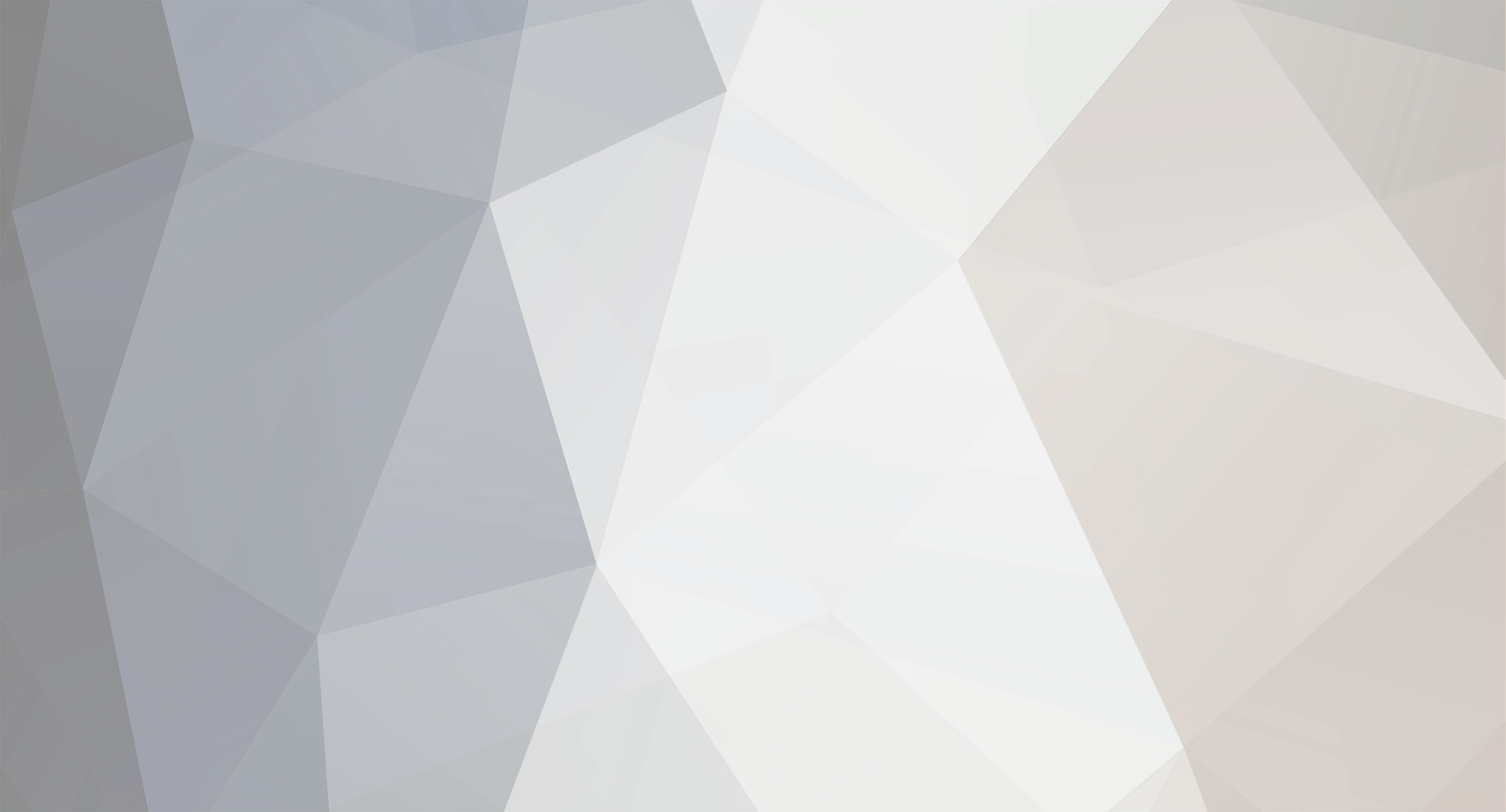
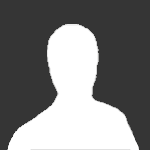
Gadroc
Members-
Posts
1060 -
Joined
-
Last visited
-
Days Won
1
Content Type
Profiles
Forums
Events
Everything posted by Gadroc
-
Nice job on the video.
-
Ok. Doing more planning on my cockpit electronics and took a minute to spin through all the panels and figure out how many inputs/outputs of each type they will need. I posted up a big table here as I thought others might find it useful. Also I got some temporary bezels on for the MFDs. I'm debating on when I'm going to design my own to maximize screen real-estate as well as square off the inner corners some. They will always have the larger bezel plater around them to hide the monitor as I surface mounted it as close to the MFDs as possible in order to make sure they where not to deep. Got DCS World 1.2.2 downloaded and OS reinstalled last night. Should be able to fly tonight.
-
Yep. That's a rough number but close enough. To get an accurate measure I'd have to disassemble the entire mechanism, which I'm not will to do.
-
Dropship, Those dimensions are fairly close. You can find the measurements I took from the real thing here.
-
I've posted up the drawings from my landing gear panel. You can find them here.
-
Very cool!
-
I wired up the ejection handles and seat arming lever tonight. Here is the inside of the left console where you can see the wire runs and the switches which detect the handle being pull and the seat arming lever being placed down. And here is the seat in place with the handles installed. I also got the front panel risers glued on and then the front panels screwed in place. I'm not ready to start working on CP panels. The last items for structure is getting my rails in place. I'm going to be using 1/8" C channel aluminum. I'll be setting up a jig so I can drill holes every .375" so I can tap the holes as necessary once I get each panel done.
-
Thanks. I'll try it out for a bit, but I'll check your thread for the dimensions. I'm pretty sure I have that post bookmarked as I used some of the pictures / measurements when I was redoing the side panels. I have not attached the outer trim or ejection handles yet. Tonight I'll try and get them done. I needed to get some more screws as well as the springs for the ejection handles. Also let me know if you run across and air speed indicator for the A-10. The one I have is the wrong casing and goes up to 600 knots instead of 500. I may just steal the need from it and build my own faceplate and bezel. Craig
-
Panels, consoles creadet by 3D printers?
Gadroc replied to JaBoG32_Prinzartus's topic in Home Cockpits
Not that I'm aware of. If you need that do mold of your 3d printed object and then pour one with a clear resin would be what you need to do. I believe that. For me I'd be more inclined to print than learning to use all the appropriate milling tools. There is a lot more finishing work to make a 3D print be final quality though, but it's work I'm capable of doing. -
I got the seat back from Flim a while ago. I believe it is a vacuum formed seat back from a real ACES II but I'm not positive.
-
I got most of the parts cleaned and assembled tonight. Here is the rudder floor and seat cradle. Cradle still needs a few parts cut (back brace and some spacers to make it easier to center the seat. Here is all the new parts I cut (minus CP risers as they need to be glued on). Here is the pit in place for dry fitting. Finally here is a closer images of the cp with risers and dry fitting my instruments. Tomorrow night I need to drill one more hole in the CP (Misplace one bolt hole for the landing gear panel, but not a big deal.), glue up the risers and finally mount the TV. I may try and drop .5" to and 1" in height on the seat after I fly a few times. The throttle seemed to be a little bit of a stretch but not bad. Have to try it out a few time.
-
Ouch.. I just hit a hold down screw when I didn't zero in the x axis properly.
-
Wheee... I've got parts... Well I got everything cut out for the pit, but only was able to assemble a little bit. CNC always takes a lot longer than you expect. You think you've got everything down and then your at the machine and realize you missed a part... or forgot a tool path... then you break a bit... sigh. That being said I'm very very happy. The CP came out great and looks to be plenty strong. I need to clean it up by filing down the rough edges and clearing out some of the plugs. Here is a shot of the front panel along with the three risers sitting on the bench. My gauges fit perfect (gotta love CAD)! I also reconfigured how the LCD holes are cut. I realized I didn't have enough ribbon cable to make it to the back of the panel. I'll be making some brackets to hang the VGA controllers closer to the screens. Now here is a shot of the partially assembled CP. I also got my seat pan together along with the seat back.
-
Panels, consoles creadet by 3D printers?
Gadroc replied to JaBoG32_Prinzartus's topic in Home Cockpits
Subtractive is more cost effective for a skilled machinist with the right tools. Creating something in sketch up an printing it is much much more accessible to many more folks. -
Panels, consoles creadet by 3D printers?
Gadroc replied to JaBoG32_Prinzartus's topic in Home Cockpits
3D printing will undoubtably be helpful, but not for making full panels. I can think of a few uses though. 1) printing a knob you don't have access to, usually to cast for a mold. 2) brackets to hold panel components (PCBs, LCD displays, etc) 3) custom gears and ratchet assemblies for unique moving parts (a-10 refuel lever, gearing for a custom joystick gimbal, etc) -
Might not get it posted until tomorrow. Scrambling to get some things ready to go the CNC shop tonight. I did do a quick 3D cad drawing of the crystal and will do the handle next. Once I get them in I need to arrange them on a drawing so they make sense which will take a few minutes.
-
I have one sitting here. I will take some pictures today and post them up.
-
Yes. I have a pair of them I use over my 10" screens. It works well but keep in mind they are resistive screens which take pressure to register. Also you'll need to fix them good to the screen so them don't move are flex up and down. Dragging is harder on these than optical touch screens. Also they use the touch kit controller, which emulates a mouse and does not show up as a touch screen to windows. At one point they had a driver that registered as a touch screen, but I have looked for a new one in a while. It's a good driver though and has lots of options to support multiple screens.
-
Back at it again... whoo! Wow. It's been a long time since I've had something to post to this thread, but I finally had some vacation time this week. I spent a good deal of it in front of the computer. First I'm planning on upgrading my cmc laser. I'm going to upgrade it to a 16" x 24" cutting table along with motorized z axis as well as a much better gantry and drive configuration. This should also allow me to create jigs to make buttons and other multistep engraved items much easier to align. I'm following the buildlog 2.x laser plans and adding 40mm to the X axis so I can put in a full 12x24 sheet of acrylic so I don't have to cut them down before using anymore. I've ordered all the parts except the skin material and should be assembling it next weekend. Second I've done a LOT of CAD work for my pit this week and I'm finally read to cut the rest of the pit out this weekend. Here is a shot of the stand alone CP. I've merged some of Dimebug's designs with yk2iah's to fit my needs. I'm cutting the front panel out of 1/2" birch plywood, but if it's not strong enough I've found some HDPE plastic I'll order to recut it. Here you can see some of the individual components as well. The pit breaks down into 6 pieces (left console, right console, rudder floor, seat cradle, ejection seat and center console). Ohh... and I also designed out working ejection handles and seat arming lever with embedded limit switches. Just need to head down to the hardware store and get a few springs. Once I get this cut and installed I'll be able to go back to working on software and panels. Can't wait to actually be able to fly again. I have high hopes I'll be flying by the end of the weekend (depending on the wife letting me spend all day tomorrow down at the shop on the CNC). If not I'll be back in the saddle by the end of the week.
-
Also try checking out the forums over at hover control. There are several helicopter pit builders over there as well.
-
Thanks Mike. Saved me a trip across town to check the dimensions!
-
Help needet ... HELIOS and potiometer on hardware panels
Gadroc replied to TomDK's topic in Home Cockpits
That is correct. For those controls you would need to use a rotary encoder. -
Helios, Phidgets LEDs and brightness
Gadroc replied to JG14_Smil's topic in PC Hardware and Related Software
I'll have to refresh my memory on this and try and replicate it. PM sent to e-mail me your profile. -
Help needet ... HELIOS and potiometer on hardware panels
Gadroc replied to TomDK's topic in Home Cockpits
Drag the set lighting action from the A-10C to slider changes as you have. The trick is that direct x supplies 0-65536 and the game expect 0-1. Just change the binding vallue from trigger value to lua script and use: return TriggerValue/65536 -
Yea it's definitely nice chip and I started with that one for the first prototypes of my EOS boards. I moved over to pure on/off using a MCP23018 plus limit resistors for indicators (about 1/10th the cost of a 5940 for use cases with out dimming) and PWM direct to a transistor power circuit for back lighting.