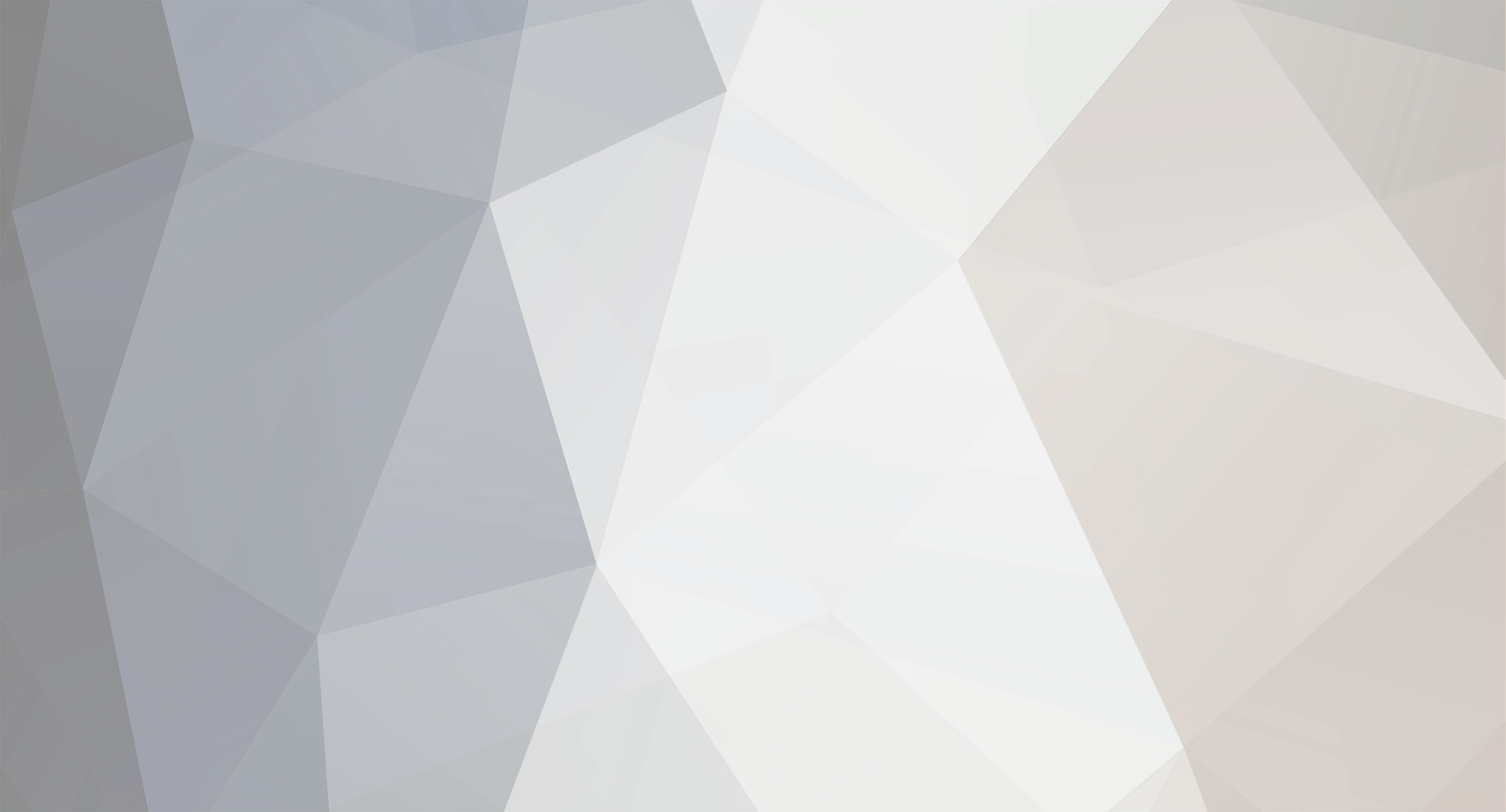
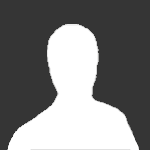
roadrabbit
Members-
Posts
127 -
Joined
-
Last visited
Content Type
Profiles
Forums
Events
Everything posted by roadrabbit
-
About those wingtip vortices & engine smoke ...
roadrabbit replied to Echo38's topic in DCS World 1.x (read only)
;) Well. I have now! The question still arises - how did the designers find a way round the blade interference problem? I see from my latest reading that by bending the blade into a 'scimitar' shape it delays the onset of the transonic airflow over the blade tips - perhaps it was this transonic flow that was causing blade interference? -
About those wingtip vortices & engine smoke ...
roadrabbit replied to Echo38's topic in DCS World 1.x (read only)
Correct - I am amazed. For those who want to know more than they need ;) I recommend the Wikipedia entry Propeller (Aircraft) which has a great description (plus formulae!) of most of what has been discussed in this thread. It also has some great photos. :smartass: -
Set up a practice convoy in a narrow valley. Came in low following the valley road and gave the convoy a blast from the GAU. Forgot I'd set up the convoy as 'insurgents': why doesn't the plane repond? Why can't I fly this thing? Why have all switches stopped working? Oh, oh ....... I'm dead, that's why! The rotten s...s fired back!
-
About those wingtip vortices & engine smoke ...
roadrabbit replied to Echo38's topic in DCS World 1.x (read only)
A book I was reading a while ago stated that the number of blades on a propeller was 'limited' to 5 by propeller interference. I have just seen another photo of the Alenia C27-J (thanks to Python for alerting me) which has 6 bladed propellers. Anyone know how the 'limit' was able to be broken? -
About those wingtip vortices & engine smoke ...
roadrabbit replied to Echo38's topic in DCS World 1.x (read only)
Another element in the equation is altitude. Jet engines are most efficient at higher altitudes with reference to specific fuel burn per distance travelled. Therefore the inlet guide vanes ae designed to be most efficient at these higher altitudes. With fixed IGV's they are not as efficient at lower altitudes and one result is less efficient fuel-burn leading to visible black smoke in the exhaust. Many military (and civil) jet engines of the past had fixed IGV's and so produced black smoky exhausts when at high power and lower altitudes. A comparison is an off-tune diesel engine in a car - if you floor the accelerator you get clouds of black exhaust smoke. -
About those wingtip vortices & engine smoke ...
roadrabbit replied to Echo38's topic in DCS World 1.x (read only)
Precisely! :D -
About those wingtip vortices & engine smoke ...
roadrabbit replied to Echo38's topic in DCS World 1.x (read only)
:) Hi Flagrum - I have just shortened your quoted reply in order to answer a specific problem. What you have tried to do is resolve the propeller motion of an aircraft in flight into two seperate motions. This can be instructive on occasion, but could be confusing the issue here. Notice I have not even introduced supersonics here! As a propeller rotates it meets the air. With an aeroplane stationary on the ground the relative speed of the air to each propeller blade increases with distance from the centre of rotation. This means that with a constant section airfoil (one with no twist in it) the angle of attack of each blade increases towards the tip. If the physical blade angle is more than a small amount, at some point along the blade's length towards the tip the blade will stall at normal rotation speed. To prevent this a propeller blade is twisted and has "wash-out" from the spinner to the tip. Thus at a typical rotational speed of 2,000 +/- rpm the blade will produce thrust (the 'lift' force spoken of previously) evenly along its length. Now the tricky bit :D. As an aircraft gathers speed the forward motion of the plane comes into the picture. There is, as you say, now a longitudinal component to the airflow meeting the blade which is along the propeller's axis to the free airflow. (Try though here to picture the 'total' airflow meeting the blade - the propeller cuts a helical path through the air like a screw going into wood) This has the effect of decreasing the thrust of the propeller if at constant rpm. At some point in the aircraft's acceleration the thrust will reduce until it equals the total drag of the aircraft - this will be the maximum speed of the aircraft at that propeller rpm. Increasing power can increase rpm and thus speed, but eventually the propeller drag will equal the engine power - the aircraft speed reached will then be the maximum in level flight. There is much more theory and explanation about variable pitch and 'constant speed' propellers, but it would be better for anyone interested to consult one of the many textbooks available. In the UK I started off with "Flight Briefing for Pilots" written by Birch and Bramson. I am not sure if it still in print, but I am sure there have been replacements! :book: -
About those wingtip vortices & engine smoke ...
roadrabbit replied to Echo38's topic in DCS World 1.x (read only)
This does not accord with what I was taught. First off - a totally flat blade does have a profile i.e. totally flat. It will produce local lift forces if presented at an angle of attack to local airflow, as with a propeller. Secondly, airflow is relative. This means that any aerofoil moving (relatively) through a mass of air will have all the aerodynamic forces such as lift and drag present. The thrust produced is equivalent to lift on a wing section. Thus the actual thrust is proportional to the square of the local propeller section and only directly to the section of the aerofoil section (shape). Taking the case of a propeller tip rotating so fast that the local airflow is moving supersonically in relation to the tip, then you will get shock waves being produced. These may have visual product through condensation, with visible vapour being produced, and which usually converts back to invisible water vapour almost immediately as it exits the shock zone. These shock waves interfere with the airflow in the immediate vicinity and cause localized loss of "lift", which, in the case of a propeller, is thrust. Vibration is caused by the effect of the shock waves produced giving continually variable local "lift" as the air meets the tips at slightly varying angles. Thus you can see that at the propeller tip the air is moving supersonically, but in relation to the tip itself. Think of an aircraft going supersonic: the air is not moving over the ground at supersonic speed, but the aircraft is moving through the air at supersonic speed. It is the relative speed between the air and the aerofoil which produces the supersonic effects. :thumbup: -
Two different headings to the runway?
roadrabbit replied to Dudester22's topic in DCS: A-10C Warthog
This is a thread which seems to come up with great regularity.:doh: Could someone create a 'sticky' with the information laid out simply and succinctly (it's Sunday night and I'm showing off :music_whistling:)? The charts can be found in your folder ....... Eagle Dynamics/DCS World/Doc/Charts and use the charts labelled "DCS_VAD_Charts_A10C" All the previous information is correct, the big point being that there can be three heading references: 1. grid north 2. true north 3. magnetic north Just remember that the A-10C uses magnetic north, and make sure the charts you use have the same heading reference. :D -
I do like the way you guys are thinking about the order of the checks and thighs and things, and thighs ........ :music_whistling: In a previous a/c we did the checks pretty much the route you have been following above. The route given in the A-10C checklist seems a little odd, even if taken from the RW. In modern a/c the preflight cockpit check is basically a quick scan across the panels to make sure anything that will kill you or damage the a/c is set to off. The next thing is to enable basic electrical power so that computers can be switched on, and, most importantly, gyro platforms can spin up and the alignment process can begin. This can take up to 15 minutes (yes, I know the A-10C is quicker!), so leaving the CDU until just before engine start is the item that seems the oddest in the A-10C checklist provided. Once the alignment process has begun, then you can do the detailed cockpit checks. This way, by the time you complete them, the alignment process should be just about complete and you are ready to go, with no time wasted. Otherwise you have to sit on your hands and wait ........... and wait ........ and wait ........
-
I am very happy now with my triple displays working from an nVidia GTX 590 graphics card - but I would like more! Specifically I am wondering is it possible to incorporate two Cougar MFD's with 2 7 inch TFT displays to actively model the two MFCDs of the A-10C Warthog? If so, can someone explain how to go about it? I use a Track iR 5 at present, but would like to model the MFCDs in the same way that the Thrustmaster HOTAS models the thrust lever panel. I have several virtual beers on offer to share with the best reply! :drink:
-
And it is much appreciated! :D Your statement above says it all - some just don't get the difference between a "full blown simulation" and those other games out there. Yes - you could reduce the FPS loss caused by rendering of explosions and smoke etc, but then you would get complaints that it looked less than realistic. Didn't someone once say: "You can please some of the people all of the time .... "? "But apart from that, Mrs Lincoln, what did you think of the play?" :music_whistling:
-
The fullest discussion is in thread "WTH Happened to the Load Times", see page 10 and following. It certainly may NOT be the answer as there are so many other possible causes, eg a weaker GPU. However, many responses come from folk with RAM of 4 GB and 8 GB, and some of the more knowledgeable replies talk of the large(er) amount needed by the latest versions of DCS World. One thing that some may not be aware of is th limit on usable RAM caused by the operating system - and this is what the referenced thread above addresses. I am always surprised at how many do NOT put their rig specs down as a signature, and how even fewer say what their operating system is - it would help all those who would like to help. :)
-
;) Looking at your rig, may I suggest the answer could be just a lack of RAM? This has been discussed in depth elsewhere on the forum, but anything less than 16 GB of RAM causes problems with various parts of DCS World in the latest releases. You only have 8 GB RAM which others have suggest is just not enough. With an Intel i-7 chip and an SSD drive it is only your RAM which gives cause for concern. It costs, yes, but with my rig I have Windows 7 Professional and 24 GB usable RAM (yes - it is a little over the top :D) but I get 80 fps all the time running with three monitors and Track IR5. I also have the nVidia GTX 590 which runs the three monitors as a single screen. Note that to increase usable RAM above 16 GB you will need Windows 7 Professional or above.
-
Why not follow the recommended landing technique? :D 40% speedbrakes on approach with 30 degs flap and the landing gear down. Fly the 'donut' accurately. You will have power on to counter the drag from all three items: speedbrakes, flaps and wheels.. At the flare point, as Bill says, walk the TVV further down the runway by slightly raising the nose. Close the thrust levers and hold the attitude - wait for the touch-down. Do NOT 'feel' for the runway! On touch-down raise the speedbrakes to full, gently lower the nosewheel onto the runway. Then apply wheel-brakes. Keep straight with rudder and don't select nose-wheel steering until below 50 kts and with the rudders at neutral (or you will shoot to one side of the runway or the other!). Believe me - it works, and works well :thumbup:
-
:( Yeah, yeah, yeah! Too slow - was always my problem. All good initially, but then a drift off left with nothing to steer with. More practice required, obviously. Think I'll become immortal until I work out a fix - fed up with thinking of new names :D
-
Thanks for that, Noodle. Now I just have to get that Control Stick lever to work the Emergency Brakes - I've just tried it assigned, and I've just died (again!) by hitting a radar truck off the side of the runway after a catastrophic left engine failure at 100 kts.
-
:thumbup: Yes, I am agreeing with you - what I meant by primary effects was the assymetric power causing a swing, and the need to brake during an RTO, i.e. before take-off. The primary controls are there to be used to counter the swing, but with a left engine failure you would have only right rudder powered (are they connected - both work in ED with zero left hyd pressure?) and no nosewheel steering. Avoiding going off the side of the runway would be your primary object, with going off the end of the runway being secondary (at first!). I now think that setting the lever switch on the control stick to Emergency Brakes (on the Thrustmaster HOTAS control stick) will be a good idea - as I've said elsewhere, using the keyboard as set requires two hands and 'looking in'! Question: with a left engine failure will speedbrakes still be available? The manual suggests not, which seems at odds with how the systems are set. Secondary question: If they do work with a left engine fail, is the RW RTO drill to try and extend them anyway?
-
I have just done some more checks of hydraulic action after shutting down the left engine. On the DCS A-10C the pressure remains at 3,400 psi provided you don't touch anything (I was stationary on a runway!). Exercising the flight controls didn't have any effect on hyd pressure and nor did moving the nosewheel. After more than 60 secs after shutdown (no hyd pressure reduction), cycling the wheelbrakes did have an effect and I was able to reduce the hyd pressure to an effective zero with about 10 cycles. Prior to this I did have effective nosewheel steering. Afterwards I had lost both wheelbrakes and nosewheel steering. I had probably lost hyd flap operation as well but the 'other' pilot :huh: forgot to check! It may all seem a bit pedantic, but I feel I am really getting to know how this DCS ship operates. One thing occurs to me: if you lost the left engine and rejected the take-off, it would be nice to know that a little (accumulator) hyd pressure was left to steer and brake the aircraft. Dealing with the primary effects of engine loss wouldn't leave much headspace to deal with alternate brakes and reduced steering capability. Just a thought :D
-
:music_whistling: Fancy me forgetting that the gas is in a bladder!
-
Very useful and informative thread. Re the above: actually a hydaulic reservoir doesn't just contain hydraulic fluid - it also contains gas (air?) which is compressible. Other aircraft have reservoirs at e.g. 3,000 psi, which is often enough stored pressure to operate emergency brakes following an RTO. The trick is NOT to pump the brakes as you will, as described previously, use up all the stored pressure. :smartass:
-
Well, ...... not quite that far! I do have 'Birds' set about 1/3 of total. I shall reduce it and see if it makes a difference. What is 1000% anyway - 10 x the maximum? Reminds me of Bob Newhart's story of Sir Walter Raleigh's discovery of tobacco: "You know, Walt, back here in England, come fall, we're up to our ears in leaves"! :smilewink:
-
Exploring the hydraulics systems on the DCS A-10C I shut down the left engine. I expected to lose the use of the flaps, nosewheel steering, wheel brakes, anti-skid and the hydraulic control of the left elevator and rudder actuators (along with loss of dual channel pitch and yaw SAS). But no - I still had nosewheel steering and wheel brakes.The SAS warnings DID come up on the warning panel. So what is going on? This all came about because I wanted to assign a "usable" keyboard stroke to activate the Emergency Brake - using HOTAS have you tried to operate the combination of 'W RWin'? Or maybe you have no trouble with mouse operation of the Emergency Brakes lever in the virtual cockpit :lol: Look out grass - here we come!
-
You didn't see my plane after my last mission, did you? :music_whistling:
-
Quite right! I shall show my age now :D, but way back when we had to navigate before INS or GPS were around, we used TAS with forecast winds to provide a provisional course to steer (heading) to maintain a desired direction (which we in the UK called 'track'). This calculation also gave us ground speed, so we could estimate our ETA at the next navigation point. When we got our next fix (no, Brian, not that kind!) we then found out how good or bad the forecast had been, and adjusted our next heading to steer.