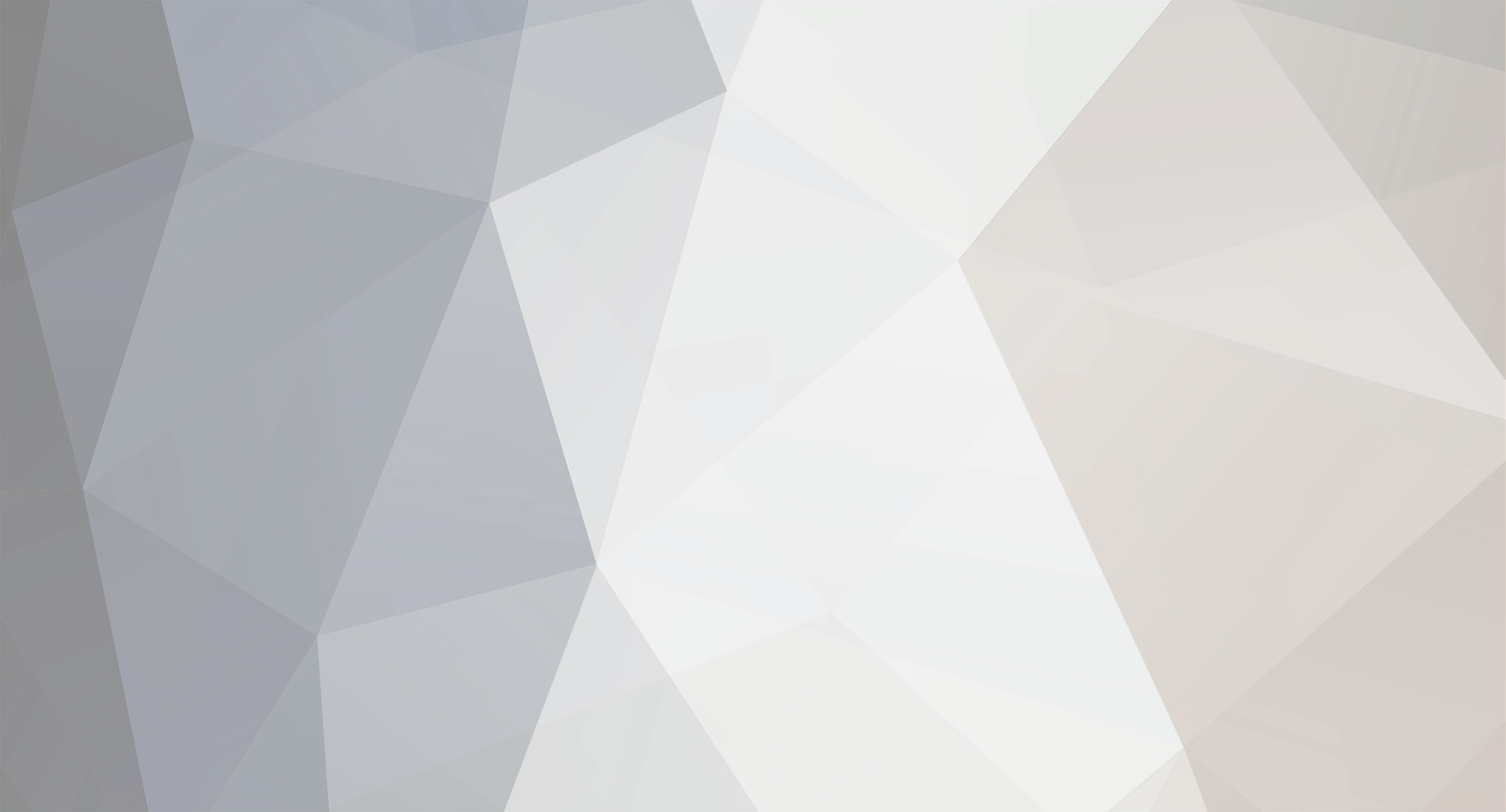
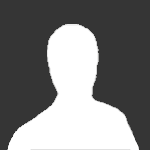
Ranma13
Members-
Posts
564 -
Joined
-
Last visited
Content Type
Profiles
Forums
Events
Everything posted by Ranma13
-
The two fat wavy pins on either side are locking pins used to secure it to a circuit board. The side with the 3 pins are the two 'buttons' that get momentarily pressed when the encoder is turned. The middle pin is the common, and the left and right pins are for the two directions the encoder can be turned. The two pins on the other side are for the push switch. The encoder can be thought of as 3 separate switches, one for the clockwise direction, one for the counter-clockwise direction, and one for the push. You can hook it up to any programmable microcontroller. Leo Bodnar is a popular choice, but personally I find it to be extremely expensive compared to either an Arduino or a Teensy, and it can't be integrated with DCS BIOS. If you're going to use DCS BIOS, it's not important whether the microcontroller can emulate a joystick or a keyboard, you just need to make sure that it has a serial port, which the vast majority of them have. You install DCS BIOS, then run the command-line app that comes with it, and it will handle the connection between the microcontroller's serial port and DCS BIOS.
-
I would love to have the room to get a CNC mill like that. Currently, I have to use CNC milling services, which gets expensive very fast.
-
As an update to my previous post, I was able to squeeze the Teensy 3.2 into the throttle lever, even with 28 headers soldered on. Only 8 pins are needed: 2 for power, 2 for I2C, and 4 for the force sensor, but I've had this Teensy for a while now so all the pins have headers. It's a tight fit inside the throttle and I had to turn it sideways to clear the screw holes, but it does fit. I also played around with the clock speeds. At 96 MHz, 72 MHz and 48 MHz, the Teensy has no problems communicating with the throttle, but at 24 MHz and below it completely doesn't work. I also tried the ATTiny85 at 16 MHz. Surprisingly, the throttle does receive something from it, but it seems to be garbled as the axes just jumps around to random values despite me sending it a fixed value every time the throttle requests data. My shot-in-the-dark theory is that the throttle is toggling between reading the X value and the Y value on a fixed clock, and if the I2C slave doesn't send data over fast enough, the throttle just ignores it. In any case, I set the Teensy to 72 MHz and just used map(analogRead(pin), 0, 1023, -128, 127) and send this directly to the throttle. After using the calibration tool, the throttle will properly take into account any off-center drift, and will also scale the calibrated value to go from -100% to 100% so that, for example, if your sensor only goes from -50 to 50, this is scaled out correctly and you still get the full range (albeit at a lower resolution). You can do these things within the Teensy as well, but it doesn't seem like it's necessary. Speaking of calibration, I did run into one issue. I couldn't get the slider axis (the gray friction lever) to calibrate properly. It would be fine going from center to 0%, but from center going up, it would only get to around 53%. I first thought that the pot went bad, but after graphing its output voltage on an Arduino, it turns out it's completely fine. After wracking my head for options which included replacing it with a hall sensor and asking Thrustmaster for a new controller board, I stumbled on an unlikely solution: calibrate the axis backwards. When the calibration tool says to move it to INCR, I moved it to DECR, and vice versa. This seems to have done the job and I've regained the full range of the axis. Not sure if anyone else has run into this issue, but I hope this info helps anyone that does. One other nugget that might be useful: if you want to use the slider for something like radar elevation, but don't like how it has a fairly wide deadzone around the center detent, just set TrimCenDZ to 0x00 in A10_calibration.txt before calibrating. This gets rid of the deadzone. For the Ultra 462 force sensor, I also picked up the matching concave joystick control knob. RS Components sells it on their website, but if you're trying to buy it from the US, they'll redirect you to their US partner, Allied Electronics, who doesn't carry it. I ended up working around this by selecting "Other Countries" under North America on their region selection page, then purchasing it from that site. They will ship it out from the UK with no issues. Here's the direct link for anyone who's interested: https://export.rsdelivers.com/product/ultra-electronics/3625012-3/concave-joystick-thumb-control-knob/0419665 It costs a pretty penny at $50 USD and $20 USD for shipping, but it saves you from having to 3D print a hat and tap it for set screws, and it also looks very similar to the real deal. The set screws it uses needs a 0.9mm hex key though, and I never realized there exists a hex key this small. Bottom line is, if you want a force sensor and if Delta ever does another run, jump on it. Doing it by yourself requires a serious time commitment, the proper tools and components, and the know-how to put it all together. I was eyeing the force sensor ever since he listed it on eBay, and through the first and second runs. By the time I decided I wanted one, they were all gone, and I had to build one myself at high expense. For the price he was selling them for, he was practically selling them at cost. He's not doing this to make a buck, he's doing it because he wants people to have a useful slew cursor.
-
It rotates 50 degrees from minimum to maximum.
-
Delta was nice enough to send me the Shapeways link for the force sensor holder, which I got printed. It was slightly too large to fit in the throttle hole so I had to sand down the sides, as well as the keyway for the force sensor (the little part that sticks out to prevent the sensor from rotating). I think this is because I got it printed on professional plastic instead of versatile plastic. I also picked up a used Ultra 462 sensor on eBay. The solder lugs are clean, but it was obviously used and has tool marks on the locking ring. I suspect that the sensors are rejects and hence why they're selling for so cheap; my Y axis is off-center by about 3-5%. However, this is easy enough to correct in code by measuring the offset and applying a correction every time the axes are read. I've also tested the sensor by itself running through the Arduino as well as through the throttle. You get more sensitivity and control through the Arduino, particularly around the center point when trying to do small movements, but it's minor enough that most people wouldn't notice unless they tried the two back to back. In particular, the throttle will apply a deadzone to the sensor even if you set the deadzone setting to 0x00 in the throttle calibration tool, and this is what makes it feel less sensitive around the center. In general, the sensor works fine through the throttle for the A-10C and Falcon BMS. However, the Ka-50 has a particularly twitchy sensitivity for the Shkval, and I found that the extra sensitivity through the Arduino makes a pretty big difference in how well you can control it, especially since you can remove the deadzone in the Arduino. I'm running into an issue though. I picked up an ATTiny85 (specifically the Adafruit Trinket 3.3V), but the throttle won't recognize any of the I2C messages it's receiving from it. I tried the same code on a Teensy 3.2 and it works just fine (just with the Wire library swapped out). I think this may be because the ATTiny85 doesn't have a true hardware I2C, rather relying on the internal USI (Universal Serial Interface) to emulate one, and this is somehow incompatible with the I2C master on the throttle. I don't have an oscilloscope or a logic analyzer though, so I can't be sure. All I can tell is that it looks like the ATTiny85 is sending over the bytes for the X and Y axes properly, but the throttle continually asks for the bytes whether I send something or nothing, which makes me think it's a timing issue despite the throttle controlling the I2C clock. I'd use the Teensy since that definitely works, but unfortunately it doesn't fit inside the throttle handle. I'll have to play around with it some more before giving up. My backup option is to pick up the Adafruit Trinket M0, which uses the Atmel ATSAMD21 chip that, as far as I can tell, uses a true hardware I2C.
-
The shell needs to be around 8mm thick, and it's hard to source acrylic in that thickness unless you stack panels on top of each other. 3D printing is also an option, but any threads will have to be tapped and the plastic won't stand up to repeated screwing/unscrewing. Aluminum can not only be tapped and be repeatedly used without much wear, but it also has very tight tolerances. That said, I haven't decided what material to use yet for the shell because I'm focusing on getting the front panel made first.
-
A minor update, I'm still modeling out all the parts, and I've started communicating with some vendors besides Front Panel Express to see how much it will cost to manufacture both the front panel and the shell. It's looking like it's gonna be $150-$250 for the front panel and $150-$200 for the shell no matter which vendor I go with. One area that's harder than expected are the thumbwheels. I found the manufacturer of the actual thumbwheel, and they have a surprisingly detailed datasheet with lots of useful dimensions: https://www.consolite.co.uk/air/control-potentiometers-and-encoders/ https://www.consolite.co.uk/wp-content/uploads/2018/02/Data-5-Thumbwheel-Potentiometers-Iss-7.pdf I'd need to adapt it so that it can be used with potentiometers. On the actual ICP, the thumbwheels are mounted to the backplate, and the thumbwheel is offset forward so that it's centered with the ICP: Redneck gets around this by mounting the potentiometers inside of the ICP shell so that it's already centered. The upside is that this is a cheap and effective solution, but the downside is that due to how close some of the buttons are to the edge of the ICP, you're limited in what kind of potentiometers you can use; namely, low-profile side-addressed PC-pin ones. This isn't completely off the table for me, but I'm still weighing some other considerations such as whether I want physical switches or not, how the potentiometer itself feels (the smaller they are, the lighter they feel when rotated), how thick I want the thumbwheels to be versus how thick they have to be (too thick and they won't fit within the Polycase LP-70P and I'll have to find a new enclosure, but too thin means I'm severely restricted in which pots I can use), and whether I want to go with a two-piece design that mirrors the look of the real thumbwheel or a single piece that slips onto the pot stem and looks close enough.
-
You can adjust which axes are used in the controls settings. Pick axes from the dropdown and remove whichever binding you don't want to use.
-
Thrusmaster Warthog throttle wiring required
Ranma13 replied to MrPiper's topic in PC Hardware and Related Software
I don't know about the left throttle, but the connectors in the right throttle uses Molex PicoBlade connectors. Best place to buy them from is eBay, where they come with the connector and the cable together so that you don't need to crimp them yourself -
Increasing sensitivity of joystick pot
Ranma13 replied to CptTangerine's topic in PC Hardware and Related Software
Yes, the degree of travel. Potentiometers are voltage dividers, they take an input voltage and give you a value between 0-100% of that input voltage. The resistance is only to limit the current running through it so that you don't suck up too much power. This doesn't matter too much for USB devices, so just try to match the 50K resistance. Theoretically 10K would be better because the higher the resistance, the more subject it is to circuitry noise, but it might not be a good idea to suddenly increase the current draw by 5 times if you're not sure the circuit board can take it. -
Increasing sensitivity of joystick pot
Ranma13 replied to CptTangerine's topic in PC Hardware and Related Software
The issue is that you're not using the entire travel of the pot, and you're using only a small portion of it and extrapolating it to a full range. All pots have some inherent jitter to them, and increasing the sensitivity will also increase the jitter. You could replace it with a more expensive pot, but it's best to try and find one that covers your new angle of travel instead of using only 30 degrees on a 150-degree pot. -
NEXT LEVEL MOTION PLATFORM V3
Ranma13 replied to lasvideo's topic in PC Hardware and Related Software
How does the motor notching feel? Some people are saying that they can definitely feel the discrete steps, and others aren't saying anything at all, so it's hard to get a clear picture of what it actually feels like. Also, does it add a lot to the sim? I have the JetSeat and to be honest, I forget to turn them on most of the time (they don't really add much for me). Someone mentioned that the they preferred their JetSeat over the NLR V3, and I was wondering if anyone else mirrored that sentiment. -
It uses 6 wires, 4 for each direction, one for the press in, and 1 for ground.
-
I'm in the US. I've already taken a look on eBay and there hasn't been any sold recently. The last record I could find was one that was sold in 2013: https://www.worthpoint.com/worthopedia/16-icp-real-435308773
-
I've completed the preliminary drawings of how I want the panels to come together: This is without the screw holes and threading, but it's enough to get an idea of how much it will cost to manufacture. Unfortunately, even in this incomplete state, the estimate is already $300: The shell is surprisingly the most expensive part. Milling out the inside portion alone is $35, but the real price comes from the holes for the buttons. Apparently Front Panel Designer doesn't take into account whether you've drilled a cavity or not, so a 13x13mm hole in a 3mm-thick panel is $0.72 per hole, but a 13x13mm hole in a 8mm-thick panel suddenly jumps to $2.10 per hole, even though it's the same thickness with the cavity. Given the high price, I'm starting to wonder if I should go through with it, or stick with the Hispapanel for now until I can reduce costs somehow.
-
I see, I understand. Would it be possible to provide the CAD file for the 3D-printed sleeve that the sensor mounts into?
-
Thanks for the info! According to Gravograph's website, they only sell them in 0.02", 1/16", 3/32", and 1/8", which corresponds to 0.508mm, 1.5875mm, 2.38125mm, and 3.175mm. The top part of the ICP is exactly 2mm, so I'm going to ask Front Panel Express if they can shave the 3/32" sheet down to 2mm. Thanks, that's what I started from, but it's missing a lot of measurements. The beveled part on top, for example, doesn't have any dimensions and doesn't give the bevel angle, and there are no dimensions provided for the bat and the hovering cap that has the 4 direction arrows on it.
-
Some updates: I've decided to stop measuring out the Hispapanel and instead use the CAD drawings from here: https://github.com/JonahTsai/F16/tree/master/ICP This is due to several reasons. I still can't get accurate dimensions from measuring it. I'll measure the spacing between each hole and it'll match up to my drawing, but when I repeat the same measurement from the left edge, suddenly everything's off by 0.1-0.2mm. Then when I try it from the right edge, it's off by a different amount. There's also no way of adding a finger guard to the Hispapanel unless I simply glue it on. If I use a CAD file that I can control, then I can add a channel for the finger guard to sit in. I've already extracted out the finger guard from the aforementioned CAD drawings and added a 1mm extension on the underside: And uploading it to Shapeways shows that it will be quite cheap to print in either steel (~$24) and professional plastic (~$12). The Onshape drawing can be found here: https://cad.onshape.com/documents/a0dbab0389b4a3940def7514/w/2e052f0607ec455fa72986cc/e/7d7352af587dca7abebe90dc Additionally, the CAD drawings are a complete set; it has drawings for both rockers, all the buttons, and even the backplate, and the cutouts are perfectly matched for the size and height of the Otto T4 switch and Honeywell toggle switches. The only downside is that there's only 5mm of distance between the bottom of the button and the backplate: This will be an issue because if I go with a push button, they will all be taller than 5mm. This means that instead of being able to sandwich the circuit board in between the backplate and the front plate, I will most likely have to place the circuit board behind the backplate. I may even have to add in an additional reinforcing plate so that the order becomes front plate -> shell -> back plate -> circuit board -> reinforcing plate. I'm still trying to work this out though to see what would be best. I've also modeled out the Otto T4 switch: It's not 100% accurate since I can't get my calipers into the very small gaps and had to eyeball it, but it should be close enough to get an idea of how it will fit within the panel. The Onshape drawing can be found here: https://cad.onshape.com/documents/efe03f26673b12a940d2efbf/w/14b95306aeb819f8767ff750/e/044829b0aa76fe9feb6bc623 I also created a 2D DXF drawing for the ICP outline so that I can load it into Front Panel Designer (software for Front Panel Express). Adding in all the holes and text for the ICP, the estimated price comes out to ~$100 before S&H. Although it's not listed in their software, you can ask them to use a 2-color acrylic/ABS panel called Gravoply / Gravoglas: https://www.gravograph.us/products-and-consumables/consumables-and-engraving-materials/plastic-materials-for-mechanical-engraving/gravoglas-2-plex-subsurface https://www.gravograph.us/products-and-consumables/consumables-and-engraving-materials/plastic-materials-laser-mechanical-engraving/gravoply-2 I found this buried deep within their online help though, so I'm not sure if it's something that they still offer. Another concerning thing is that the only place I could find Gravoply for sale is selling it for $140 for a 24x48" piece. Though this is much larger than what I would need, I wonder how much Front Panel Express will charge me for an ICP-sized piece. If I'm unlucky, I'll have to buy the entire 24x48" panel. On top of that, this is only for the front plate. I still need a middle shell and the back plate; the ICP body may end up costing me $300+ depending on how things go. In the meantime, I'm going to continue modeling out the various parts of the ICP, as well as purchasing a grab bag of components from DigiKey to see which ones I like best.
-
RealSimulator F-16SG-HOM & F/A-18 Joysticks
Ranma13 replied to Sajarov's topic in PC Hardware and Related Software
I haven't seen any info regarding backwards compatibility with the Warthog/Virpil base, but I'd be surprised if it did support those bases. At the price point that this stick will sell at (likely >$300), there's really no point in buying one to use with the Warthog/Virpil base, since you can't take advantage of the extra buttons or the extra features that it has, and the MongoosT-50 and TM stick are at much lower price points for the same functionality. Maybe it's something that's super easy to implement and will be added in as a "sure why not" feature, but unless someone is looking for an eventual upgrade path to the FSSB R3 base, I don't see an advantage of purchasing this stick over the other 2. -
Any chance of selling the force sensor again at a higher price point? The sensor itself is still available on eBay: https://www.ebay.com/itm/462-JOYSTICK-ULTRA-MSI/292411568241
-
I'm making progress on the Hispapanel CAD drawing: You can find it here: https://cad.onshape.com/documents/fc0cbecdb84b963f470caf2a/w/a3bb88e56d58cca0c2ca2d52/e/9646fe8fff198f5e44bf12ee You will need to create a free account to view it, but I prefer Onshape because it's free, it's better than SketchUp, and it allows for exports in multiple file formats. My plan is to model out the front panel and all the components I want to use (buttons, switches, etc), and then combine them together to see how it would all theoretically fit together before I start getting things 3D printed and designing the circuit board. One thing that makes modeling the front panel difficult is that the panel is an actual item that's manufactured with a certain tolerance, whereas a CAD drawing is the ideal. For example, the button holes measure 13.5 x 13.6mm, and the spacing between column 1 and column 2 is 5.6mm, but 5.5mm between column 2 and column 3. Ideally, the button holes should be a pure square, and the spacing between the columns should be the same for all columns. I have to make a decision on whether to use the actual measured values, or go with the ideal value. 0.1mm may not sound like a big deal, but when you have multiple items that are positioned in relation to each other, it can easily add up to more than 1mm off by the time you finish placing all the components in a line. I did ask Hispapanel for a dimensional drawing, but they sent over this, which is fairly useless: It's unclear what the 3x3mm squares are supposed to represent. I assumed that the center of each square is the center of each hole, but measuring it out shows that they're more than a few mm off from the actual measured value. I will ask them again for a better dimensional drawing, but I can understand if they're reluctant to provide it, as it can be used to create clones. I also need to pick up a second panel; my calipers are doing a really good job of scraping the paint off of this first one.
-
Hey all, I originally put this post up over at viperpits.org, but since that board requires registration and the community is larger here, I decided to post it here as well. I know that there's no F16 in DCS (yet), but since the ICP can also be used as the A-10's UFC or the Ka-50's PVI-800, I figured this info could be useful to some people. I'm starting a build of a ICP because I can't find one out there that matches my requirements. Before I start, here's a quick picture of my current setup: I don't exclusively play Falcon BMS, so my pit is intended to be used across multiple aircraft. However, I do want an ICP because I can use it across several aircraft and Falcon BMS is my main sim. As you'll notice from the picture, I currently use Redneck's ICP (now known as Viper Gear). It's a great value for the price ($325 without S&H), but I do have some issues with it (note that in the following picture, I removed the two toggle switches that it comes with): 1. The backlight is uneven. The "C" in ICP is brighter than the other 2 letters, SYM, BRT, DEPR, and CONT are dim, and the numbers in the buttons are brighter than the text above it. 2. The buttons use tactile switches that have a rather high activation force. This may be similar to the real ICP, but I'm not a big fan of it for sim use. I'd rather have push buttons that are softer with more travel. 3. The 'rocker' switch uses the same tactile switches, and is a flat button that doesn't rock. I'd rather have it be a real rocker switch that is V-shaped. 4. The buttons are rather loose. When flipping the DRIFT C/O switch, the buttons will jump around, particularly the master mode buttons. 5. The backlight leaks through the edges of the buttons. As far as I can tell, on the real ICP only the numbers and text is illuminated, not the edges. 6. The dials use rotary encoders instead of potentiometers or rotary position sensors. It doesn't allow for smooth motion and will instead 'step' through the axis rather than smoothly rolling through it. 7. The front panel is a 2-layer acrylic panel that has the text engraved on the reverse side, similar to this one on Inventables. However, on mine, there was an issue where two spots leaked through (one to the right of the ENTER button, one to the right of the 0 button), so Redneck colored them over with a sharpie. This is obvious because Sharpie's look purple when placed next to something more black than it, and the spots wasn't colored over well enough so light still shines through: 8. The wires for the potentiometers are really easy to break off. I've already broken off 3 of them just taking apart the ICP, which I've had to solder back on. Cutting apart the shrink wrap reveals that the wire broke off at the point where it just clears the potentiometer leg. Even with shrink wrap, this is why it's not great to solder wires directly to PC pins instead of actual solder lugs that allow you to insert a wire in a hole to act as stress relief. 9. The DCS switch uses a standard SMD 2-axis tactile switch, but this switch wasn't really designed to be used with a lever arm. As a result, it's *very* easy to accidentally brush it and have it activate a direction without even knowing about it. I've have multiple times already where I think I'm changing my steerpoint, but I'm actually changing the UHF channel because at some point I inadvertently pushed the DCS switch. For these reasons, I've decided to build my own ICP. My design goals are: 1. Use a real DCS switch. I've already purchased it from Mouser. 2. Use Honeywell miniature toggle switches. The Apem switches that comes with Redneck's ICP feel ok, but not that great. 3. Stop light from leaking from the edges of the buttons, and have the backlight only illuminate the text. 4. Use push buttons instead of tactile switches for a better feel, even if it's not authentic. Also tighten up the buttons with some foam or other material to prevent them from rattling. 5. Make each backlight LED individually addressable in order to control their brightness independently. This will make it easier to smooth out the illumination, as well as be able to turn on/off and flash buttons individually, which will be useful when used with other sims. 6. Use potentiometers for the 4 wheels, and implement the on/off switch using software. I've looked into this, and it looks like it's impossible to use potentiometers with built-in switches. Not only are the ones with switches too big, but they will also be in the wrong position when mounted on the left side (the switch is at the full counter-clockwise position, and when the pot is mounted on the left, this will be at the top of the wheel travel). 7. Use rocker switches for the two rockers. I've looked through a number of rocker switches and none match close enough to the 10x22mm hole, but I did find some that lets you to put your own cap on top, so I will most likely 3D print one. 8. Use a project box to enclose the entire ICP. Someone recommended that the Polycase LP-70P is almost an exact match for the ICP and I agree. With a custom ICP backplate to act as the LP-70P's cover, it will hopefully look like the project box was designed for the ICP itself. I will try to achieve as many of these design goals as possible, but one limiting factor is that I live in a very small apartment and only have access to hand tools. I will need to outsource anything that requires any degree of precision to other companies, which means that nearly every component will need to be made elsewhere and shipped to me. This can easily spiral costs out of control, but hopefully with some good measurements and initial CAD work, I can minimize the risk. Otto T4-CN211N DCS switch mini-review: For $100, I have mixed feelings about this switch. It requires a heavy activation force when pushed in any direction, which is exactly what I want, but the 4 directions all feel different than each other. Pushing the stick to the left is smooth all the way until it hits the limit of its travel, and I expected all 4 directions to feel this way. However, pushing it up and down requires a heavier force, and has a region where the force gets heavier, similar to how a Cherry brown switch feels different once you get past its activation point. The right side requires an even heavier force than the other 3 sides. Because the switch is weather sealed, there's no way for me to open it to adjust it internally. It feels like there's a big spring coiled around the stick, but is coiled in a way that makes the 4 directions feel different. I'd imagine that in actual use this is not much of a concern, but evaluating it by itself, I feel that it doesn't really feel like it's worth $100. Another thing is that the switch has a very small lip, only around 0.85mm. The catalog states that it's a 11/16" thread, which means a 45/64" clearance hole is needed for a close fit or 23/32" for a free fit. This translates to a 0.2mm or 0.4mm gap around the switch. If you can't get the hole drilled very exactly, it's too easy to accidentally drill away too much due to the low tolerance. Hispapanel ICP Front Panel I was originally considering getting the $425 Viperpanels.com ICP panels, but after reading stories about how the owner doesn't reply to e-mails and fulfills orders sometimes 6 months to a year after the order date, I decided to get the Hispapanel ICP panel instead. It arrived inside of a week. The panels come with the protective layer still attached; the pictures above are of the panels after the protective layer is removed. The two intermediate layers are transparent except for the sides, and the front panel itself is made out of 2-layer acrylic, but the white layer is opaque. You can shine a LED light through it, but you need a fairly bright LED that's right up against the acrylic in order to get any sort of brightness on the other side, though the upside is that it acts as a natural diffuser. The panels are about 3mm thick each. The ICP also comes with buttons that are also made out of 2-layer acrylic with the words engraved on top (Redneck's ICP has the words engraved on the reverse side). It also comes with clear acrylic pieces slightly larger than a button and a square hole in the middle. I'm not sure exactly how you're supposed to put these together; I know that you're supposed to glue them together, but I don't know what the square hole is for or how exactly you're supposed to align them together. The square hole is also too small for a tactile switch stem and there's no alignment marking on the buttons themselves, so my guess is that it's just some kind of manufacturing thing? 3 of my buttons also came with chips in them. 2 might be issues with shipping (they're shipped together in a single bag, so they could be rubbing against each other), but 1 was very obviously chipped during the manufacturing process itself: Wheels are also provided, but they're not only the wrong color and too thin, but they're also slanted: If you look closely at the image, the grooves don't line up and the top of the wheels aren't straight. The slant is more obvious if you spin the wheel, as it appears to ripple around when spun. One of the wheels I got also has some black spray paint on it, like it was too close to the ICP front panel when it was getting sprayed. Luckily, I don't plan to use the buttons or the wheels, so these issues don't really affect me. Here's what the 3 panels look like when switches are mounted to it. In the end I only plan to use the front panel, but this gives me a good visualization of how the through-hole switches will look like when mounted: Notice that the DCS switch needs to be lower than the other 2 switches that are mounted on the middle layer. This is because it needs more space for the lever to move around in when it's tilted. I measured the required gap to be about 9mm between the top of the acrylic mounting layer and the back side of the front plate. Any lower and the DCS switch will hit the back of the front plate when moved. I also noticed that the amount of force required to move the lever is causing the acrylic to bend slightly. Though I don't plan to use the middle and back acrylic layers, this probably also means that mounting it on a circuit board is not a great idea, as over time the force can cause the board to crack. The keyway for the two toggle switches are also too wide out of the box. Most siwtches require a 1.83mm-wide keyway, but the middle acrylic panel's keyway is 2.35mm. I purchased a set of 1mm files on eBay and filed the keyway down in order to get the switches to fit. I also purchased a M3 nylon screw and spacer set, also on eBay, that allows me to play around with various distances between the 3 panels to see what works best. That's all the info I have to share for now. I'm currently in the process of drawing up a CAD diagram for the ICP front panel so that I can start designing a circuit board for it, but it's a slow process because I need to measure everything. For the most part, it follows pretty closely to the actual ICP dimensions, but it's not quite the same so I need to double-confirm everything.
-
RealSimulator F-16SG-HOM & F/A-18 Joysticks
Ranma13 replied to Sajarov's topic in PC Hardware and Related Software
This question can be viewed in two ways. If you're asking whether the RealSimulator F16 grip can be put onto a base like the TM Warthog base or the Virpil base, then the answer is most likely no. You will be able to physically mount it, but the RealSimulator grip has a ton more buttons: Every control on the joystick is a 5-way switch. Unless the base can handle it or there's a fallback mode in the joystick, the base won't be able to communicate with the joystick properly. If you're asking whether the RealSimulator FSSB base is compatible with the Warthog stick, then the answer is yes. -
RealSimulator F-16SG-HOM & F/A-18 Joysticks
Ranma13 replied to Sajarov's topic in PC Hardware and Related Software
Yes, this is not such a big of a deal for displacement joysticks since even the strongest springs and cams are light enough that you won't have trouble hitting the limits, but with a force joystick you can feel a pretty big difference between the force required to roll left and to roll right. I found myself vastly favoring going left due to how much easier it is, so I changed my roll sensitivity to 150%, which makes rolling to the right 50% more sensitive than to the left and feels more even.