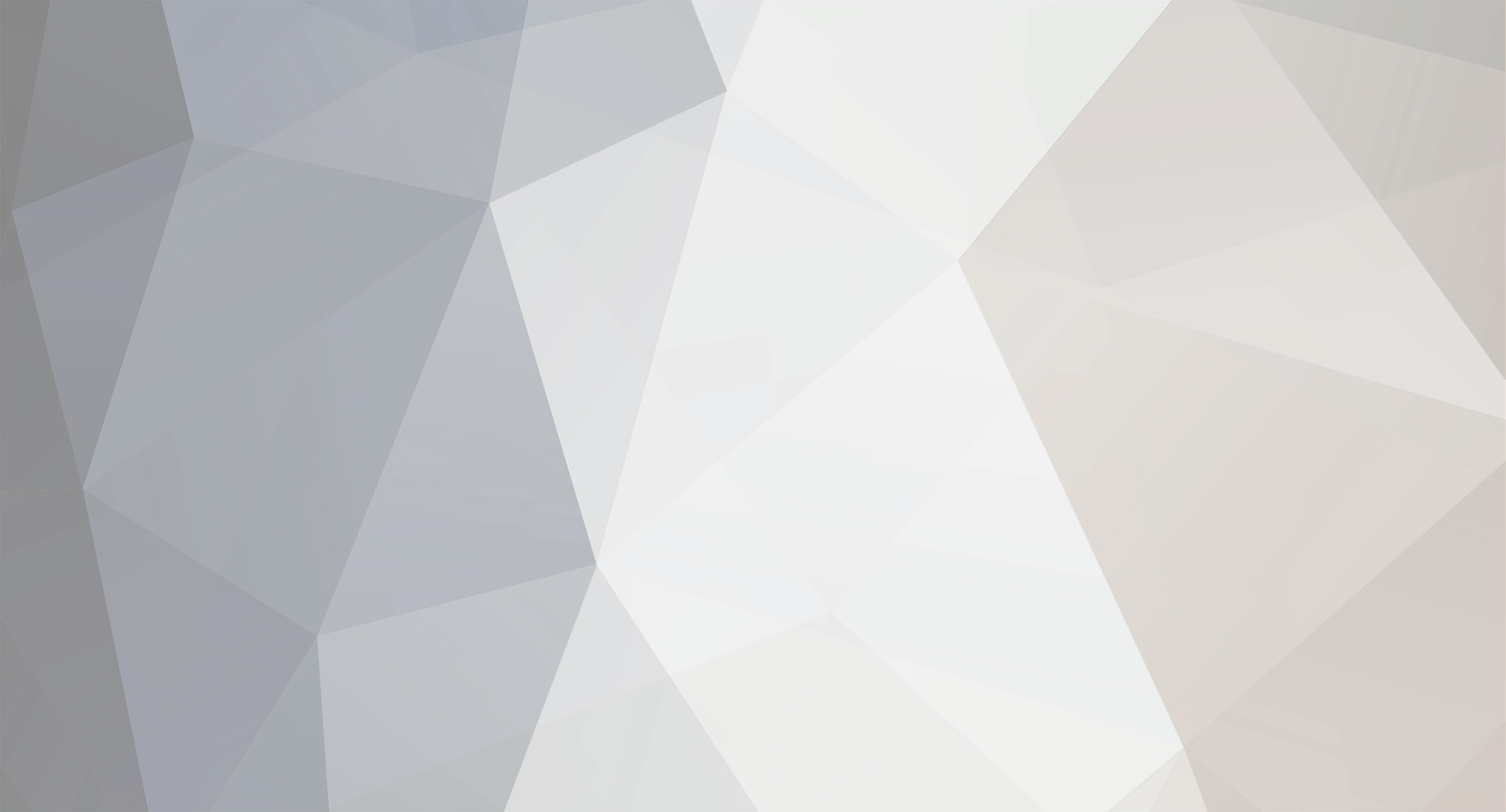
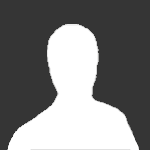
CubPilot
Members-
Posts
212 -
Joined
-
Last visited
Content Type
Profiles
Forums
Events
Everything posted by CubPilot
-
Thanks, but just for the record, it isn't a real life, to scale pit. It just fits the space I have available. It started life to hold the TM MFD units with the video screens mounted behind them. Then I started adding things. It progresses with thinking, "I might as well add this..... might as well add that" ................ I think this is how building a full cockpit starts! Never been a machinist in the professional sense of the word, but I have been exposed to it on a basic level. Hopefully I had enough exposure to keep all my digits intact. No engineering degree either. I got the chair on sale about a year ago at Staples (USA). It is comfortable but it does swivel which isn't ideal with rudder pedals, but still usable. I may try to do something about the swivel feature in the future. The armrests might go or be modified if I decide to mount the throttle to the chair, it needs to go somewhere other than where it is now. :pilotfly:
-
Nice work Gadroc! :thumbup:
-
Thanks. I have seen similar approaches using PVC pipe in other posts on the web. However, if my joystick mount to the PVC works out as planned, that will be something I can call my own. Yep, PVC pipe/fittings can come in handy for some things, I'm thinking this is one of them. After I get the design finalized (still considering the hinged joystick...... :lol:) it will get a bit of black paint to increase the stealth factor. :smilewink: :pilotfly:
-
Hmmmm....... with a bit of refrigeration....... that works for me too. Now there's something that the real A-10 doesn't have! :megalol: :pilotfly:
-
Yep, going for some authenticity, every A-10C seat has a piddle pack or two. :D :pilotfly:
-
Joystick / Chair Mounting I have taken a break on the instrument panel work due to real world stuff, but I have begun working on joystick placement. I had the joystick sitting on the pull out keyboard shelf. This is far from ideal. The joystick is too high to be used comfortably and the joystick base has to hang off the edge of the shelf so that full forward stick movements do not hit the instrument panel - :joystick:. The throttle is also on the keyboard shelf and it also hangs off the self for the same reasons as the joystick. I thought I would like to have a center mounted joystick attached to my desk chair. Others have done similar things, this is my version, a work in progress still needing some fine tuning. I was wandering through Lowe's the other day and decided to look in the plumbing section to see what I could come up with. Shown above, beginning at top left to right: 2" diameter x2ft PVC Schedule 40 pipe (Lowe's #256099) PVC Vent Elbow (Lowe's #23349) 2" PVC Drain (Lowe's #253242) 2" PVC Offset Drain (Lowe's #253214) The offset drain is a perfect match for the diameter of the Warthog joystick base (the round part). I began by making a wood attachment for the chair to mount the PVC parts to. The picture shown above shows the attachment. The view is looking at the bottom of the chair, the front of the chair is towards the bottom of the picture. The aluminum tabs are attached to the wood and then slide under the two front bolts that hold the chair to the chair's base. The above pic shows the whole thing. The horizontal board has a dado (groove) cut into it about 1/2 the thickness of the board, the vertical board fits into the dado and is glued and screwed. This makes a very stable arrangement to attach the PVC bits to. The horizontal board is also screwed to the front bottom edge of the seat for added support. I cut the drain flange off at the top of the drain so it would fit up tight against the horizontal board. A short piece of pipe connects the drain to the 90 degree elbow. Presently the joystick is clamped to the PVC. This is a view looking at the front of the chair. All the drain flange attachment screws are not installed. There will be a total of 7 screws. The vertical pipe pushes the front of the chair cushion in a bit and the offset drain positions the joystick perfectly for this chair without having to cut a notch in the chair seat or cut the chair seat leather. So, this is where I am at the moment. I took the stainless drain screen and gaskets off the offset drain as I won't be using them. The top offset drain, vertical pipe, and vertical part of the 90 degree elbow are not glued together yet. I can use screws to temporarily connect them together securely if needed for testing before gluing them. I need to fine tune the height a bit more and I am also considering a short joystick shaft extension which would have an effect on the PVC pipe length needed. My plans are to make a metal plate to attach to the joystick base, and another to attach to the PVC drain. These would be made so that the joystick can be detached easily to ease sitting & exiting the chair or when I don't need the joystick attached. Note: This is continued here.
-
I'm not sure VAC is better. I haven't used GC2 in quite awhile (I got the version with the labtech noise canceling mic). The mic works great, but when I found the original GC2 box it was minus the program disk & I can't find it. So it would be hard for me to make comparisons between the two. It appears that GC2 is no longer being updated (it's a Win95 thru Win2000 era program), so I tried VAC (free trial period w/full functionality), very reasonable price, and it did the job for me. It is also being improved by the author, so that's what I went with. If you already have GC2 & it does the job for you then by all means use it. There is nothing wrong in doing so. If not I recommend VAC. Seeing how you are using GC2 maybe you might want to try VAC & compare them. I don't remember enough about GC2 to do that. It would be good to know the +'s & -'s of each & how they measure up to each other. :pilotfly:
-
Thanks. I hope I gave you some ideas on at least one way to make some of this stuff. Feel free to pick, choose, or modify any of my methods so they might work for you and the tools you have to work with. Been taking a break from this for a bit. Been working with VAC (Voice Activated Control) for use with the AI command menus (for $18US this is a bargain! Very much like Game Commander, but is still being updated, even for Win7 64bit!). :thumbup: Also relocated the Track IR center button to the Warthog joystick pinkie lever using AutoHotKey (While still retaining the Warthog's plug & play with DCS A-10C). It was on the UFC keypad, but it wasn't the best place for it. I used AutoHotKey again to bind the Warthog throttle Comms switch "UP" position to act as a mike switch for the AI command menu, works pretty good. I can probably do the same for TARS or Teamspeak using the throttle switch "IN" position of the Comms switch. :pilotfly:
-
A how to guide to breathing new life into old Aces II seat cushions
CubPilot replied to TulsA-10's topic in Home Cockpits
This is another option, and if you get the 1" thick for your butt, the price is about the same as the yoga mat. It is good stuff! :pilotfly: -
Looking good TulsA-10! :thumbup: Give you a soldering iron and look what happens!:smilewink: :pilotfly:
-
Looking good Deathcobra. Hey, looks like you have my keypad............ I'm going to have to check to see if I still have mine! :smilewink: :pilotfly:
-
With any computer joystick extension it is best to be very conservative as far as how long the extension is. It doesn't matter what brand joystick you want to consider, they all could have problems with broken gimbals when adding the extra leverage of an extension. The gimbals (or other designs) were never designed to handle the extra leverage and disaster could rear its ugly head during spirited use. I don't say this to be-little what was done here, just wanted to make people aware of what could happen at the more extreme lengths of joystick extensions. :pilotfly:
-
Map HOTAS Warthog buttons w/o using TARGET! I have the UP Mic Switch mapped to turn on AI Comms menu without re-doing the DCS A-10C "plug & play" TM Warthog functionality with TARGET programming. I used AutoHotKey to accomplish this. I did the IA Comms button & Centering Track IR using this method. Also I use VAC (Voice Activated Control). If you remember Game Commander it is very similar, but is being updated, unlike GC which is not. I will make a new post about this (& link to it) later tonight, dinner calls. :pilotfly:
-
Sounds like a good system you have there Mr Burns. Coolermaster makes good cases IMHO. I have a CM Centurion Case with a water cooled i7 920 OC'ed to almost 4GHz, it does quite well running most any sim with the eye candy turned up. Enjoy your new rig! :thumbup: :pilotfly:
-
You better keep her, you are a very lucky man! :D
-
Well, you might be able to get some of the big sheets cut in pieces that are a bit bigger than what your finished size is for a component (inst panel, side panels, etc.). Then you could trim them to the finished size. If you have a circular saw & jig saw an aluminum cutting guide would keep the straight cuts straight. The guide is clamped to your workpiece and the base of the saw is run against the cutting guide. The guide will take a little work to get into the proper position, but it can be done. Of course the panels will need to be laid out on the material so you have finish lines to follow. The various dimensions would have to be planned ahead in order to do this. I used a Router for the MFD & keypad holes in my of my little desktop panel along with the cutting guide. The basic panel I started with was cut on a small contractors table saw (you can do the same with the Circular saw & cutting guide with careful setup of the guide). It would also help to have a good builders square to help keep things........ well..... square. Not having many tools to work with just makes it a bit harder to do some things and will add to the build time, but it is not impossible. :pilotfly:
-
Not sure how much the stores jettison and fire ext switches will be used (although at the moment I seem to take a lot of damage trying to take out targets). The fire ext kind of goes with the fire pull handles, it allows you to select which fire ext bottle to use (there are two). I have mine wired up only because I had the button room on Leo's USB board & I wired the fire ext handles. I have had damage to the LDG Gear a few times and had to land wheels up, good to use the Stores jettison button then................................. but I forgot to use it! :doh: In the end, what buttons are important is something each of us will need to determine for ourselves. I do think having the artwork looking more like the sim would be make it look much better IMHO. All my file needs is to be re-sized to fit the width of your panel. As far as your LDG Gear lever, I think it needs a longer bolt (the bolt should have a shoulder [ area of no threads] that the handle will pivot on), a Nylock nut (it has a bit of nylon in it to lock it to the bolt threads so it doesn't loosen with movement), a fender washer (much larger outside diameter than what you have now) to go under the nut & touching the handle, a spring that fits the bolt, and something that will act as a bearing between the handle & the MDF it is attached to (some plastic or a nylon washer maybe, the larger the outside diameter the better). Also screws would probably be better than the nails holding the switches, but if there is no movement of the switch bodies now then the nails are OK. Just some ideas to help you refine your LDG Gear Handle.
-
Mr. Burns......... Mr. Burns! Man I get busy, then come back to the forums and see this thread. You go man! Looking good. :thumbup: I posted a file in my thread with the graphics that I used for the Fire handles and the left & right parts. They are .png files (Photoshop or photo editing program as long as you can load & save .png files) and you are welcome to use them and re-size them for your pit if you want. Save them as .png files and re-sizing will not affect the quality. Change the width equally for each file, make sure that the height is locked to the width (aspect ratio) & print them out, tape them together and check them against the width of your panel. If it isn't right change the size until it is. :pilotfly:
-
Thanks. I had to think for a bit...... UC Lever...... UC Lever.......... ahaaaa........ Under Carriage Lever! :doh: You are from across the BIG Pond I assume?
-
You may have seen it in this thread earlier! :smilewink: The button is a Radio Shack item, the one with two in the package. One has a red button, the other a black button (I painted it red for the LDG Gear panel button). These don't take much force to push them in which I thought was better for me because the Inst Panel is not fastened down to the desk and the only G's I will be pulling will be virtual ones. The button guard in my handy work, dimensions my own. :pilotfly:
-
I won't tell anyone what you have been up to at work, if they ask .... :music_whistling:, that's all they are getting out of me. :lol: First off, my panel is as desktop unit, so it is not made to simulate the sizes of the real deal. It is also a mixture as far as being a close copy design wise (not so much dimension wise) of the A-10C inst panel. Some items I model reasonably well, like the LDG Light Switch. Other items aren't even close, like my UFC keyboard. I consider cost, time spent, what materials I already have on hand, the physical constraints my panel imposes on me, if a certain item sparks my interest to spend more time on, etc., when adding items to this project. There are threads on this forum which discuss the real dimensions of the A-10C cockpit. That's where to look for that stuff. I have attached a .zip file of the graphics I used for the glare shield. I got them from making screen shots from the sim using Track IR and then tweaking them in a Photoshop type program (I used Serif PhotoPlus X2). Because of cockpit shadows in the sim I needed to tweak the yellow markings to get them to be closer to the same shade, the shaded areas had an orange tint to them. It isn't perfect, but close enough for me. They are .png files and can be resized without losing quality. Be sure to keep the width & height proportions the same when resizing them and to save them using the highest quality settings. What I did was re-size each module equally (I changed the width settings as that was my main concern and checked "Maintain Aspect Ratio" in the software). I then taped them together, and held them up to my panel to check to see if the proportions were about right for the width of my main panel. The left and right modules were then printed and trimmed along the yellow dotted lines, this was then used as a template for the shape of the modules and placement of the switches/buttons. The modules are slight larger than the template (use a pencil to draw around the template, then cut out leaving the pencil line + a bit more for sanding to leave the line on the finished piece). This insures that the graphics will fit inside with a little room to spare. All I used from the Fire handle graphic was the Fire Handle part of it. The areas between the Handles needed to be wider to match the LED units I used for the flood lighting. Well, I hope this helps! You might be able to use these graphics and re-size them to the actual A-10C dimensions, or very close to it. :pilotfly: a10c_fire-bottle-stores_graphics.zip
-
Actually, the Weller soldering station I bought is a WESD51 with the Digital temp readout. It reads and controls the temperature of the tip on the iron same as yours. Very nice unit, and I got it at a reduced price with a rebate to boot! So far I'm happy with it. :thumbup: I'm not sure what tip it came with but I will check out the .64 conical tip. Where is a good place to find them reasonably priced (if that's possible)? Not sure about the uTube video. My still camera will do video, but it isn't very good. The lighting is much better looking than what the camera shows. It is a much more even lighting with out all the hot spots. For example in the last picture in my previous post there is not the green hot spot between the Laser Arm & TGP switches when viewing it with your Mk II eyeballs. The intensity does drop off with added distance from the light source, but the approximate same distance from the light source will appear to be the same brightness. There are shadows from the switch handles, but it still is very usable as far as seeing the switch markings. At the brighter settings anything that may be below the panel can be seen, like cockpit checklists for example. :pilotfly:
-
My Version of the Whelen Post Light First of all thanks for all your kind comments. TulsA-10, I do OK at soldering, but I haven't tackled the really small SMC connections as in a cell phone. I did the matrix PCB using a cheap Radio Shack iron, but since then found a real good deal on a Weller electronically controlled digital soldering station that I couldn't pass up. OK now on to the post light. This is a Whelen Post Light. It is made to be a replacement for one of the screws that hold aircraft instruments to the instrument panel. It uses an incandescent bulb. My version will use a very bright 12v 5050 SMD LED instead of the incandescent bulb and since there are no real aircraft instruments in my "computer" A-10C instrument panel the mounting will be a bit different. I found this neat 12v 5050 SMD LED that is mounted on a small, thin, flexible, pcb. The backside of the LED has double sided adhesive tape on it to attach it to any surface. It also has flat wires from the pcb that the "normal" wires are attached to. The wiring includes the proper size resistor for use with 12v DC. This is perfect for my needs as the other panel lighting LEDs are the same type with the same voltage requirements and I can add the post light LEDS to the same circuit so that they all are controlled via the Dimmer/ON-OFF unit . I bought the Whelen Post Light Caps for 0.48 cents each (black item to the right). Then made my own aluminum "post". I turned it to the proper dimensions so the hood would fit. Because I could not feed the LED wires through a hole (due to size of the resistor on the LED wiring and the diameter of the post), I elected to mill a slot down one side of the post for the LED ribbon wires. Shown above is the 5050 SMD LED stuck onto the end of the post with the flat ribbon wire positioned in the slot. This LED has three LED Diode lighting chips on it and outputs 5 times the brightness of a regular 5mm LED! This picture shows the ribbon wire and the slot more clearly. I used double sided tape to hold the ribbon wire to the bottom of the slot. The slot is deeper at the left so the ribbon wire will not get caught by the nut that fastens the post light to the instrument panel. Notice the raised portion at the right end of the post. The Cap has an indentation that will mate up with the raised part, thus holding the Cap on to the end of the post. A little bit of epoxy and the slot disappears. I was careful not to let the epoxy run over the sides of the slot. I let it set up some and then trimmed it flat across each side of the slot. After painting, the flat area will not be very noticeable because it will be out of view near the bottom side of the post. Notice the white material inside the post cap. It's reflective and will redirect the light of the LED down onto the panel. Above shows the back side of the post light. It is held by a "pal" nut (used as a jam nut in aviation in certain situations). I need to secure the wiring so the flat "wire" will not become damaged if the wire gets tugged on a bit. So, here is the Post Light mounted in the instrument panel illuminating the LDG Gear Switch Panel, the LED is at full brightness. The inside of the Post Light is not seen when in use, you see it here because of the camera angle. There is another Post Light above and to the left of the Flap Indicator (it is not a switch as some have thought). I will probably add a post light there to illuminate the lower part of this panel and LDG Gear Down lettering. Just for fun here's the UFC keyboard and AHCP panel with the LED flood lighting. It works pretty well and is very usable in the dark. Again, the LED units at the top at each side of the APU Fire Pull handle are seen due to camera angle, but are not seen in normal use. I'm going to redo the keypad key labeling with a black background (it's a medium dark gray color now) so it will show up better, more like the AHCP panel lettering All in all, I'm pretty happy with how this turned out! :thumbup: :pilotfly:
-
So, I unhooked the panel from the computer to tidy up a few things on the backside. This "wiring spaghetti", an example of wiring gone wild, will never do! It invites trouble with wires getting caught on something and being pulled out of the connectors. The wires are as long as they are so they are long enough to be able to make changes to the connections to make it all work correctly. Now, this is much better! The wiring is more controlled and I can actually see the connector markings now. If I were to make the USB button break out board again I think I would have had the connectors at the back turned 180 degrees like the middle connectors are. It would make connecting the switch/button wires much easier. :doh: I have about 5 more button/switch connections left plus the four hat connections. The wiring going towards the right goes to the LDG Gear, Taxi/LDG Light and the other items there. This is a broader view of the back of the panel. It is clamped to the 2x4 so it's level, which makes it easier to work on & prevents it from tipping over. I would not want to break the monitor screens. I dropped one on the floor while taking them apart earlier in the build..... the results were not good.... had to order a new one. I had to move the USB hub to the right side (partially hidden by the clamp) when I added the AHCP switch panel below the keypad (green PCB at the upper middle), there wasn't room for both the AHCP panel & the USB hub there. To the left you can see Leo's USB PCB on top of the Rudder DB15 breakout PCB. The USB cable connection is pointed towards you, the rudder DB15 connector is pointed to the left. The white item attached to the left side of the left monitor is the ON/OFF/Dimmer for the LED flood lighting. I just reach around the right side of the panel (from the front) to access the control knob to adjust the LED brightness or turn them On or OFF. These are very bright 12v 5050 SMD LEDS. Each LED has three lighting chips in it, so you get three times the brightness in that configuration. I found another cool 5050 SMD LED item and I plan to use it to make a LED post light to put over the LDG Gear Panel to illuminate it. It will be added onto to the LED wiring already there and will be able to be dimmed with the others. I think I can make it work, we will see. :pilotfly:
-
Groovy Game Gear makes a USB card very similar to Leo's. :pilotfly: