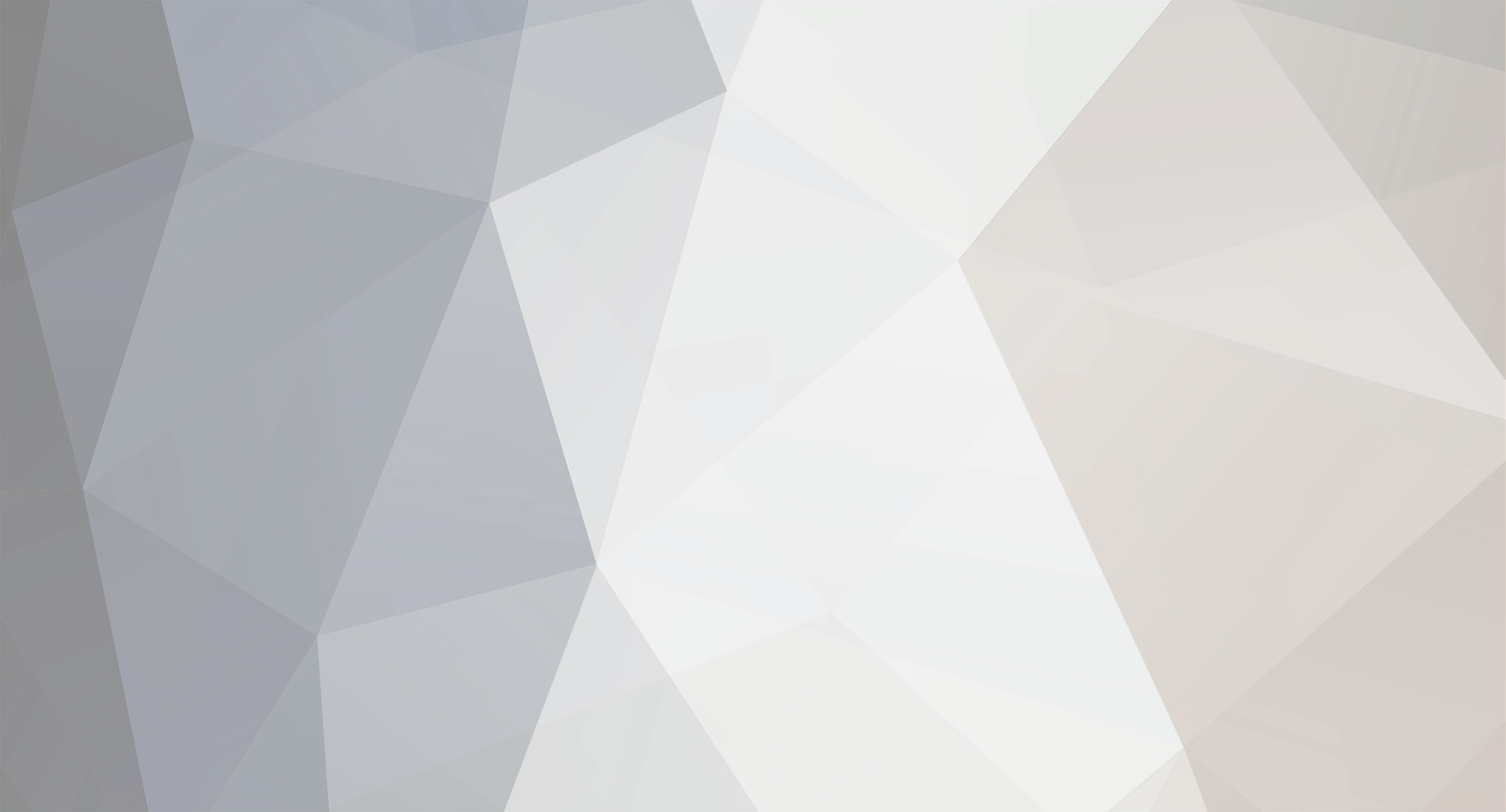
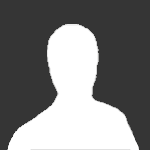
Boltz
Members-
Posts
476 -
Joined
-
Last visited
-
Days Won
1
Content Type
Profiles
Forums
Events
Everything posted by Boltz
-
SAS panel mag switches connected to the RS485 bus and working
-
Got it working. Removed the orange seal, changed contacts and then put the seal back. I thought they should be able to be changed in place but possibly not or I had the wrong tool. It's good enough for the pit
-
Hey Deadman! Hope you are well. I've got a lot to catch up on with building. I have a question, do you know what tool is needed to insert/extract the contacts from Honeywell IWTS switches? I tried the M81969/14-10 and -11 tools with no success
-
Wired up a few panels recently and tested them with DCS. I need to download the latest version and reinstall at some point but DCS-BIOS works perfectly with what I have. First up is the Antenna Select Panel and Electrical Power Following Hans work, I also got the magnetic switches working nicely. Need to order more Ethernet cables for the RS485 bus then can keep the panels connected up.
-
Wow Hempstead, excellent quality casting you have done there! Very impressive work
-
Not yet Nikolas. I think it should be possible to machine a small cylindrical pin slot mechanism and add a compression spring. I also looked at Henkie's excellent work http://www.pdp-11.nl/viperpit/ky58/ky58-panel.html The CMSP doesn't have a lot of space around the rotary switch so I'm not sure which I will go with.
-
Looking great John, incredible how much you have completed. I have another design for the RWR using a 4" LCD which ends up just larger than the original. It needs some dimensions changed IIRC but I will find the design tonight. Thanks for the links to sketches, can't wait to get things connected up. Then I have to update DCS
-
Thanks guys. Hope you are both keeping well
-
Update 14/07/2019 I've had very little time to work on much pit related work this year. I started a degree in Mechanical Engineering last year and moved into a new flat. Changed jobs along the way and currently in Austria for the summer. At least I have some time in the evenings now to start on the pit again. I've been working through my notebook, building some designs in CAD. 3 weeks ago I managed to sit down and work on the caution panel. This is a real panel that I have got working. It has the flashing and master caution reset logic built in which took some time to reverse engineer. No video for now but I've got the PCB designed to control the panel by Arduino. I will make a video when I'm back and have it running again. Apologies for the panel being upside down and notice the cheap pushbutton sitting on top acting as my master caution for the time being. Filled the NMSP with the illuminated push buttons. I've cut most of the parts needed to convert the lenses for the A-10. Still working on the process to have the text white and triangle masked but still having them backlightable. Got a couple small panels engraved More switches acquired Wired post lights for engine instruments to a connector. Tested them on an off the shelf dimming circuit but they need to be changed to a custom high-side circuit instead. This was a small side project I tried. Both images are the same size but using a fresnel lens to magnify the RWR. This isn't going to work due to the users viewpoint not being perfectly perpendicular to the lens. I might have found a suitable screen though. When I have time I'm trying to work on some PCB designs. Hopefully I will be able to put in my order at the start of Autumn and finally get some parts properly wired up and working in a more final location. Boltz
-
Many thanks WhoMadeWho and congrats on all your work! I really like the look of your RWR. The engraved green over the screen completes it.
-
Looks excellent WhoMadeWho! Love all the gauges but what screen did you use for the RWR? I've been struggling to find something good for it.
-
Finally removed the masks around the digits on the 186 panel to see the lighting. The edges of the cutouts still need to be cleaned up but the lighting looks good. There's also another LED to go in the top right corner but not sure if it will be needed. There was no way for the PCB to reach the corner so I bought a 3mm LED of the same wavelength and made a cutout in the front plate so it can be pushed in
-
I haven't put a whole lot of thought into the HSI yet and my knowledge isn't very good regarding how it should work with DCS. The Course knob is mechanically connected to both the course readout and the marker on the compass rose. I'm not sure if it also is connected to a synchro, I really need a lesson in DCS navigation to know what to expect. The heading knob is mechanically connected to the so called "captain's bars" on the HSI and also the shaft of a synchro. A friend told me that this synchro's stator is wired to the same pins as those used to set the magnetic heading which allows the "captain's bars" to follow the magnetic heading. And the rotor connections are available on other pins. The system seems a bit vague to me and I really want to get the HSI powered up on the bench and hooked up to a test setup. I still haven't totally decided on whether I will use synchro transmitters or generate the synchro stator signals from digital electronics. I'm about to get a few test PCBs that should do this. My ADI actually has a some damage inside as well so I'll be having to convert it mechanically unless I can find a replacement in working order Painted the throttle left grip today to match the right. It will need sanded down and at least another coat first Also cut the plates needed for the front of the 164 and engraved the metal display bezel and A32 plate
-
Thanks Hans. The 20 position switch cost 70USD, so I'm waiting a bit before buying the second one. More than I'd like to spend on it but finished the panel nicely. The flip cover on the radio was printed by shapeways. Came out well but took some time cleaning up the surface. I've got fingers crossed that everything works as expected. Can't wait to get the engraving done and backlighting on. I'm still touching up paint at the moment on front plates then I'll leave them a full week for all the paint to harden, there's 10 layers there. Cheers Calum
-
Thanks guys. GSS Rain your videos have been a huge inspiration for me! I've started following along with your ADI and HSI. Just looking for a few suitable synchro transmitters. I've got the parts to build a 115V 400Hz power supply just not got round to it. I can't stand that 400Hz sound so opted to build much lower rated supplies. It's really been off and on with working on things for me but I've kept on designing and learning some new software packages. I finished putting together the fuel receiver lever and emergency brake housing. Took time to fill and sand that one but it's together. Just need to paint the actual handle so I'm currently looking at the best way to paint the letters and stripes. Any tips would be most welcome. Altimeter is still in pieces. The one I have has such a gear ratio such that I need a very fast spinning motor to turn the shaft even slowly. That led to some alignment problems and vibration because of the speed so I'm more or less back to the drawing board on getting it working. I've figured a mini lathe would make it easier so that maybe an excuse for a purchase sooner rather than later :music_whistling: I've tapped all the knobs I need for the left console. I purchased them from DM's Shapeways store and I have to say they are brilliant. Fit all the panels perfectly. I just drill the set screw holes to 2.5mm and then tap for M3 and the set screws hold fine. No stripping of threads and they have a good hold on the shafts, even the tough Grayhill switches. I managed to completely assemble the first VHF radio head, and it all works! From a long time ago I wanted mechanical radios instead of digital displays and finally realized that plan. Pics don't give the best views but it's all I have since it's now apart to paint the last parts. I'm going to add an extra plate to support the extended shaft of the large rotary switch. All the digits will be illuminated through the frontplate, at least that's the plan. If it doesn't work I can go back to backlighting them. The 164 UHF panel is also nearly completed. The small plates on the lightplate need cut and a filter over the displays. The lightplate is nearly 16mm thick, since I thought this would be a great idea. It does look good not being in layers but I think it cost me far more to produce than splitting it. I also got back out to the garage where the pit structure is and modified the left console to fit the throttle and then the left side to fit the console in. Need to test the slew control of the throttle. There's not space to keep the PCB in the grip so I'll have to relocate it under the throttle or build a new amplifier circuit which is probably simpler and easier to interface. Ground Safety panel and utility light are nearly finished. Just need wired up. No backlighting here and just 28VDC for the light. Tested working on 24V which is already in the pit so that'll work fine. Annunciator lenses are all engraved. I'm playing with resistors at the moment to find good "bright" and "dim" values so that the signal lights switch works. Built the indexers and MIP annunciators. For bending the metal I only have a set of brake jaws in a 4" vice so even some of these parts were beyond their capability and I had to improvise. A larger folder is definitely on the never ending list of tools to purchase. And finally I picked up a suitable HSI for the pit I'm really going to try and post more regularly now that I've got imgur on my phone it's much simpler to upload pictures. Currently waiting for paint to dry and then should get into engraving lightplates next week. Cheers, Calum
-
Started the altimeter project a while ago but last night I designed the parts to get it working and ordered the off the shelf components. Today decided to get on and convert the front end of the instrument. It started life in a tornado and looked much the same as this one I took it apart about 6 months ago but never really got anywhere with conversion. Today I finally realized the part of a dream by converting the front of the instrument. I changed the flag from STBY to PNEU, changed the faceplate and painted the bezel. Finally I changed the drum from the millibars reading in inches of mercury. Took some time to figure out where the stops were and how to get past them but I managed to wind it all the way up to the correct part of the scale after disconnecting the mechanism that adjusts the main scale. I still need to file a profile into the stop piece to increase the travel but that shouldn't be too difficult. I'm going to attempt to 3D print the pointer through shapeways. It should come out nicely. And then I need to make the parts for the backside to make it work again.
-
Hi Hans, Alburg is correct. I just went with cheap rivnuts instead of floating nuts couldn’t afford to spend that much on them. They’ve worked perfectly. Alburg it’s a great way to construct them. Just took me some time to acquire all the tools and ability to actually produce them consistently. I’m leaving light plates till the end in case anything changes since they cover a lot of the workings from the front
-
Awesome work Hans! Very jealous of that KY-58 and I see it has the NVG backlighting and good condition. Nice find. Cheers
-
Thanks marques. I was able to reassemble a lot of parts after painting. Everything is looking sweet now. First the new throttle grip. The speedbrake and china hat are original switches, hat switches are Mil Spec Otto. Ordered a proper boat switch as the cheap one I tried first broke it was just that, cheap and nasty. You can see the missing spacer part in the second picture. It's on the way then everything can be fitted correctly. Annunciators for the right console are started. Still need to assemble the actual fronts with text. They are in the "to-do" box. Emergency brake housing and mechanism are fitted for a dry assembly before breaking out rivets and epoxy. Paint on the handle needs cleaned off and redone. Finally a load of panels are back together painted and with the switches installed. The red Honeywell switches are beautiful and the feeling on some of the real locking ones are so good. Definitely been worth all the time and money hunting them all down. Most of these panels need lightplates, backlighting PCBs and wiring then they will be finished (probably years of work:music_whistling:). Well that's all for now. Long overdue on the pictures. Displays for the UHF radio finally arrived a couple days ago, just in time for the snow here. Just waiting on Max7219 chips to test them out Huge thanks to both Deadman and Hans for all the help you guys have given me. Wouldn't have got this far if it weren't for your help and inspiration Cheers
-
Thanks guys. I got the new throttle end but still needing another spacer part for it since I had to file more of the original grip. Means that it won't follow the original curves perfectly but should still look good. Also managed to paint the backplates for most of the left console and install the switches. Switch collection is nearly done just needing the SAS panel monitor switch, 1 more pot and the rotaries for the 186 panel. Using Honeywell 53C110K pots which have a real nice feel. I bought one of the 53C1SW10K for the fuel receiver light control which says "It is available in a special construction that accepts a rotary switch (purchased separately)." However I cannot find any more information on the rotary switch unit anywhere and the construction appears identical to the regular 53C1 pots. Anyone have any idea how it's meant to work? I'll take some photos tomorrow when back at home. For now though I finished work on the radios, all ready to go with them, just saving up the money now to buy the rest of the parts. The AN/ARC-186 VHF panels have the mechanical displays instead of 7 segment displays. This is something I've wanted to do for a very long time. Fitting in backlighting for the panel text, digits and thumbwheel display required a lot of work but it's all drawn up now. Over the past few months I've been purchasing several of Deadman's knobs from Shapeways and the quality is outstanding! Highly recommend them to everyone. Just need to get my painting up to scratch first before touching them. Cheers
-
Should have all the parts for fuel panel, emergency brake handle, annunciators and connector plates for all of the left console next week. Got to place an order on Shapeways next for some more parts. Finished up on designing the AN/ARC-164 panel. Biggest hurdle on that next is working out how to mill the lightplate. It's quite thick at nearly 16mm! I wanted to test the circuit boards though so got on and ordered them. One holds all 8 displays, a second contains a MAX7219. So all the 7 segment display neatly transform to 5 wires. Forgot to add decoupling caps to that one so I'll either have a new one made or just make do with some hacking. The third is simply a shield for an Arduino Mega, allowing all the switches and displays to be connected. The boards arrived today with minimum order of 10 each so theres a few spare :music_whistling: Started design of the 186 radios with mechanical displays. Really tight to get everything to fit but I'm working on getting everything positioned correct then can add support parts in the remaining space. This panel still has a long way to go but I've ordered some of the hardware such as gears and couplings from China so they should be here sometime in the next month Also a pic of some of the parts I've managed to acquire. There's a g-meter and standby compass as well as a prototype 3D printed Grimes light alongside a real on the right. Everything confirmed correct on it so good to go and have the rest printed. Also the hat switch for emergency flight panel, seat adjust switch and fire extinguish on the glareshield. Also, managed to get my hands on the 4 elusive 3-position locking toggle switches for the AHCP. And a really nice Grimes utility light Also started collecting some of the electronics I need to get things wired up. Started out with the power supplies with two 5V/10A supplies and a 24V/5A in a 19" subrack. Still to work out what other voltages will be required then I can make the fuse and diagnostic panels and wire all up to 230V. Then I'll have some solid high current supplies to have things working. That's everything I'm up to at the moment
-
Some information on the stepper motor test setup: At the moment I'm playing around with the firmware to get good performance out of the motors. It's not for testing all stepper motors, but just the 2 most common ones I'm playing with now. Cutting a bunch of metal connector plates for the left console as well as parts for air refuel lever and emergency brake handle. I'll have something to show soon on those. I've been away from the pit a lot recently but had time to draw up a lot in CAD. Also put together all the 2D and 3D drawings to make each of the individual parts as well as parts list for each. Just got to save up some money first then can get to ordering more parts :thumbup: Cheers, Boltz
-
Ganeshka, I can’t provide dimensions of each part because I’m not taking it all apart. IMO would cost far more to reproduce one than to buy a real throttle. The TM version is a good version. Mr Burns the real throttle has a friction control it’s just in a different place. It is the grey slider on the right hand side. It’s an axis on the TM version but a mechanical linkage on the real throttle. I hear ya on trying to get some of the real parts. Some are pretty difficult to get
-
Bought a new toy recently. Cost quite a bit to get to the UK but totally worth it. Made a stand for it since it doesn’t fit in my current console setup. Needs converting to Charlie model, fuel flow switch guard, hall sensors for position and required to cheaper connectors. At the moment enjoying sitting it on the desk. Coolest desktop throttle :thumbup:
-
Thank you very much guys! Got plenty more happening at the moment. Warhog, I haven’t totally decided on controllers but looking at using a 40MHz PIC (can’t remember part no at the moment per 4 instruments based on some other designs. It’s a bit vague at the moment. I will get some pictures up of the test rig. It’s built around an Arduino Uno and can run both unipolar and small bipolar motors like the x27. Your move sounds sweet hope you enjoy Nova Scotia!