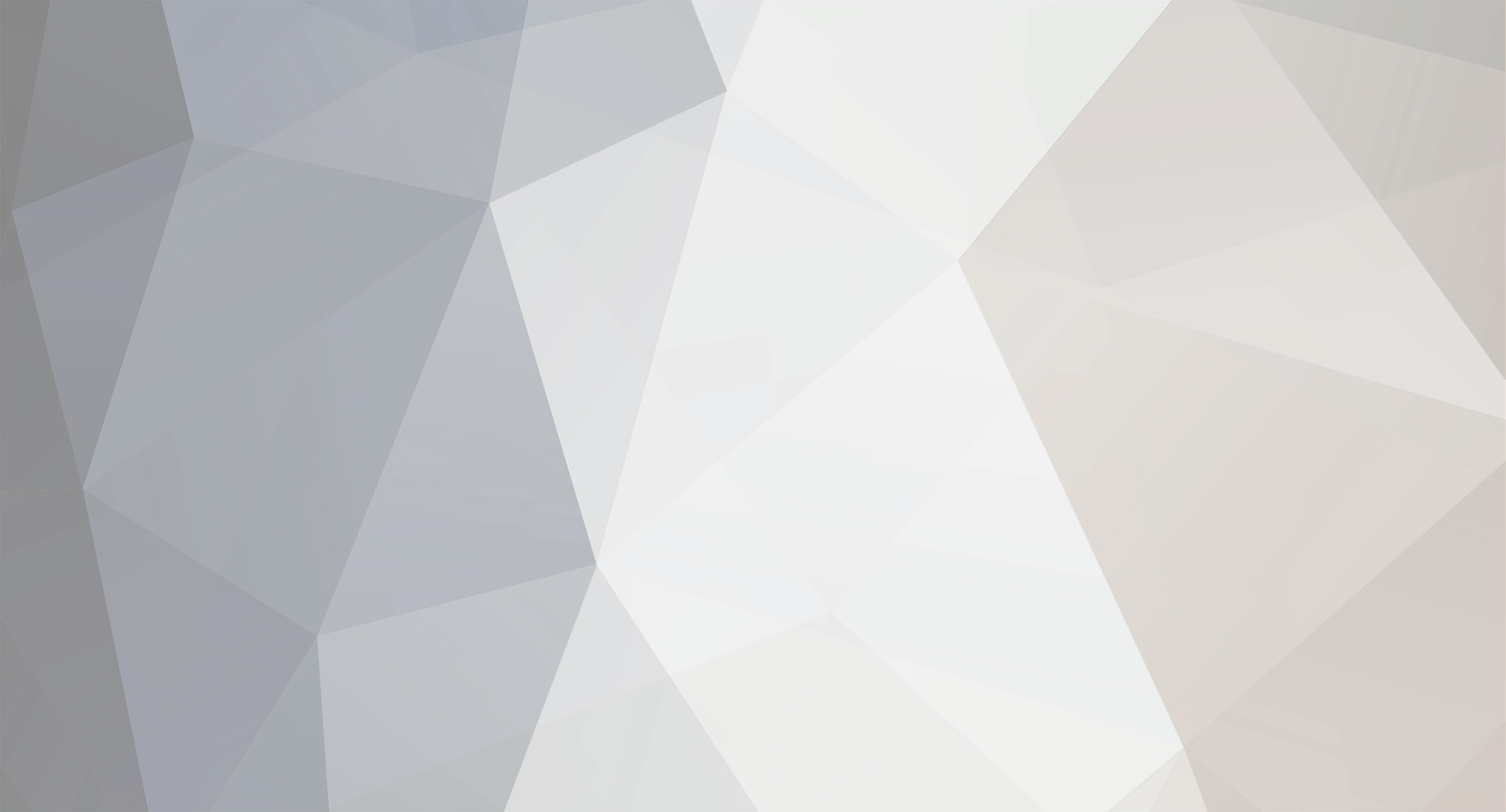
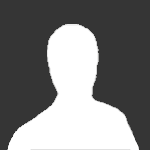
Total
Members-
Posts
546 -
Joined
-
Last visited
-
Days Won
1
Content Type
Profiles
Forums
Events
Everything posted by Total
-
Sorry Deadman - not doing this for drama, but good a natured ribbing and laughter: It's the fourth return on that search - :megalol: Excellent find though! That one should be in a "home cockpit parts sources" thread :)
-
Ask Cali, Tweet, Rugg, Or Grimes - I could go much further with that one and definitely make it much more perverted.....but I don't wanna get slapped around for breaking the forums rules :D Back on topic though - OFP and the ArmA series have always been fun. OFP was the first of it's type and many take the purist stance when it comes to OFP since it busted their cherry for warfare simulation. It's the same argument as Starseige: Tribes vs Tribes 2, Unreal 1 vs Unreal Tournament, etc etc and so forth. The ArmA series has it's bugs and shortcomings, . So did OFP. Any game that is ambitious enough to take on that many elements of the battlefield in a simulation aspect is going to have shortfalls due to hardware and engine limitations. As a former R&D tech who worked night & day for software integration, I accept that. Many who continually complain and critique are not developers have not experienced the absolute frustration of fixing one thing only for that single fix to break 50 other lines of code and do not know the countless weeks that go into successfully achieving just a few of the items on the "To Do" list. Since I do not always use Steam to launch my games (I prefer retail boxes myself), I cannot tell you how many hundreds of hours I have poured into OFP, ArmA, ArmA 2, and ArmA: OA. That's hundreds of hours EACH, not combined. I've played each one as it's own game without constantly comparing it to the previous title. While I have my reservations about BIS going for a more "near future" type approach by using more experimental and "drawing board" weapons and vehicles, I do think it is a very ambitious undertaking that, if done right, could be just as much fun as the previous titles have been. I say that because we have played for years using M-16's, M-4's, AK-47's, Mi-8's, Humvee's, etc and I would expect these weapons to be in ArmA 3 as well. If BIS continues to rehash the same inventory, then people would continually complain for the lack of new weapons and vehicles. In an era where many games are centered around the "near future" of weaponry, not one of them has come anywhere close to being a simulator. It's all been arcade. Having a "near future" game set up more as a simulator than a game, is a risk that I applaud BIS for taking. Personally, I wouldn't have the balls to do that. Designing realistic ballistics and behaviors to items that very little data is available on can be the equivalent of standing in the frying pan and hoping nobody turns on the stove. If they can pull it off without dumbing anything down and improving the AI, then A3 could be one helluva fun and immersive release. Compared to OFP and ArmA 1, A2 and A2:OA's AI are much better and neither were dumbed down from previous releases. I do miss tank interiors from OFP, but the lack of them being there does not mean that the tanks have been dumbed down. Besides, as always, the community mods will pour forth for A3 and it will become many different genres of warfare just as the previous titles have been. The sandbox has been the best feature out of them all. I still await the day when hardware advancements could finally allow BIS and ED to make a full out flight & ground combat simulator (hell, Naval too for that matter!). Until then, I'm just glad that there's still great titles coming out for PC since I do not own, and refuse to own, a console platform of any type lol!
-
The Simpson and the ole Tek 465.... Ahhhh. Brings back many memories there. I can't tell you how many hours I have logged into each of those since becoming a tech 25 years ago. Just seeing the 465 makes me realize I could still operate the controls without have to looking at them lol!
-
I use to work research & development for avionics (fighter aircraft). I would make the first versions of our mock-up or prototype panels. Plexiglass or arcylic would be the better options for your panels than wood. Use wood for the housing. Print out your panel drawing and tape it to the plexiglass and cut it out using the paper as your guide. Cut the panels themselves using a simple variable speed jigsaw. Use a blade made for soft metals and keep the blade speed on the slower side. The faster the blade speed, the more the pastic will melt instead of actually cutting. Once cut, you can leave the paper on so you can drill your holes. Now, when it comes to labeling, here's a trick I used to use in the lab when making a prototype: First, sand the front side of the panel with a fine grit sand paper. This will diffuse any light from backlighting. Stick small pieces of tape to your panel where the text will go. Once in place, paint your panel black. Once dry, pull off the pieces of tape so there will be a clear "window" where the label for each switch will go. Go to an office suply store and look for some self adhesive, clear labels. Here's the ones from Avery (Click Here). Print the panel onto one of these wuith a laser printer ensuring that you have thje panel color set to black and the font color set to white. Once printed, cut the panel out from the sheet, peel off the back, and then stick it onto the front of your panel. Voila! A cheap and easy way to have a backlit panel with labels for switches and knobs. It won't look "pro" but it will still look pretty cool. Here are some prototypes I made for a project I never really went all the way with. I used the above easy method. And a crappy pic of how it looked when the black-lights were turned on )FYI - I was using only 2-3 bright LED's for the back-lighting and had it set up so I could use blue or red): I used a 12V un regulated power adapter. I made a small regulator board using a 7805 (+5VDC regulator) and a couple of electrolytic caps. All together, the adapter and the regulator PCB materials cost less than $15 USD. I still use it when I play LOMAC. I have it mounted in a small enclosure next to my desk with some slide rails on the panel housing. I slide it wout when flying and slide it back into it's hiding space when I am not. There's enough room on the bottom half for my manuals too :D This was my set up when i still had three monitors. I am back down to one monitor now, but not upset about it. My wife felt sorry for me when I gave up my triple set up and let me get a much bigger monitor :D
-
Hehe, considering I perform component level troubleshooting and repair on circuit boards for medical equipment, it's kind of required I do quality work. Lives depend on it :) Before you go doing anything rash - Does the power light come on but the display just does not display a picture? If so, then the backlight inverter is most likely bad. Most of the time, the FET's on the inverter are bad and maybe an tantulum or electrolytic cap. In unlucky cases, the transformer is bad as well. If you lived in the US, I'd just tell ya to send me the monitor and I'd take a look at it for you. Could just be a bad solder joint. No way to tell without being able to look at it under my microscope. Generally, in LCD monitors, you will have +5VDC, +12VDC, and -12VDC. I've seen some LCD's have the +/-12VDC set to +/- 15VDC. Just depends on the design. If it uses an apater style power supply, it's probably going to be an unregulated power supply judging from the components in the lower right hand corner of the circuit board pic you posted. So, if it's 12VDC unregulated, you could see up to 18VDC if there's not a load connected. Multimeter's aren't that hard to come by. Most auto parts stores carry them as do many hardware stores. You can get a pocket sized one pretty inexpensively these days :) Thanks for posting the pic though. If I ever get a Lilliput monitor, then I know I'll need to go in and clean up that mess of a solder job first LOL!
-
Those are just choke coils and their coated with a non-conductive conformal coating. Looks like they were coated (very sloppily) after installation. Cleaning the board with a small brush and 91% isopropyl alcohol could possible yield some results, but it would be hard for me to say just by looking at a photo of the board. Overall, it whoever populated the board for Lilliput performed a really crappy solder job on everything. If the electronics lab I run put out something that looked like that, they'd fire me and every employee too. Is that the only circuit board in the monitor?
-
Unfortunately, the lack of protection means we have to deal with more exploiters/hackers in the servers. Without sufficient anti-cheat an exploiting client can crash the server in seconds. Battleye is ok in some aspects, but falls short in many others. Better copy protection would help alleviate some of this. Not all, but some and any is better than none. And ED doesn't bog their games down with the full out Starforce. Only the essential portion of Starforce needed for copy protection is needed. All the other crap that gets loaded in many other SF equipped games is not present in FC2 or DCS series ;)
-
^^^^^^^^ AAAAAAAAAAHAHAHHHHAHHAHAHA!!!!!!!
-
purchase advice on a 10 " monitor w/mfd
Total replied to rogueone's topic in PC Hardware and Related Software
Unless you are buying two, then it will not work. The monitor screen size is determined from corner to corner, not side to side. The MFD's measure 10" on the inside of the two outter bezels when placed side by side. The actual width of the 10" LCD monitors is closer to 9.7" and that includes the bezel of the monitor, so you'll only have about 8" or so actual viewing width. -
Take On Helicopter - New game by Bohemia Interactive
Total replied to Eight Ball's topic in Chit-Chat
Well, not everything can be that high fidelity. At least in the one from BIS, trees will kill you :D -
I dunno about it being just Saitek. My first stick was a Logitech and it drifted far to the left and resetting it was the only way to fix it. I bought a new one of the same model and it started doing it right off. Almost every time I hear of a joystick of any make/model losing its center calibration, it's always been to the left. There was a time when the cursor on my desktop would slowly drift upwards without warning. Isolated it to the ministick on my X52. I had to move the ministick to get it stop moving my desktop cursor. Was annoying as heck! By circumstance, I was going to be reformatting my system around that time, so I decided to see what impact that would have. I haven't had the problem since....and that was several years ago. Sometimes, I think these issues are not faulty hardware, but a miscommunication between the device drivers, the USB firmware, USB Drivers, and the OS itself. The manufacturers of the hardware rarely make the USB firmware from scratch. They usually use an SDK released by the component's manufacturer as a starting point. Such issues can the fault of the joystick manufacturer. It could also very well be a problem with the firmware SDK or a problem within the OS architecture itself and out of the hands of the joystsick manufacturer. We may never though....
-
Knowing you plan on etching your own PCB's, I still thought I'd post a hint from someone who, as an electronics technician, has dealt with more wiring of breadboard designs than I care to remember lol For the wiring coming off the board, pick one side of the board and work across it laying your wires flat on the board towards the exit side. Laying them flat will prevent breaking of solder joints. As the solder ages, the stress from the wires being perpendicular to the board will cause cracked solder joints or can even create an open in the wire beneath the insulation (if the solder wicked up the wire beneath the insulation). Work from the outside edge of the exit point inwards - no sense in trying to solder around wires if you don't have to. As you solder them on, bend and route the wires so you group them together at the exit point. There can be more than one exits point btw. On the board you pictured, there would be both right and left exit point. This way, you can then zip tie the wires after they are all soldered on. The bending and routing of the wires will not only neaten up the appearance of the board, but also allow you to solder on the board without having to jam a hot iron down between wires that are sticking out everywhere. Done correctly will minimal stress on the organized wires, a perf board (or prototype board) design can last just as long as a printed circuit board with plated through holes. I'll see if I still have any old project boards laying around from back when I enjoyed tinkering. If I still have any and I find one, I'll post a pic of what I described above :)
-
Also, let me add this in: My X52 goes off axis to the left occasionally and has since I owned it. With the USB cable still plugged in, unplug the cable that connects the stick to the throttle. Leave it unplugged for about 2-3 seconds and then plug it back in. That always corrects it for me on the X52 and I have seen some reports (that went largely ignored) saying it works on the X65 as well. ...and always do some research on a highly expensive product before buying. Research both the good and the bad ;)
-
CONFIRMED: Next aircraft will be a fixed wing US FIGHTER!
Total replied to kingneptune117's topic in Chit-Chat
@Mower - ya buttnugget :D @ GG - ROFL We lost on Harrier while I deployed, but it was not due to a bird strike nor enemy fire. The pilot did not know there was this large object in front of him called a mountain. It was daytime and he had his FLIR off. Cloud cover around the peak limited visibility and he smacked into full speed. It pretty much turned to very small pieces very quickly. I just found it odd that none of his wingmen said anything like "Hey dude - uhm, mountain ahead!" Maybe he owed them money and never paid the debt.....lol -
CONFIRMED: Next aircraft will be a fixed wing US FIGHTER!
Total replied to kingneptune117's topic in Chit-Chat
I have to disagree there. I was in the first Gulf War aboard the USS Wasp LHD-1. We were diverted from the main scene to assist with the Kurdish refugee exodus. In all of our operations, our sister ship which was the USS American CV-66, did not operate with us hardly at all. The CV's and CVN's were primarliy in the Red Sea and the Persian Gulf with their aircraft enforcing the No Fly Zone and going after targets of interest. Close air support for the Marine Amphibious Readiness Group 2-91 and CAP patrols for the immediate area was provided from our own flight deck. No F/A-18's or A-10's came to play. We were in the envelope for CAP, so there were F-14's and F-15's flying at around 30K within 100-250nm, but they were enforcing the No Fly Zone, not assisting ground troops. The AV-8B Harriers and AH-1 Cobra's did their job of ground support as well as the AV-8B's providing immediate air control of the area. The AV-8B Harrier was a great little aircraft and takes pilots of a special mindset to pilot, but (as stated) it's capabilities are very limited. In 1991, we only had the night attack variant. The more modern plus variant with the APG-65 radar was released after the cease fire. Even with radar, it's still a sub-standard platform for air superiority and, with only 6 pylons, it's ability for sustain CAS missions is limited as well. In my tenure working with the amphibious navy, I never once saw one take off vertically. They just use up far too much fuel in a vertical take-off. They also have to reserve enough fuel to land since they land vertically. Unless a tanker is on duty nearby, then their range and time on station are greatly reduced due to these factors. It's a niche aircraft that fulfills that niche extremely well but, without having the ability to participate in the fight on the ground ingame to get the full appreciation for Harrier support, it wouldn't be that immersive choice of aircraft for the next DCS module. It's great fun to fly CAS in the harrier in ArmA2 as you are working with the ground troops, but (imho) would have a short-lived tenure in the DCS series and that's not a wise business decision. -
Utes is the island off to the South of Chesnarus. Which mods are you using? Also: Are you running ArmA2 and OA in combined ops mode? Are you running the box version of ArmA2 and the Steam version of OA? This will help isolate a possible answer :)
-
Problems with X-52 + CH Pedals
Total replied to DarkFire's topic in PC Hardware and Related Software
I have the same set up. Make sure you have the latest drivers loaded for the pedals. To map the axis to the CH Pedals, you have to click the box for that axis in the CH Pedals column in the options, not the X52 column. Then move the axis on the CH Pedals you want. Don't forget to unmap that axis from the X52 by selecting the box in the X52 column and clearing it out. I have my rudder axis on the pedals and my wheel brakes as well. If you play ArmA2, the pedals are also great for use with land vehicles for gas and brake ;) -
Found this one over half an hour ago. I'm still hurting from laughing to hard. I haven't laughed this hard at something on the internet in well over five years lol! http://www.craigslist.org/about/best/lax/182862349.html
-
Remember to leave the sapce around your switches to accomodate the size tolerance for your switch covers. The standard is 10%
-
Showed my wife the video & the post and she replied with this: "I guess his wife loves him more than I love you" Why couldn't I have been well hung instead of just good looking? :(
-
Now I gotta show MY wife the video AND your post :D
-
Mine is like 9.20 X 2.15. I just scaled it from sight basically for clearance around the buttons. Kinda funny that it matches up LOL! I still have to add in the master caution reset button. Slight oversight on my part lol!
-
Either your wife REEEAAAALLLY loves you or you're single! Envious setup man :)
-
Damn Red - that's gonna be awesome and I can't wait to see the video of it all in action :D Other options for design software (especialy for PCB layout): Inexpensive 2D/3D CAD - TurboCAD by Imsi Runs abourt $80 retail. Thas a PCB library, but I find it inefficient to use for PCB layout. Schematic Capture & PCB Layout - Diptrace The free version is limited to 500 pins & the pcb layout has an auto router. Schematic Capture & PCB Layout - ExpressPCB. You can print to file (good when etching your own) and export dxf files. You just can't import dxf files. Also, no auto-router, but unlimited connections. (heh, Deadman posted his link after I posted this lol! Gret minds think alike lol!) Making my own UFC. Nowhere near as authentically pretty as Red's, but I'm going for placement and function over authenticy in order to keep my costs down. Already have an X-Keys USB Matrix board, so going to use that for the interface. Rough render of the panel I'm building (done in TurboCAD 16):
-
I , personally, have had a TIR4 TCPro for going on 3 years now. Haven't broken it and use it pretty much nightly. My friend's broke one of the fingers from it as well. I took a good look at it and decided to do the following. There is a small gap between the clamp housing and the back of the trackclip. I put 2-3 small washers into this gap. This pushes the trackclip so it sits on the hole that the fingers normally went into. I used some sand paper to rough up the area of the clamp holder around the washers. Then I used a little JB Weld to glue the washers in place beuing careful not to let the glue touch the trackclip. He can now still move his trackclip as always. I'll ask him to take a pic of it one night and send it to me so I can post it.