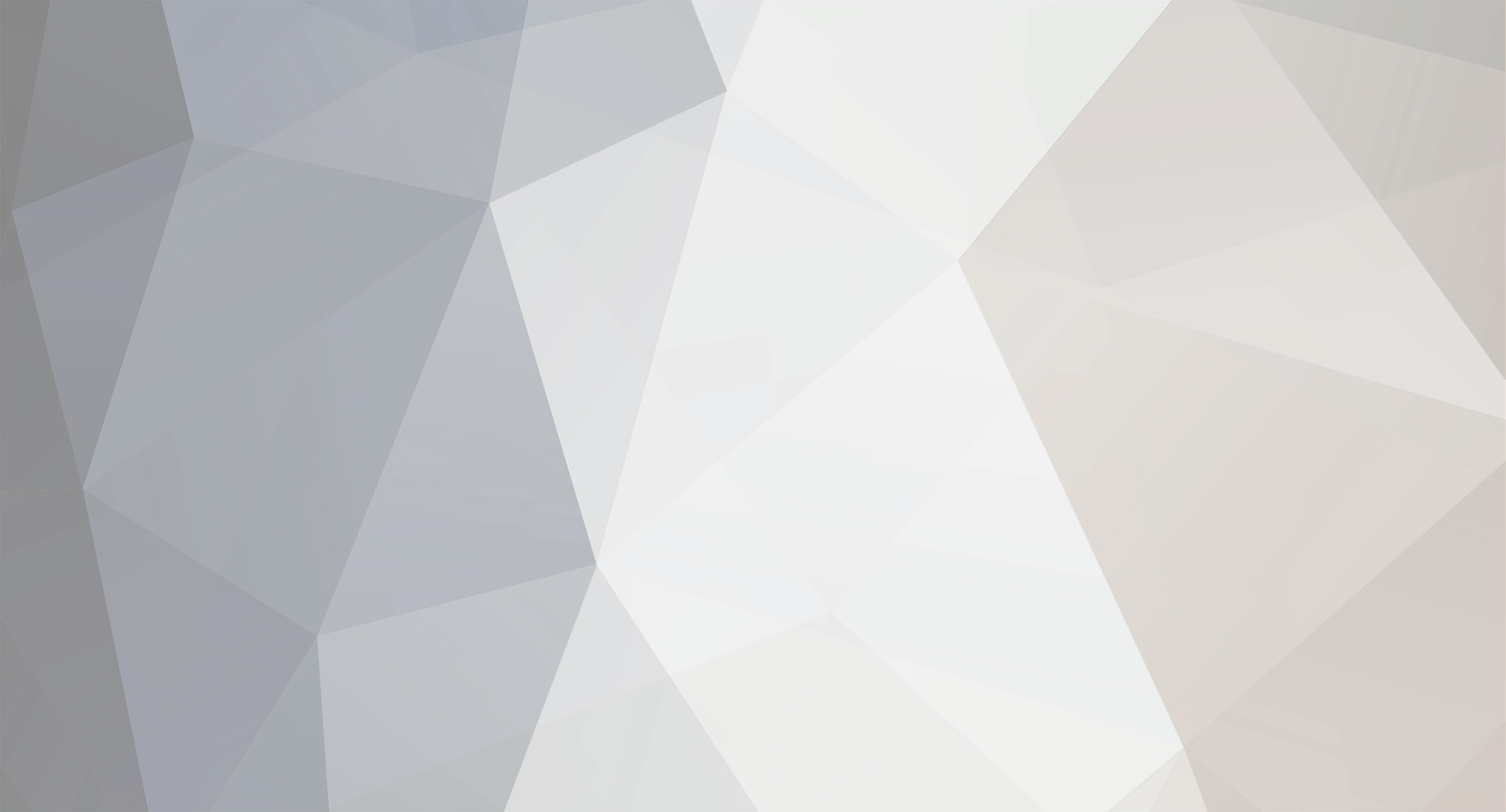
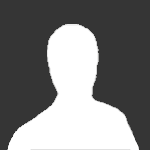
Gadroc
Members-
Posts
1060 -
Joined
-
Last visited
-
Days Won
1
Content Type
Profiles
Forums
Events
Everything posted by Gadroc
-
I'd highly recommend checking out this thread. Short answers from me. I think Laser is the tool I'd pick if I could only have just one. You can build a lot of things out of flat acrylic sheets once you understand the build process. I got my K40 machine for $750 delivered. You'll spend $800 more to make that a serviceable machine. With a $900 + $800 price your are close to some of those smaller import machines that metalnwood points out. I'd take a close look at them.
-
Linden has probably hit it on the head. They imported the DXF in mm instead of in inches which would cause it to be 25.4 times too small. They should just be able to open the DXF and specify inches during import.
-
@BlueIcaro - That's what I was referring to with the 5V. A teensy or arduino will require a shield or other circuit board or some other wiring to supply power to the servos directly instead of through the arduino power regulator. Which is why I pointed out the Pololu. It's $30 to drive all twelve servos, where as the open cockpit is $30 for 6 servos. Once you add the power circuit board to deal with the arduino/teensy power distribution it's going to cost more than the pololu. If you build in bulk (at least 50 boards) you could build a custom ardunio board to match that cost albeit you'll have to solder. @hegykc - Would you mind sharing your gear design? I'd like to try it out on my laser.
-
Doh! That's a bummer. Hope you mend fast!
-
Yes you can do this. You need to change the binding to lua script instead of trigger value and use string.format like below. return string.formate("%s", TriggerValue) Just replace %s with the appropriate formatting specifiers. You can find the formatting specifiers here.
-
Looks good. Have you tackled how your going to do the concentric shafts for the dual pointers?
-
Also you should look at the Pololu Mini Maestro 12. It would run all twelve servos with just a 5v power source.
-
Ahhh.. didn't see that. It glanced over it because of the french right before it in the parenthesis. Might want to look into an "access denied" page instead of "file not found" page in this scenario.
-
Both the instructions and software download links on your page give 404 errors. Thanks in advance for sharing!
-
These look really good. I'm assuming from the pictures you are gearing up servos 2:1. Have you tested this? If so how is the positional accuracy? Also are you laser cutting your own gears or are you buying them? I'm debating on stepper vs servo for my engine cluster. I have about 20 or so 400 step nema 17 motors waiting to do it, but I have to get drivers for each of them ($10-$15 each). Servo's are attractive as I can do one board to drive them all, but looking into it each servo is going to be $8-15 for a digital servo and I'll need two gear for each which will run $10-15. The bonus of steppers is I can direct drive the needle with just a custom shaft coupler. The arduino comes with a servo library which can drive 12 servos. Keep in mind you will need to supply the +5V directly through the power supply on the servos. If you try to draw that current through the teensy or arduino you'll blow it's power regulator. I have not attempted to set this up, but it should be a trivial circuit.
-
New toggles are next on my list. I have already cut the new switch plate I need to unmount the current panel and transfer over the wiring. Unfortunately that means soldering as the NKK switches are solder lugs instead of screw terminals. The flaps gauges is fully my work. I used paulrk's photo on page 18 of this thread as a reference. I'll be posting up the full DXF files for my gauge.
-
Wee progress! I finished my flaps indicator today. It's setup using a sub-micro servo. The lighting on it is not that great, but workable. I have two led's projecting behind the flaps and symbol. They also front light the needle and rule. The flaps is very uneven, but the rule is nicely lit which is the important part anyways. For Helios crew I did find a bug in the phidgets servo where it was not properly saving your servo type. I'll be posting a new Helios version sometime this weekend with the fix.
-
He has mounted the side projectors both inside and out. I think he said it was easier inside and they are in a position you rarely look at when flying the A-10.
-
Need to add big fans in the back wall and vents in the bottom black areas for cooling.
-
You know... my pit budget would be so much more reasonable if Flim would quit doing crap like this!
-
Also I have to send a big thanks out to PeterP! He's spent a lot of time on this and spent plenty of time via Skype with Flim and myself explaining his process and formulas.
-
Bingo. Also it allows you to manage lighting as well.
-
How are you building the light holders for the engine gauges? Are you 3D printing that? It looks like it has angles you couldn't do with laser cutters.
-
Flim and I are working on adjusting things to work in a 7' cube for easier build and fit. It will require some modifications to our pits to sit lower. An 8' cube is easier for projector placement and pit building, but is just a tad to large to fit into a normal sized US room. A 7' cube could fit in most US bedrooms / basements. 3 projectors would mean you loose the top view.
-
Looking great!
-
-
Yep... I'll get one posted up in a little bit.
-
The foot print of the pit on the floor is 56" front to back and 53.375" right to left. The ACES needs about 6" min clearance behind the pit floor foot print. Eye point in the pit is roughly 16" from the rear of the pit floor outline and 55" up from the floor. I can make an 8ft x 8ft cube work but I can't go any taller than 80".
-
Here is my "ideal feature list" * High Performance * Easy to use GUI * Support for separate refresh rate per screen * Src/Target rectangle support just like SoftTH * Allow multiple target rectangles per monitor * Support "interlaced" updates of destination target areas (ex: Setup the CDU to only update at 2 frames per second to the target display) * Support scaling of dest to target rectangle * Profile switching via Hot Key. All DCS World aircraft share the same exe and it would be nice to switch config via hot key instead of having to exit game and change config. * Plug-in API which would allow rendering directly to target monitors via a DirectX surface. I would love to write the Helios rendering engine as a plug-in to this.
-
CNC laser versus milling machine - A newbie's quest
Gadroc replied to wolfster's topic in Home Cockpits
Do the math as well... I have a great maker space available to me and at $35 per hour it's dirt cheap. If you have perfect plans and just need to cut once its great. But you do need to figure in time to experiment and learn how you want to do panels. I still opted to get my own as I break even in less than 100 hours of cut time. With engraving you can easily be an hour per panel. Not to mention the fun factor of having one. In my case the K-40 was always a stepping stone. For me it was the same price as buying a tube and powesupply. I used it till I was able to spent the rest to build the larger machine. Building my own has been great. I've learned way more about CNC and how a laser engraver works. Aligning and other maintenance activities are much easier now. In addition I have a 40w machine with a 12x24 cutting area for a great price. This path is not for everyone and you have to be willing to put in the mechanical elbow grease to get it tuned up.