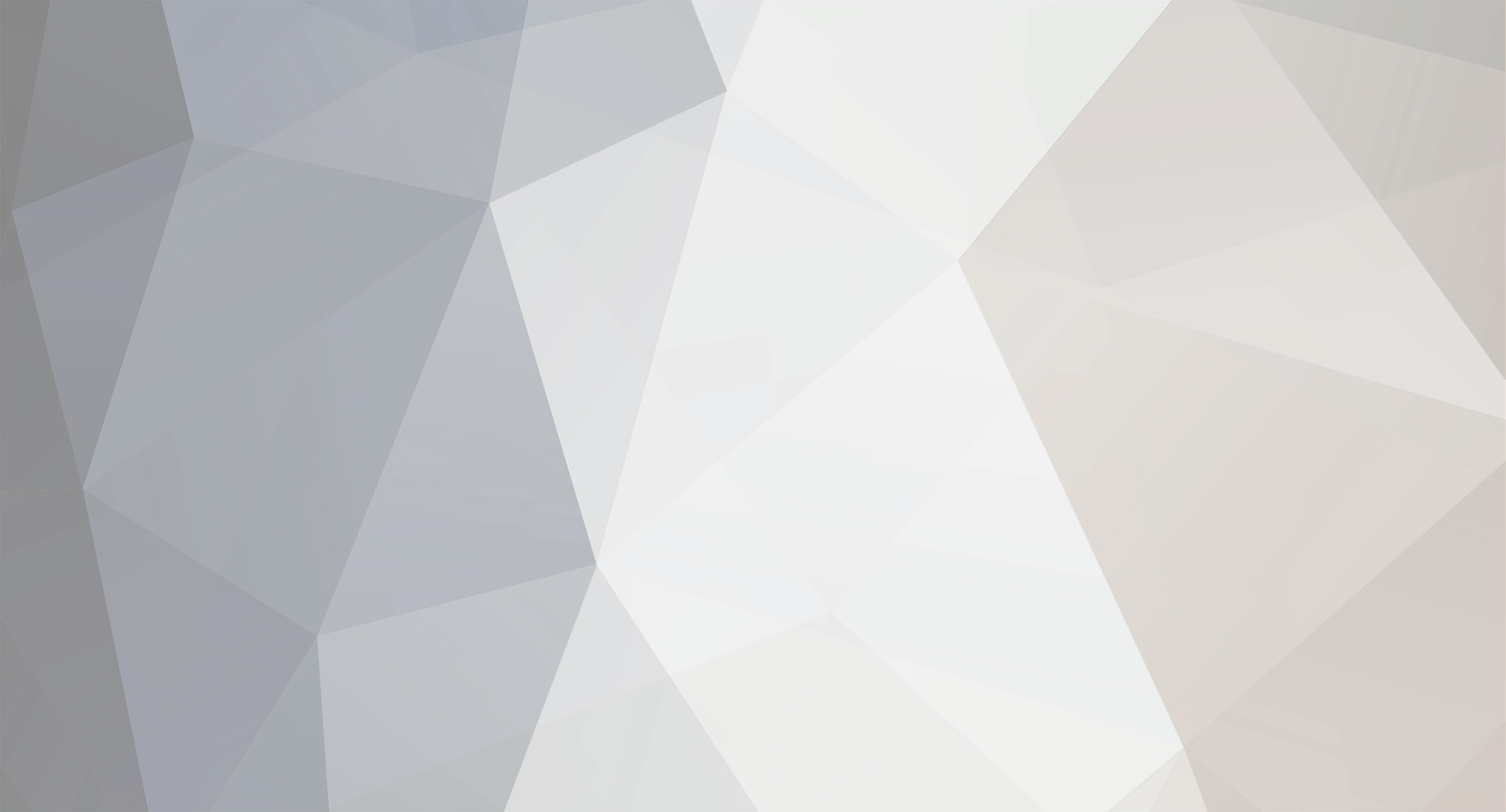
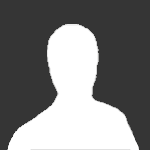
Mike Powell
Members-
Posts
164 -
Joined
-
Last visited
-
Days Won
1
Content Type
Profiles
Forums
Events
Everything posted by Mike Powell
-
well done. good example of a useful concept.
-
Very nice!
-
What technology/tools to use for building cockpit?
Mike Powell replied to Fabou78's topic in Home Cockpits
Home cockpits tend to be long projects, and as you've already noticed, interfacing hardware tends to have a short "product life span". Over the years I've watched many people struggle with items that are no longer supported and/or no longer produced. With that in mind, Arduino has substantial appeal. It is such a versatile and successful module that it has a massive user base and is very likely to be around for a long time. It has the additional advantages of many, free online tutorials, low cost clones, multiple suppliers, and the existence of a flight sim specific code base in the form of DCS-BIOS. -
People build panels in as many different ways as there are people. I've seen them made from cardboard, Masonite, wood, plastic, and metal. It's up to you, your skill level, and what degree of fidelity you're looking for. Same thing's true for the interfacing boards, though there is a lot of interest in using Arduinos. Software depends on the simulator software being used. Here, in DCS land, you have the great advantage of having DCS-BIOS which will do most of your interfacing software for you, but not all, you still have to set it up for your particular cockpit implementation. There's probably no way to avoid learning some programming. This is a very involved hobby. You learn new stuff daily. Or maybe a better arrangement of those words is: You must learn new stuff daily if you're going to be involved in this hobby.
-
Wow. I don't know if I'm more envious of the pedals, or of the fact that you have a shop which is provisioned with enough high quality "scrap" to build them. Well done, sir!
-
Where do you guys get your information from?
Mike Powell replied to .30-06 Springfield's topic in Home Cockpits
Information is where you find it. There's rarely a good single source. Generally I've had to assemble bits and pieces from multiple sources. For the B-8 flight grip (also called an MC-2) check manufacturer sites: Guardian Electric, Otto Engineering, Mason (part of Esterline). They've all made it at one time or other. I've seen catalogs with dimensional drawings (though I can't find them now). Infinity Aerospace makes a slightly smaller version for the sport aviation market. You can buy a new B-8 grip through Aircraft Spruce. Search through pictures on forums. People post pictures, sometimes with a ruler in the pic. Ebay can be a source of info as sellers generally post pictures. Visiting an aircraft museum is not a bad idea. Many have volunteers helping who can be sympathetic to polite requests for help. -
Solderless PCB mounting for pushbuttons, on-off switches etc
Mike Powell replied to pappavis's topic in Home Cockpits
Just in case no one's mentioned this yet (cough, cough) Learn to solder! Even milspec metal-on-metal connectors have problems. Simple wire ends stuck together will cause no end of grief. The problems won't be something as simple as a disconnected circuit, though you'll see those too. You'll experience a variety of intermittent problems. If you have enough non-soldered connections, you'll eventually see non-ohmic connections form when (usually invisible) corrosion at the connection point turns the connection into a diode like structure. Circuit malfunctions will be so weird as to define description. Frustration will set in. You'll begin to drink heavily and pull your hair out. Your sleep will be affected. Eventually you'll give up on sim building and take up Karaoke. It will be terrible, so just learn to solder. -
One of the desired effects of the military G-seats is to shift the pilot's viewpoint. If you're smashed down into the seat your perspective of the MIP, HUD, etc. changes, and this happens exactly when it's most important to get things right. This is one of the reasons that bladder types G-seats were developed. (Not to say there aren't other approaches.) So, if you're looking for super realism in addition to better immersion, shifting the viewpoint is something to keep in mind.
-
These used to be everywhere in surplus stores, but now they are far less common. I think they were often referred to as "push-on, push-off" switches. They may also be called "latching push button switches". Here's a link to a similar switch http://www.allelectronics.com/make-a-store/item/pb-229/dpdt-push-on/push-off-switch/1.html
-
What Ian says is correct. A bit more detail: The DTS2 board provides a "modified sine wave" output that can be used with an external filter/amplifier board to produce 400 Hz power expected to be on the order of 30 watts. If you have an instrument with several synchros and the total power demand of that instrument is less than 30 watts then you should be able to use one DTS2 board to drive one synchro input and a filter/amp board, and additional DTS2 boards, synchronized to the filter/amp board, to drive the additional synchro inputs of the multi-synchro instrument. If the multi-synchro instrument requires more power than about 30 watts then you need a separate source of 400 Hz power. However, there's nothing to say you couldn't build a more powerful filter/amp board. The one I'm planning is based on a pair of LM1875T audio power amps. They cost about $3 each. The LM3886 costs $6~7 and handles about twice the power, but remember you still have to pay for the DC power supplies feeding the amps. This isn't the most efficient method of generating 400 Hz power, but uses readily available parts and does produce clean power. If you have a lot of synchro instruments, it's probably worth tracking down a 400 Hz power source.
-
A brief update. Synchronization has been implemented. The DTS2 board will synchronize itself to an external 400 Hz source, and will switch to its internal timing if the external reference is removed. This simple sounding function took a surprising amount of time. The synchronizing function is basically a feedback circuit. Not too many eons ago I took a feedback and control class, and thought I did pretty well at it. Of course that was done with continuous variables and with the expectation that applications would be continuous voltages or mechanical positions. The synchronizing function is controlling a digital oscillator (a counter inside the PIC) using a rather low resolution 8-bit micro and binary arithmetic. Took me awhile to figure out how to begin to model the dynamics of the control loop and how to stop it from bouncing around. If it worked the first time, I guess it wouldn't be any fun. The next step is verifying the serial control input functionality. This is "proven" code lifted from earlier projects. What could go wrong? To find out, I've written a simple Arduino sketch...
-
There is a huge range of possibilities. I suggest you decide where on the "reality scale" you want you project to sit. Do you want an exact copy of a real cockpit, or are you looking for something a step above a joy stick, mouse, and keyboard, or something in between? Another way to look at the same question is to decide if you primarily enjoy the building and look at the flying as testing and validation of that building, OR do you just want to fly with a bit more realism? And of course, yet another way of looking at this is to check your bank balance. In this hobby "DIY" does not mean inexpensive. Much of what you need to know about electronics can come from the Arduino site (arduino.cc). Yes, there is a great deal you can do if you know lots about electronics, but the Arduino is increasingly a central component for interfacing everything from switches to instruments. Buy an Arduino and work through a few of the samples on arduino.cc, and take a look on this site at the fantastic things people are doing with the Arduino. Equally (or more) important is looking through the projects here. See what people have done and decide how close their projects are to what you want. People have posted here not only to ask for help on their own projects, but also to share their problems and solutions with others. So, let me emphasize again the importance of reading the material on this site. Many, if not all, of your questions are answered here somewhere. Yes, there is a lot to sift through. Regard it as a necessary part of your project research.
-
A progress update: A design goal of the DTS2 is that it can be optionally used with a 400 Hz power supply, or that it can be used to drive a filter-amplifier combo that produces limited amounts of 400 Hz power. The second option is useful if you have a small synchro gauge and don't have a separate source of 400 Hz power. Since the cost of filter-amplifier combo looks to be perhaps $10 for semiconductors and $2~20 for the bare board (depends on quantity, source, etc.) this second option has a certain appeal. The first option, however, looks useful when you do have a 400 Hz power source, or you have a need to interface an instrument with multiple synchro inputs. Both of these situations requires that the DTS2 boards be able to synchronize with an external 400 Hz timing reference. Developing the synchronization functionality is what currently occupies my time. At present, it works but has an annoying amount of bouncing about as it responds to changes in the reference signal timing. Looks like a great application for a phase locked loop or for a PID controller. Unfortunately I'm working with an inexpensive 8 bit micro lacking multiply-divide capability and a somewhat vintage brain which is increasingly refusing to remember classroom discussion from the distant past. Still, progress is happening, and it is fun.
-
Wow! Very nice.
-
@Ian. The filter has four stages which is overkill. You get a fair waveform from two stages, but the cost of going from two to four is almost zero. Both filter channels together require only a single quad opamp. The passive components are surface mount devices costing pennies. @Gadroc. There are $15~20 in semiconductor devices on the board along with a few dollars worth of passives. The bare board can cost anywhere from $2 to $20 depending on quantity, lead time, and choice of manufacturer. It's double-sided, 9.5 square inches. The board has a pair of power amplifiers which need heat sinking. I'm planning on mounting the board(s) on a chunk of sheet aluminum along with an Arduino which will act as PC interface as well as provide any needed local processing. Re scopes: I used Tektronix scopes throughout my career, though toward the end I was spending a lot of time squinting at a logic analyzer. Tek gear started showing up frequently at swap meets and I picked up a pair of Tek454 scopes for about $35 each. (I must admit it almost broke my heart to see ten or so Tek 7000 series scope mainframes sitting in the dust at an outdoor swap meet. They had been the elite, high end scope of choice.) I've never gotten around to buying a DSO. I suspect the smaller size and weight will eventually be what gets me to do so. The '454 was the portable field scope of its day for a great many, but that was only when compared to 50 pound scopes on large four wheel lab carts.
-
Project update The test board is together, and so far not smoking. I've got a chunk of software running on the PIC and have successfully exercised the core functionality of the board: producing 400 Hz sine waves with varying amplitudes. The DACs are actually producing a "modified sine wave" which is marketing double speak for power inverters that produce really crappy waveforms. The reason for making modified sine waves is that it's far easier than making pure sine waves. Turns out that filtering can make a very nice sine wave from it. The top trace is the modified sine wave. The bottom trace is the cleaned up waveform that will make its way to the synchro. I have a few more functions to add to the software then I'll solder the power amplifiers to the board and see what a synchro thinks of the board.
-
Thanks, yes I've been following that. I think the Tested guys also have something about it on their Youtube channel. A few years back one of the Microsoft researchers posted a few short videos demonstrating some of the core functionality of the approach. I can't recall which HMD he was using, but I think the viewpoint tracking was aided with a MS Kinect. He had a virtual helicopter hovering over his coffee table. As he walked around the table the imagery he saw was adjusted to his shifting viewpoint providing a 3D walk around.
-
Once you have adequate processing power and the ability to accurately determine the viewer's physical perspective you can do all sorts of really, really neat things. Several years ago there were academic projects that used chroma-keying and trigger symbols in the visual environment coupled with head mounted cameras and displays. The cameras provided the computing hardware with an "awareness" of the viewer's field of view and the trigger symbols and/or chroma-key indicated what and where to paint chunks of virtual reality imagery. For example, you might have a sim cockpit with green board for windows. If the "window had, say, an "@" on it, the VR image was the front exterior view. A "1" might indicate left side view. IIRC, the position of the viewer was calculated by using the images from the head mounted cameras and an knowledge of how the room was laid out. What we're seeing today is a continuation of that research effort enabled by the confluence of low cost, high accuracy head tracking, cheap processing power, and cheap display systems. There are several companies pursuing their versions of how to make the next great thing. I'm pretty certain that we'll see a number of really neat & shiny things. I'm far less certain any will actually be more than a modest market success, but I do expect it to be fun watching the show.
-
The topic of virtual reality and augmented reality in flight sim pops up frequently, generally with discussions about its feasibility, and how physical cockpit components might interoperate with head mounted displays. L-3 Link delivered such a system to the US military for training about a dozen years ago. I'd vaguely remembered reading about it, but couldn't find where I'd read it. I finally ran across it again, and given the VR/AR interest here, thought I would post about it. The system is called Aviation Combined Arms Tactical Trainer (AVCATT). Here's a link to a video. https://www.youtube.com/watch?v=f1jgGuOi49U The cockpit description starts at about the 5:30 point.
-
Lars, On the off chance that you have not seen these documents, I thought I would mention them. They are old military standards that provide information about panels. They can generally be found with a Google search. MS25212 Control panel, Console type, aircraft equipment, basic dimensions MS25213 Control panel, aircraft equipment, typical installation MIL-C-6781B Control panel: aircraft equipment, rack or console mounted MIL-C-81774A Control panel, aircraft, general requirements for MIL-F-25173A Fastener, control panel, aircraft equipment MIL-M-18012B Markings for aircrew station displays, design and configuration of MIL-P-7788F Panels, information, integrally illuminated Keep up the great work.
-
The test board is now assembled far enough for debugging. I left the power amplifiers off so a heat sink is not needed. I also left the RS-485 receiver off as I'll simply be stuffing a TTL level signal directly into the micro controller. While this is largely an SMD project, I have used a few through hole components. In some cases I had a surplus of through hole versions on hand. A few other components were only available in through hole packages. And in one case, even though I have the SMD version on hand AND the board is designed for the SMD part, I used a though hole part because when I started assembling the board I remembered what a pain in the butt soldering that particular SMD package was last time I used one. Next step is completing the firmware.
-
My early results with self built and cheap programmers were definitely mixed, but the PICkit2 always worked. I've recently bought a PICkit3, though I haven't used it yet. I should have some experience with it in the next few days.
-
Yes, I've seen it. We're taking different approaches.
-
I built the assembly in stages on a flat piece of MDF. I thought I would have to fasten supports to the MDF to hold the aluminum in alignment, but that proved unnecessary. I simply clamped the joints until the epoxy set. The major problem was squeezing too much epoxy from the joints, something I did not realize until the assembly was completed. When a glue joint is too thin it is not resilient enough. I've had a few joints pop loose. This surprised me because I built a small test article that supported my full body weight. This is the reason I'm leaning toward Extreme 310 in the future. The completed structure without anything mounted in it will flex roughly 1/8 inch from an approximate 50 pound load applied vertically. I expect adding the panels will reduce flexing to almost nothing. I build the assembly from 0.125" thick 6061T6511 aluminum bar.
-
If you want to go highly realistic you can build up a MIP frame from flat aluminum stock as shown here: http://mikesflightdeck.com/oldnews/oldnews_2011.html (scroll down a bit to where the A10 MIP pictures are.) I used epoxy with fair results. If I did it again I would likely use Extreme 310 structural adhesive.