'm doing - that way, when you discover you've done something wrong (which is almost guaranteed to happen), it's no big deal. Once I get everything working the way I want it to, I may start the transition to sheet metal, acrylic, backlighting, etc. I personally wouldn't worry about specific part numbers. If you go with OpenCockpits cards, the highest electrical current you'll have to deal with is 5V DC at around 20mA ... that's less current than a typical model railroad layout. Most standard toggle switches are designed to handle far beyond that. Like Triggerhappy, I've been having good luck finding switches on eBay. He may have better specific stores to point you toward since he's closer (I'm in the US). In general, the more you can buy at once, the cheaper it is per unit, so plan ahead! As far as start to finish on the OC cards, the USB Expansion and one Master Card are what you'll need to get started with the most basic stuff (exactly what Triggerhappy advised). Depending on your wants as things progress, you'll be able to add other cards for additional functionality. One Master Card though, will give you 72 inputs, and 38 outputs (usually used for individual LED indicators). One USB Expansion card (needed for interfacing the Master Card) will accept up to 4 Master Cards, and has 4 inputs for potentiometer input. By the time you're ready to add more, you'll have an understanding of SIOC, and will know what you'd like to add next. I can't wait to see how yours starts to come together!
-
IMHO, OpenCockpits is the way to go. Input & Output, extremely versatile ... a little more complicated to work with, but I think the flexibility and integration is worth it. Of course, I'm just getting started, too.
-
Rocketeer - VERY NICE!!! I'm jealous that you're so far ahead of me, but I believe we'll end up taking much the same path (functional over form). Would you tell me where you decided to get the knobs? I have been ordering from various sources on ebay, and I'm happy with a few knows I have, but the 'right' knobs are always more than I want to pay. It's looking very, very good.
-
HA HA HA HA HA!!! Congratulations on finding a very lovely box, and the beginning of your 'pit! Welcome to the insanity. I got started the same way, dropping about $100 on PVC and just started putting things together. That was about 3 months ago ... Have you chosen an interface yet?
-
hog_driver, I'd suggest it's important to decide what you plan on doing right up front. Leo's boards are great input devices, but they will not let you do any kind of ourput. If you have *any* plans to add functioning indicator lights, panel readouts, or anything of that sort, I'd choose a platform capable of that right from the start. Once that decision is made, almost regardless of which card you choose (Leo's, OpenCockpits, EPIC, Hagstrom, or most others), you'll most likely be fine with any off-the-shelf switch you're likely to find. Unless you're trying to interface REAL aircraft components, the most current you're likely to encounter is 5 volts at around 20 milliamps. Configuring the software interface that will make the simulator react to that switch the way you want it to is an entirely different challenge, and you'll have to know how your interface works. If you wire up a standard toggle switch to a hacked joystick, or one of Leo's cards, then what the computer is going to see is a joystick button, either turned off (joystick button not pressed) or on (joystick button is pressed - and held down until the switch is flipped off again). Only you know your budget, but do as much research and planning as you can, before starting to build. Take it from me - I bought a Hagstrom KE-USB108, convinced that I'd thought it through. It IS a fantastic and capable card that is well worth the money - if it suits the plan. Since I want to have indicators and readouts (outputs), I wish I'd just gone 100% OpenCockpits from the beginning. Rocketeer - I'd be interested in a copy of that spreadsheet as well. I don't know that relying on the simulator functionality is the best course, but it's certainly a good place to start. There's also the manual (for both the simulator and the real thing - I know the A-10A manual is posted here somewhere). A few other (minor?) points - Leo's cards AFAIK are not key emulators - rather than recording keystrokes, they're recognized by Windows as joysticks, so you'll assign simulator commands to joystick buttons. Hagstrom offers a few choices, some of which offer keystroke emulation, joystick buttons, etc. The OpenCockpits stuff is very capable at a relatively low cost, but it is significantly more complicated to set up. It all depends on what you plan to do. very minor ... Cat5 is 8 leads, not 7. :) Both Deadman and Rocketeer, as well as most other folks around here - are extremely helpful and have great advice/ideas. As a newbie around here, I'm impressed and thankful.
-
While that would certainly be the way to do it RIGHT, I've done this type of casting and it works well enough without the need for any sort of special equipment, especially for such a simple shape. Would I be afraid it might break in a real cockpit - yes. Is it going to cause a problem in your homebuilt simulator? Highly unlikely. As with anything, you can demand absolute perfection, or you can accept trade-offs for money, time, and effort. What's the saying? "Fast, cheap or easy - pick two." :)
-
I've seen the caster gear lever - and agree that it's a good, simple, cheap approach, if it's satisfactory for the builder (which is really all that matters). My suggestion for resin casting is simply due to the fact that this part in particular looks like it would be extremely easy to manage. @Oakes - I suppose it depends on what one considers expensive. You'll need material to make the mold, which could be latex rubber, plaster, or almost anything else that wouldn't react/adhere to the casting resin. The resin itself is mixed with a hardening catalyst and poured into the mold. If I remember correctly (it's been a while), a liter of casting resin and bottle of catalyst cost me less than $20. Latex can be had for around $10 a bottle, and plaster is cheap. The main concerns are the ratio of catalyst to resin, and the thickness of the mold, which affects curing time. If anyone had the actual handle, a mold could be made of the actual part, which would be super-cool.
-
Indeed, Deadman - I was in fact referring to your post. I should have been more clear in saying they're JUST lamp covers as you indicated, and I was just trying to additionally clarify that they have no other function - which appears to be the case. :)
-
It looks like to me the plan was to cut them horizontally across the top and bottom, but that the left and right edges would all overlap, requiring rather significant areas be filled in and smoothed out. I'm suggesting instead to make vertical cuts so that the left and right edges of each dish is a line, and butt them edge-to edge, using the cut off sides as stiffeners on the backside of the top and bottom edges. Either way, it's a fantastic idea, and I look forward to seeing how it turns out!
-
As a newbie, I may be naive, but shouldn't this be a fairly simple part to create using some aluminum stock (carefully bent) and casting resin? Am I correct that the small round protrusions (from the clear handle) are simply lamp covers, and not a button with some other purpose? I would cast the two halves in resin and use a single bolt to join both halves to each other (capturing 2 LEDs within) while also affixing the handle to the lever. I was eyeing caster wheels at Lowe's today that looked about the right size - maybe built up using some clay to make the mold? ... just a theory.
-
Niiiiiiiiiice! Oh, if mine end up half as neat and tidy, I'll be happy.
-
Yeah ... $34 seems a bit steep, to me - but wire up all your switches to that, and use a simple 40-pin ribbon cable between that and your Master Card, and there you have it. The more I think about it, the more I like it, especially for those of us not building individual panels, but larger modules with a bunch of switches and buttons mounted into a single unit. Could make things very easy, indeed.
-
Thanks for that link, Deadman - I've seen a lot of your posts already, and I think it's fantastic that there's so much experience and helpful folks around here. I feel a little bit like I'm talking to celebrities as I make contact with folks that are so much further along than I am. I never intended this to go as far as it has, but it's certainly addicting. I'll have to check out Nigel's thread in more depth - with just a quick scan, I'm just in awe - like so many of the super-realistic pits folks have made. I wrestled quite a bit with how to do the wiring - DB plugs, terminal blocks, etc. Once I realized I had the RJ stuff laying around, that made it easy. You're right though - that stuff ain't cheap. I'd certainly say that unless you're REAL sure you won't be moving your pit, EVER, that you'll be glad to have some sort of disconnect - I wouldn't wire directly from the OC card to the switch, but that is me - I suppose that when it comes right down to it, the 40-pin connector on the Master Card might be all you really needed - especially if you're keeping the cable runs short. As far as the cards themselves, each Master Card can take 72 inputs, which means 288 total for a single USB expansion. I did a quick, rough count of the number needed for just the panels I've mocked up (printed a paper face to play with) and came up with at least 107, which I estimate to be about half the controls in the cockpit (but I've been wrong more than once). And again, it was a real rough estimate, figuring 2 inputs for every rotary encoder, 1 input for every on/off toggle, 2 inputs for every 3-position toggle, and 2 inputs for every rotary selector switch (which I know will end up being a low estimate, since several of those are 4- or 5- position selectors). It seems like you could save inputs on the OC cards by using some binary logic, but I'm not sure it's worth the trouble. I'll be playing with that possibility at some point, exploring the trade-offs. I think that I'd want to find a way to multi-task some of those inputs before adding a second USB Expansion - but there's no telling. I've basically promised myself I won't order any more OC cards until I get at least one switch actually functioning. :) Ok ... I think I'm gonna go peruse Nigel's thread for a while, and learn me some more good stuff (not to mention making me jealous of yet another sweet set-up). LOL
-
Definitely look forward to exchanging notes - lots of helpful folks with lots of experience around here. I'd originally chosen the Hagstrom card due to it's ability to manage toggles & latching pushbuttons right from jump. I also liked the fact that it can send joystick buttons and mouse clicks. I knew I'd want to go with some OC stuff as well, for some outputs like indicator lights, but the more I experiment, read, and learn, the more I wish I'd just gone exclusively OC from the start. It's just far more versatile. I'm sure ED will add the ability to assign keyboard commands to most (probably not all) important functions in DCS - there's just too many folks who won't be building anything close to a home cockpit - they included the 'arcade mode', after all. Really, I'm just glad to see someone coming out with hard-core simulations again. It's been far too long.
-
I'm planning on running UTP from panel groups straight to RJ-45 plugs, and using JR-45 jacks with punchdown blocks wired to the Master Cards. This is where I'm lucky, as I happen to have quite a few of those things laying around already. I figure that also lets me skip the little connection boards they offer. I'm using old IDE hard drive cables to go from the 40-pin sockets on the Master Card to the punchdown blocks. I tried to plug a MasterCard directly into the USB Exp but I don't recall that actually fitting. I ended up making a short DB25 link. While I certainly expect to need more than one Master Card, do you really think I'll need more than one USB Expansion?? One of those can take 4 Master Cards, and I don't expect I'll need MORE than that!?? Is there something I'm not thinking about?