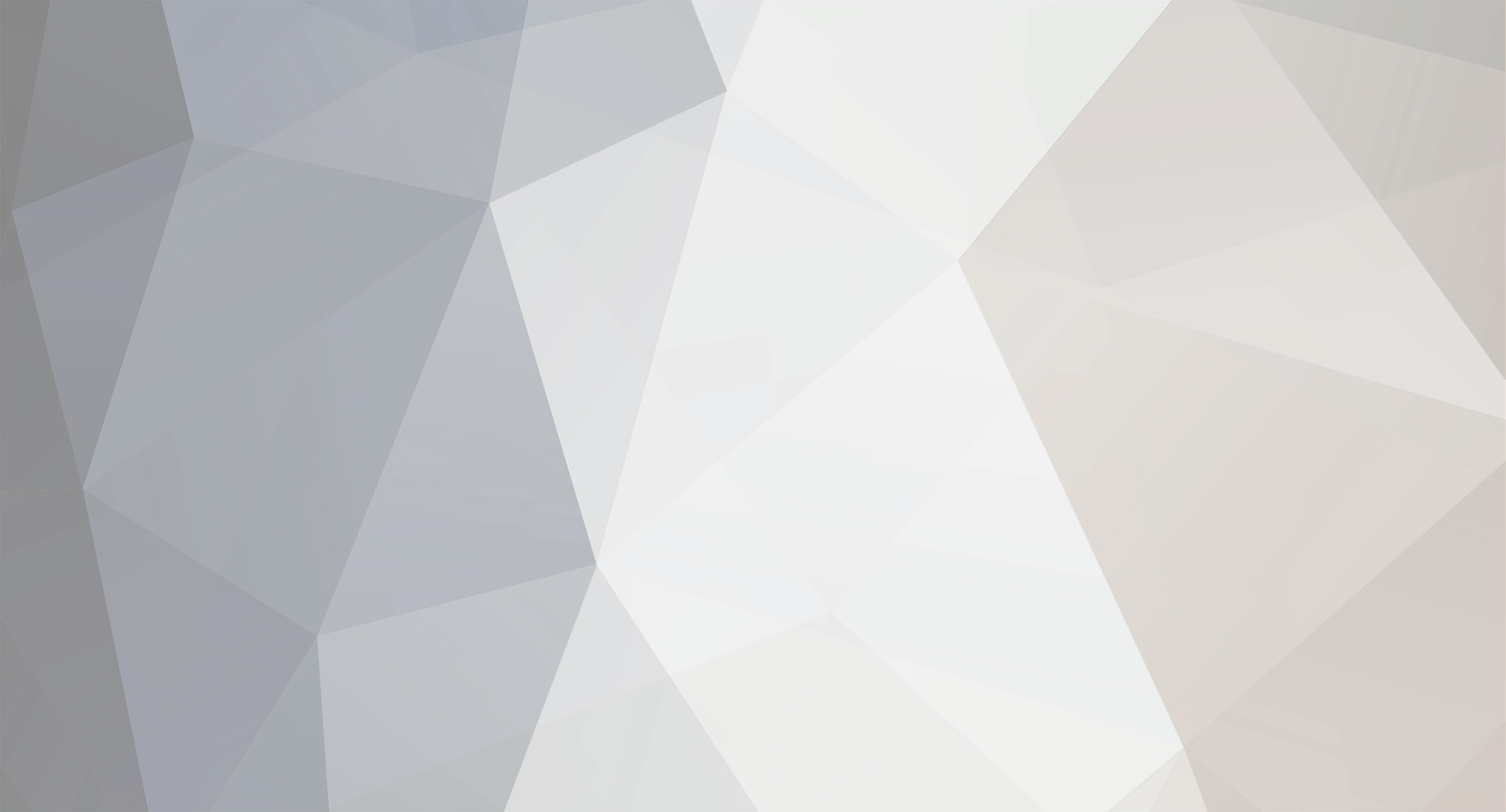
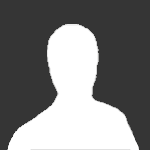
CubPilot
Members-
Posts
212 -
Joined
-
Last visited
Content Type
Profiles
Forums
Events
Everything posted by CubPilot
-
Same here Latest update changed the shortcut to open the sim, I don't know what it changed it to. I can't open the sim. My antivirus (Avira)went nuts and Q'ed about 16048 files! I'm guessing that's about the whole download, didn't use Torrent. I saw this tagged to some of the files in this update I did on 2/14/2020: Name HEUR Date Discovered Mar 2, 2018 Type Malware. The rest were marked suspicious. :no_sad: DCS is out of my reach. :cry_2:
-
There are a few things. I think that the earlier poster did a good job with his chair Joystick mount, but the joystick is a bit too tall for my tastes. I designed my mount to be as sturdy as it could be using this material and mounting it on an office chair (still haven't done anything about locking the swivel). First, I suggest using Schedule 40 PVC drain pipe, it has a thick wall. I used 2-3/8" to 2-1/2'' outside diameter pipe (whatever the standard size that fits the fittings). Also, I kept the pipe lengths as short as I could as shown below. The shorter the lengths of pipe the sturdier /less flexing there will be. I also used hardwood, about 3/4" thick, it holds the screws better than soft wood & you don't need much (be sure to pre-drill any holes needed for screws, etc.). A lot of the info about what fittings I used I believe is still there back further in this thread. I found that a shower drain matched the diameter of the Warthog's joystick base perfectly, so that is what I used. It comes as a kit, the bottom drain, rubber gasket, and the top of the drain which you would see in use And screws into the bottom part of the drain. The top, what the Warthogs base is attached to, is threaded to fit into the drain base, the part of the drain that you don't see when using this stuff for its intended use. There are two flavors of shower drains, an offset style, which is what I used and one that is not offset. This gives you some choices about what works for you the best. The offset drain can be used as I have it or turned 180 degrees to take a little bit further away from you, more choices. Most of the details have been covered in the previous posts on this subject. Notice how short the pipe is between the flange fitting and the 90 degree elbow, no flexing there. Also I looked for a fitting that had a thick flange (touching the wood), again thinking about strength, thicker is better. The vertical wood piece fits into a dado on the horizontal wood piece, it's a tight fit, glued and screwed. That is not moving either. To the right you can see a piece of 1/16" aluminum that attaches to the wood and then to the front bolts of the chair/base, the second attachment is not shown. To the left notice the small screw going up into the front of the chair, there three sheet rock screws holding the front of the bracket. This is the only pipe joint which I glued. The vertical joints are held in by three sheet metal screws (pre-drill the holes). Why do this? So i could experiment with different joystick heights with out making the whole joystick mount over again. I may just leave the screws in there, never know when I might change my mind about it. Also note that you can move the dado fore and aft if you plan ahead. This would allow you to keep the horizontal fittings/pipe as short as I have it, but there are limits, no more that about 1/2" from either end of the horizontal board. Notice that I cut the flange flat so the round part of the horizontal fitting fits up against the wood, just some more insurance against flexing / movement. Originally the vertical wood piece was as wide as the top piece of wood. I trimmed the bottom of the vertical wood piece as shown so that I would not hit sharp edges with my legs if I were to tuck them under the chair. Been thinking about how to lock the Joystick to the PVC so it doesn't turn. I think if I cut one side vertically through the threads in the bottom half of shower drain I can then attach two 90 degree brackets with which I can attach to the drain (on each side of the vertical cut) & tighten the thread up on the mating part with the joystick screwed to it using a screw through the 90 degree brackets. Now about the second question you had about an extension. Raising the whole joystick higher will not do anything to alter the sensitivity of the joystick for helicopters, AA refueling, etc. Only a joystick extension between the joystick base & the joystick handle will do it. Keep in mind, the longer the joystick shaft the more leverage, and hence force, that you can very easily impart to the plastic gimbal parts in your Warthog base, to the point of breaking something in there. Also, the longer the joystick shaft, the more movement you will get measured at the top of the joystick. It could come to the point that you would hit your body (or desk, instrument panel, etc.) before you had full travel in your joystick! I know these examples are extreme cases, but just wanted to highlight them a bit to get you thinking about this stuff. I think Metalwood suggested to limit extensions to about 3 to 4 inches. If he is still around you might ask him what he thinks & maybe how longer ones held up. Cheers
-
What size of monitor are you using?
CubPilot replied to bunraku's topic in PC Hardware and Related Software
Old monitor: Samsung 214T 21" New monitor: BenQ XL2730Z 27" WQHD 2560x1440 @144Hz w/FreeSync What a difference! -
Add TrackIR Center & Pause on 1 Joystick button
CubPilot replied to CubPilot's topic in PC Hardware and Related Software
Are you talking about the AutoHotkey Track IR Center/Pause info? This thread went into other items & using similar solutions to those first posted. Are you saying if you use TARGET for your Mig 21 profile, Autohotkey doesn't work? More specific info about the problem you are having would be helpful. -CubPilot :pilotfly: -
Thrustmaster Warthog hotas no command works
CubPilot replied to lorfar's topic in PC Hardware and Related Software
Well this is going to be a bugger to fix I guess. There is a program called USBDeview that lets you view all installed/connected USB devices on your system here at http://www.nirsoft.net/ It also lets you reset any old entries that may have been connected (my Cougar HOTAS has not been connected to my computer for ages, but there is a reference to it in my system that this software still sees). I know that the Cougar had a similar problem sometimes and deleting/resetting old references to it in this program fixed it. Plugging in the Cougar after the reset just created new USB port info that worked. Just be careful, it's a powerful program. Another thing it could be is a bad solder connection somewhere in the Warthog. I assume this had worked at one point because you would probably have sent it back to TM. You should contact TM if you haven't already. -
Thrustmaster Warthog hotas no command works
CubPilot replied to lorfar's topic in PC Hardware and Related Software
Well this is going to be a bugger to fix I guess. There is a program called USBDeview that lets you view all installed/connected USB devices, as well as all USB devices that you previously used on your system. Go here at http://www.nirsoft.net/ It also lets you reset any old entries that may have been connected (my Cougar HOTAS has not been connected to my computer for ages, but there is a reference to it in my system that this software still sees). I know that the Cougar had a similar problem sometimes and deleting/resetting old references to it in this program fixed it. Plugging in the Cougar after the reset just created new USB port info that worked. Just be careful, it's a powerful program. Another thing it could be is a bad solder connection somewhere in the Warthog or a bad USB cable. I assume this had worked at one point because you would probably have sent it back to TM. You should contact TM if you haven't already. -
Thrustmaster Warthog hotas no command works
CubPilot replied to lorfar's topic in PC Hardware and Related Software
Is this a new Warthog HOTAS or a used one? Install the latest TM Warthog HOTAS drivers. Be sure to connect the USB to a powered USB port or directly to your computer (not a un-powered USB HUB for instance). - Be sure that the two HOTAS Warthog components are installed correctly and appear as standard "HID-compliant game controller" in Device Manager. - Both devices should also be working correctly in Game Controller If one or both of the HOTAS Warthog components are not enumerated correctly, or display a "!" in Device Manager, try connecting them to another USB port. That's a start. If that doesn't work your warthog may not have any firmware in it. There is a Bootloader method in the PDF attachment below that shows How to wake your HOTAS Warthog if it is no longer recognized on PC (i.e. in the event of firmware loss). Hope this helps! :D thr_eng_00140.pdf -
Public inquiry. What is your PC video card?
CubPilot replied to Chizh's topic in DCS World 1.x (read only)
Sapphire AMD R9 290X 4GB DDR5 + EK H2O block & Backplate -
Public inquiry. What is your PC video card?
CubPilot replied to Chizh's topic in DCS World 1.x (read only)
Sapphire AMD R9 290X, w/full water block. -
Public inquiry. What is your PC video card?
CubPilot replied to Chizh's topic in DCS World 1.x (read only)
AMD R9 290X 4GB DDR5 :pilotfly: -
Add TrackIR Center & Pause on 1 Joystick button
CubPilot replied to CubPilot's topic in PC Hardware and Related Software
That's great that you got it working as you wanted. As they say, Give a man a fish & you feed him for a day. Give a man a fish pole & some bait, you feed him for a lifetime! (well, something like that, or until the bait runs out :smilewink:). :pilotfly: -
Add TrackIR Center & Pause on 1 Joystick button
CubPilot replied to CubPilot's topic in PC Hardware and Related Software
I think it will work with the latest TIR software, but I haven't tested it yet. As to your wanting to use a modifier I think that post #45 & 46 gives you what is needed. To understand the AHK code here are some tips (I'm no expert either). Anything to the right of a ";" is not code and does nothing when the program is run, it is usually describing what the code does to the left of the ";" if the creator chose to do this. So, "1joy6" means, if you read the description, Windows controller #1, joy button #6. (you can discover button numbers using windows Controller Settings/Properties). There are 2 loops in the post #46 code. Loop #1 starts at the beginning of the code. Inside loop #1 is a second loop #2, beginning with the "IF" statement and ending with the first "return" statement. It will loop until the buttons described in the loop are pressed, etc as coded there. It then goes to the second "return" statement and loops back to the very first line in the code. Hope this is of some help. :pilotfly: -
Radio option controlled by joystick
CubPilot replied to alexej21's topic in PC Hardware and Related Software
An AutoHotKey script might do what you want. It is very light on computer resources, you won't know it's running. No TARGET software needed. I have my TrackIR Center & Pause mapped to the warthog joystick pinky lever, both items on the same button, using a short button press & long button press. Link. A few posts below this is one for assigning a VAC radio button mapped to an unused warthog throttle radio button position. It looks complicated, but that's because I wrote detailed instructions. You might look at it to get some ideas on how to do what you want to do. :pilotfly: -
PM sent! :pilotfly:
-
Hmmm hadn't thought about other aircraft and the TM Warthog, been using the A-10C for which the Warthog is plug & play in DCSW. The switch bindings in DCSW have a limitation when the LUA files are created. Let's consider the FLAP switch. It is a 3 position (ON-OFF-ON) switch . The actual switch makes contact (consider it as button pushes) in the up and down positions only. When a switch or button makes an electrical connection a unique value will be sent to the sim's software via LUA script. The problem is that no LUA script will be created when a connection is broken such as in the case of the Flap switch when put in the middle "OFF" position. So, one way to deal with this is by modifying the LUA script for the aircraft in question. What you do is to write a LUA statement that will send a value to the sim software when a connection is broken. I believe the LUA files you would alter would be in your Saved games folder inside your User Name folder for the particular aircraft you want to alter the LUA files for. Tigershark has some very good videos on how to do this, here http://forums.eagle.ru/showthread.php?t=65998. If you go to the last post in this thread and back a few there is a good example (post 285) that shows the current LUA code that deals with switches and buttons and how to alter it (I think the video was from the beta era of DCS A-10C & the LUA code looks different from how it is now). This is one way to do it without loading any profiles from another software. :pilotfly:
-
That's a pretty cool panel that you made there RogueSqdn. I can't do a full cockpit either, hence my strange mix of very non-lifelike switch panels and some concessions made to actual copies of the real thing (Fuel knobs). I do try to copy the general layout of the switch panels if I can. Glad the throttle kit is still working for you. I think it will outlast all of us. :smilewink: :pilotfly:
-
Good to see that you are still around! If you need any questions answered about the disable switch mounting I will be happy to elaborate. Cheers, :pilotfly:
-
New additions Well, it isn't a lot, but it is progress. I finally got around to doing something about my throttle placement. having it clamped to my keyboard tray sucked. So, pictured above is the slide out shelf idea that I came up with (I doubt I'm the only one who did something similar). The slides are heavy duty, 100 lb If I remember correctly, when clamped there is very little wobble. The only thing left to do is come up with a locking mechanism at the open position, using clamps at the moment. This is the side view and also shows the base for the Fuel Panel. Had room for it so just had to make it. This is not to actual scale, nor are the switches as on the real panels, I used mini switches. I left a small space between the Warthog throttle and the Fuel Panel so I can still use the Warthog cover I got from Deadman. Also the Fuel Panel base has been cut down in height after this picture was taken so its front edge matches the throttle base height. The beginnings of the Fuel Panel. The metal shafts of the Fuel Disable Push/Pull Switches can bee seen on the right side of the panel. The countersunk screws hold a small sub-panel for the Push/Pull Switches. The back side of the Fuel panel shows the Push/Pull Switches mounted on the sub-panel. They are positioned so that when the switch is pulled only the plastic knob is seen, the metal shaft isn't. Added the rest of the switches. Yes, these are SPDT ON/OFFswitches, but, they were ~$1 less for each switch as opposed to SPST ON/OFFswitches (Digikey). The right side of the Fuel panel base showing the RCVR Door lever. The black UHMW tape has been applied to the MDF and the back side of the gold color washer. It has adhesive on one side, the other side is very slick. This results in a very smooth movement of the lever. It is as smooth as using a ball bearing! The two silver screws are the lever stops. The lever is longer than it needs to be at this point. Throw the lever the opposite way and the microswitch is activated & the RCVR Door opens. A good view of the bolt, lever, flat washer, spring, cupped washer, and the nyloc nut (from right to left). What may look like threads between the washers is the spring, which is tightened so that the coils bind (touch each other), this adjusts the friction. I used the same method on my LDG lever. It is very smooth and yet stays put. This is the back of the Fuel Panel (top left, bottom right) showing how I attached the GP-Wiz40 USB card. The white spacers provide the needed room between the card and the aluminum bracket to prevent electrical shorts. The Fuel Panel base is back together, all wiring is done (w/a common GND for all switches). The DB15 cable is for the RCVR LT pot. It connects to my Leo Bodnar USB card on the main instrument panel that has spare axes available. The DB15 connector (upper right) is used for connecting switches from other switch panels (ELEC PWR panel). The other panel wiring wasn't done at this DB15 connector when this pic was taken. Here's the almost finished Fuel Panel after applying the switch markings (printed on glossy photo paper). This is topped with some plexiglass from Home Depot that has one "matte" side to it to reduce glare. I still need to paint the RCVR LT knob and the base. The knobs (except for the Fuel disable knobs) were purchased from Deadman, all top drawer stuff at reasonable prices!! I used the original knobs that came with the Push/Pull switches only because I was afraid that the knobs supplied by Deadman were a bit small diameter wise for the shafts/threads on these switches. I have a switch for the Line Check instead of a button. I don't think it is modeled in the sim and I plan on using the switch to turn ON/OFF joystick decreased sensitivity in LUA script for use when refueling. Figured that would be a good place for it. The other item I made is the ELEC PWR Panel. It's not even close to being the same size as the original. It is crunched up to fit the space where I wanted to put it on my main panel. Back side of ELEC PWR panel prior to wiring. ELEC PWR spacer attached to gray removeable "wing". The hole near the middle is for the wires, there is an angle secured at the right side of the hole on the back side to secure the wiring so it can't be pulled off the switch terminals (my cat would love to do that). Installing the switch plate and the last screw. The screws are coated black and are really used for drywall, but the course thread is ideal for MDF if you size the hole correctly to prevent the MDF from cracking. I added a DB15 connectors bracket to the back of the main instrument panel for the Fuel Panel RCVR LT pot and the ELEC PWR panel wiring. I have had the canopy switch done for quite some time. I also did the seat height switch. You might be wondering why the seat height switch, what good does that do? I find it useful if info on the HUD is "falling" off the HUD (at least in vertical directions), if it is I simply adjust my seat a bit. I'm using Helios this time to bind all my switches and the RCVR LT pot to DCSW. Getting tired doing switches in the LUA files (& I don't know how to do pots in LUA). We will see how Helios gets along with new versions of DCSW in the future. That's about it at the moment! :pilotfly:
-
Oh my God! One of my suggestions may have actually worked! :v: Or was it the flash that did it. No matter, glad to hear that your USB controllers are now behaving with DCS. :D :pilotfly:
-
The USB ID's are an operating system function as far as I know. So if you use this program USBDeview: you will be able to see that info and more for any USB device that is connected to, or has been connected to your computer. Sometimes cleaning out old USB ID's will fix a problem with a USB device that used to work but now does not work properly. I guess I need to rephrase my suggestion made in my previous post. I would try deleting any USB controller ID's that are having the problems as stated in the first post using USBDeview. When that USB controller is plugged in again it will create a new ID and it may fix the problem. :pilotfly:
-
I think the USB cards need to have a unique ID, which is probably the case if they worked with the Steam version of DCS World. You might try deleting any old USB ID's relating to DCS and try plugging in your USB boards again which will recreate the ID's. USBDeview: USBDeview is a small utility that lists all USB devices that currently connected to your computer, as well as all USB devices that you previously used. For each USB device, extended information is displayed: Device name/description, device type, serial number (for mass storage devices), the date/time that device was added, VendorID, ProductID, and more... USBDeview also allows you to uninstall USB devices that you previously used, disconnect USB devices that are currently connected to your computer, as well as to disable and enable USB devices. You can also use USBDeview on a remote computer, as long as you login to that computer with admin user. :pilotfly:
-
I put my TIR Pause & Center on my joystick pinky lever which I personally find the best place for it. Short press of the pinky lever Centers & long press Pauses TIR. I also use key assignments that most likely will never be used by DCS or other sims. It could be modified for any warthog button. http://forums.eagle.ru/showthread.php?t=87543 -Cheers :pilotfly:
-
Yes, that happens. There is an option that you can check in the UI screen, it might be under the Misc. Tab that says something like Sync switches on startup or something of that nature. Check mark that item. So, start the Sim, PAUSE it, manually sync your physical switches to the position the virtual switches are at, then un-pause and if the LUA is modified correctly (if needed) your switches should stay in sync during the time you spend in the sim. The need to sync some switches at startup is the price we pay to have physical switches. :pilotfly: