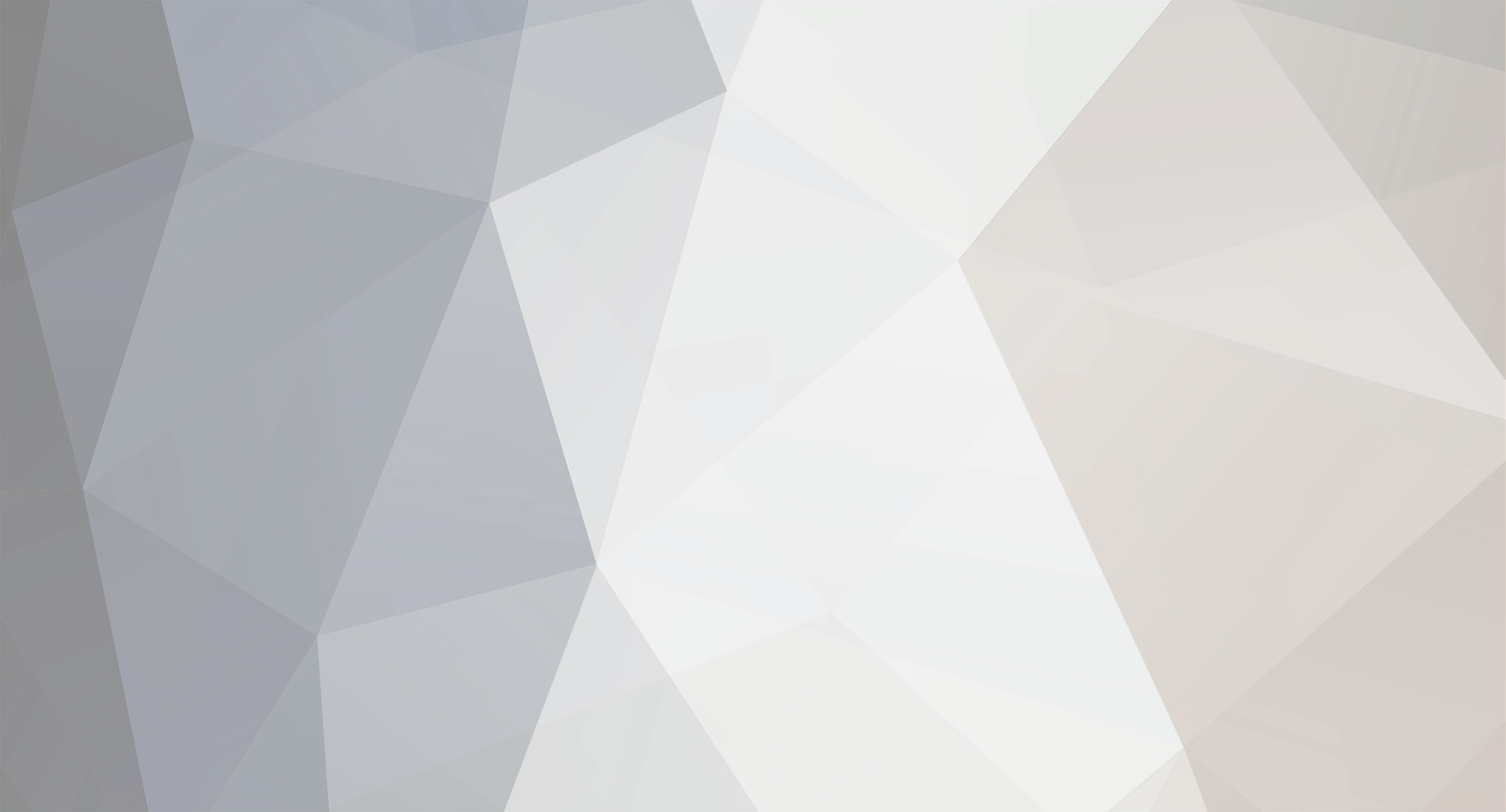
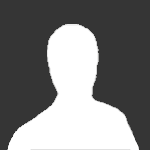
Boltz
Members-
Posts
476 -
Joined
-
Last visited
-
Days Won
1
Content Type
Profiles
Forums
Events
Everything posted by Boltz
-
Questions for Putting MFCDs on Separate Screen.
Boltz replied to SkateZilla's topic in Home Cockpits
This is the only guide I can seem to find on the topic: http://forums.eagle.ru/showthread.php?t=70716&highlight=export+indicators I suspect that you would have to change the init.lua of the Control Input Box (if there is such a file for it.) I have no idea where to find it but I expect this will just require some tinkering and tweaking to find something that works. I would be interested in this as well since the default positions are not always the best especially for those of us with multiple monitors. -
Questions for Putting MFCDs on Separate Screen.
Boltz replied to SkateZilla's topic in Home Cockpits
The RWR is just another viewport I can't remember it's name off the top of my head or whether you have to change its init file but it shouldn't be too difficult to find. Helios just adds the bezel on top of it. It's the same for the clock and UHF repeater. -
DC Guides presents "Exporting data to an Arduino 101"
Boltz replied to Devon Custard's topic in Home Cockpits
This is a great guide DC, I've learnt a lot from reading it. Good to see that others are using the Arduino platform as well though as I was beginning to wonder if I was going in the correct direction. -
DC Guides presents "Exporting data to an Arduino 101"
Boltz replied to Devon Custard's topic in Home Cockpits
Most ICs are pinned differently. If you post a link to where you got them then you will probably see that they have a different pin out compared with DC's. To overcome this problem DC would need to release another version of the circuit diagram with actual pin names rather than pin numbers. @ Joe Kurr: I'm working on something very similar at the same time as well! :lol: -
Questions for Putting MFCDs on Separate Screen.
Boltz replied to SkateZilla's topic in Home Cockpits
I'm an NVidia guy so I'm not sure about the Eyefinity stuff. Certainly with NV the screens seem to have to be identical (or nearly identical) for you to configure NV Surround. Also the 3 screens msut be connected to digital outputs and my card only has 3 so my fourth screen is running on VGA. Since my 4th screen is different it has to be setup in a Surround + 1 setup. Again only know about NVidia but I doubt you could push 7680x1080 of DCS out a single card and still get decent frame rates but I would be very interested to hear what your results are as we seem to have a similar setup but I haven't started upgrading or working on fps. Always been changing my screen setup but I think I've found a good setup now. -
Just other CAD in general. As far as I know you are the only person working on an A-10C and it is looking very nice.
-
Just wondered because the renders look very good compared with other CAD I have seen.
-
Incredible work. What CAD program are you using to do this?
-
Questions for Putting MFCDs on Separate Screen.
Boltz replied to SkateZilla's topic in Home Cockpits
I am running three screens for the main view and a fourth to export the MFCDs. All are connected to a GT640. I don't know about using dual graphics card so all I can recommend is that you test it out. -
I found exactly the same problem and I know that hegykc is planning on using gears but you would have to make sure they had no slack in them to keep precision. Another alternative is to use stepper motors like overpro did (http://forums.eagle.ru/showthread.php?t=115997) however this would require a circuit and programming to calibrate the motor and get it back to the 0 degree position. Servos can also be modified to remove the block that prevents it turning past 180 degrees but you would also have to remove the potentiometer and find some other way to calibrate the sensor (Overpro used a light sensor, if I remember correctly, to do this.) This creates a motor and gearbox that can be controlled by simple servo commands. A tutorial for modifying a servo can be found at simkits (http://www.simkits.com/brochures.php) and scroll down to the "Manual "How to modify a HS-322 Servo"" I don't know whether this only covers that specific type of servo but if you opened up one of yours you could probably work something out. Also as another note, will you be including the 10's needle on the ITT and 1's needle on the core speed indicators? I use them a lot as they make it a lot easier than guesswork from the main gauge when + or -1 is going to make a difference. They would be geared 10:1 off of the main shaft. I think your project is going to get me building the EMI as well
-
Looking good! :thumbup: Quick progress! Now you have the exports working then it should be relatively easy to connect the servos. Find the exports, change them to a servo position and then use the Servo Arduino library to output the position. I used the built in Examples especially the "Knob" one to play around with the servos.
-
iControl DCS (Another iPad pit)
Boltz replied to boarder2's topic in PC Hardware and Related Software
Exit the app and go into settings of your iPad. Scroll down to the settings for iControl and then you have the option to use the CDU in portrait mode. I just got the app today and it took me a while to figure it out. -
They are bringing out "CAN-BUS" gauges so they should be a lot cheaper than the USB ones because they don't need any USB circuitry. It would be quite easy then to build your own interface to them from an Arduino, as long as they bring out A10 CAN-BUS gauges.
-
I was looking through Viperpits yesterday for some ideas and found this build by AlbertJ. His HUD looked incredible but he also tried SMD LEDs for backlighting as well as using the PCB as the back plate to mount the switches on. You'll have to read back a couple of pages and also forward. http://www.viperpits.org/smf/index.php?topic=7674.135
-
I just saw your F-16 pit on Viperpits and it looks amazing as do these panels and the AoA indicators. I assume the aerial refueling indicators will be made in the same way.
-
Please post some pics when you get something to show. I haven't used Helios for 7 seg displays but I do use Arduinos with 74HC595 shift registers, they are relatively simple to get working and can be used to light individual LEDs as well as 7 seg displays although with 6 daisy chained together a simple piece of proto board can get quite full and busy with wires and resistors.
-
Nice caution panel. Was it CNC or laser engraved?
-
Nice one! Hope it works.
-
FC3 export radar and MFCD to networked pc?
Boltz replied to OverDhill's topic in PC Hardware and Related Software
I don't have FC3, but this is should work. Set it up to render the MFCD and radar somewhere on the FC3 computer (corners or on separate virtual or physical screen.) Then there is a small program initially written by Gremlin77 and then finished and released by whartsell. It can be found here:https://code.google.com/p/hogkeys/downloads/detail?name=Iris-0.1.0.11.exe&can=2&q=. More information can be found in Gremlin's build thread along with a short pdf manual http://forums.eagle.ru/showthread.php?t=86916&highlight=gremlin77&page=25 I use it in my pit to export the MFDs to a networked computer running Helios and it works perfectly, although because you are still rendering the MFCDs on the sim computer it may slow down FC3. It does not render them from FC3 onto a networked PC, it just copies a portion of the screen from one computer to another. -
Hey FlyNate. I have a similar screen to you for my CDU and I'm simply using one of these little convertors:http://www.amazon.co.uk/KanaaN-Composite-Converter-SHIPPING-DELIVERY/dp/B003U0PHC8/ref=sr_1_2?ie=UTF8&qid=1388572948&sr=8-2&keywords=composite+to+vga (There are loads of them on there, so I'm not sure who the seller was) For exporting other items than MFCDs, the init.lua of each indicator must be changed. Check out this guide: http://forums.eagle.ru/showpost.php?p=1152239&postcount=1
-
Thanks Cali. At the weekend, I spent the whole time flying till my extension broke due to a faulty cable. I changed the setup to a side stick while I worked on the extension. I thought my stick was dead. With a multimeter I checked the cable and something was wrong with it. I think it was under too much stress. 6 ft of cable doesn't fit nicely into a 22mm copper pipe only 400mm long. The solution, which arrived yesterday was this: http://www.amazon.co.uk/Belkin-MINIDIN6-Keyboard-Extension-Straight/dp/B004PZZILM/ref=sr_1_9?ie=UTF8&qid=1388488136&sr=8-9&keywords=ps2+extension+cable Wherever I looked the smallest size I could find was still 6 ft long but this one has those 6 ft tightly coiled. It works extremely well and provides a much stronger electrical connection than the £2 one I had before. I recommend it to anyone who is struggling fitting such a long cable into their extension. Yesterday I cut the acrylic for the left outboard sides and drilled a couple of panels before the cold got the better of me. I retreated indoors to enjoy a nice drink and finished the caution panel electronics and 74HC595 shift register circuits. Software has changed hugely now, though not cosmetically. We now have standard code that can do all inputs and outputs and go on any Arduino. It is not specific about number of pins or anything as the software will initiate the Arduino by telling it which pins are doing what. It saves you having to mess around with Arduino code just to add in a potentiometer.
-
I just came on to this forum issues section to see if there was anything about the snowstorm. Just reading this without anything else open is running my laptop at 80%. I was just wondering why the fan is so loud just to be on the forum. Edit: Snowstorm gone, I now have Christmas lights which are not working the CPU as hard.
-
The TM base on a sledge sounds like a good idea, that means that trimming the aircraft will actually change the position of the stick. Variable resistance would be good as well although it is unlikely. On the ground control surfaces move a lot better than when in a 60 degree dive at 350 knots and also the manual reversion mode could actually be felt. Some people have done this to yokes in 737 simulators. I believe they used stepper motors to change the length of springs. To do so you would probably have to stop using the base for the TM Warthog and probably build something with potentiometers and springs and dampers. http://www.737ng.co.uk/technical.htm If you scroll down a bit in that link you get to a bit about building your own 737 yoke and a pdf. Something like that but with a stick would be great because you would not have to worry about breaking the TM Warthog. It could easily be interfaced through an Arduino and the grip could be connected to the base by a ps2 extension cable like PeterP's joystick. He uses the base for the buttons but not for the axes.
-
I've got a full length extension at the moment. Got a new cable in it today so been doing some flying and it seems that sideways movement does not need to be limited to stop it hitting you, just tweak the curves and it is very similar to when I've flown in aircraft with a centre stick. The only concern would be that it may put too much stress on parts in the base and yes there is a lot of leverage on the base. The handle weighs more than 1 kg and its 40cm away from the base so it does push quite hard on the TM base. The main problem I have is there is not enough resistance on the stick but Flims extension will sort that out. Just make sure there is no slack at all at the top or bottom. Even a small amount of play at the bottom is huge at the top with the sort of forces and weight up there.
-
Can't wait till February hegykc!