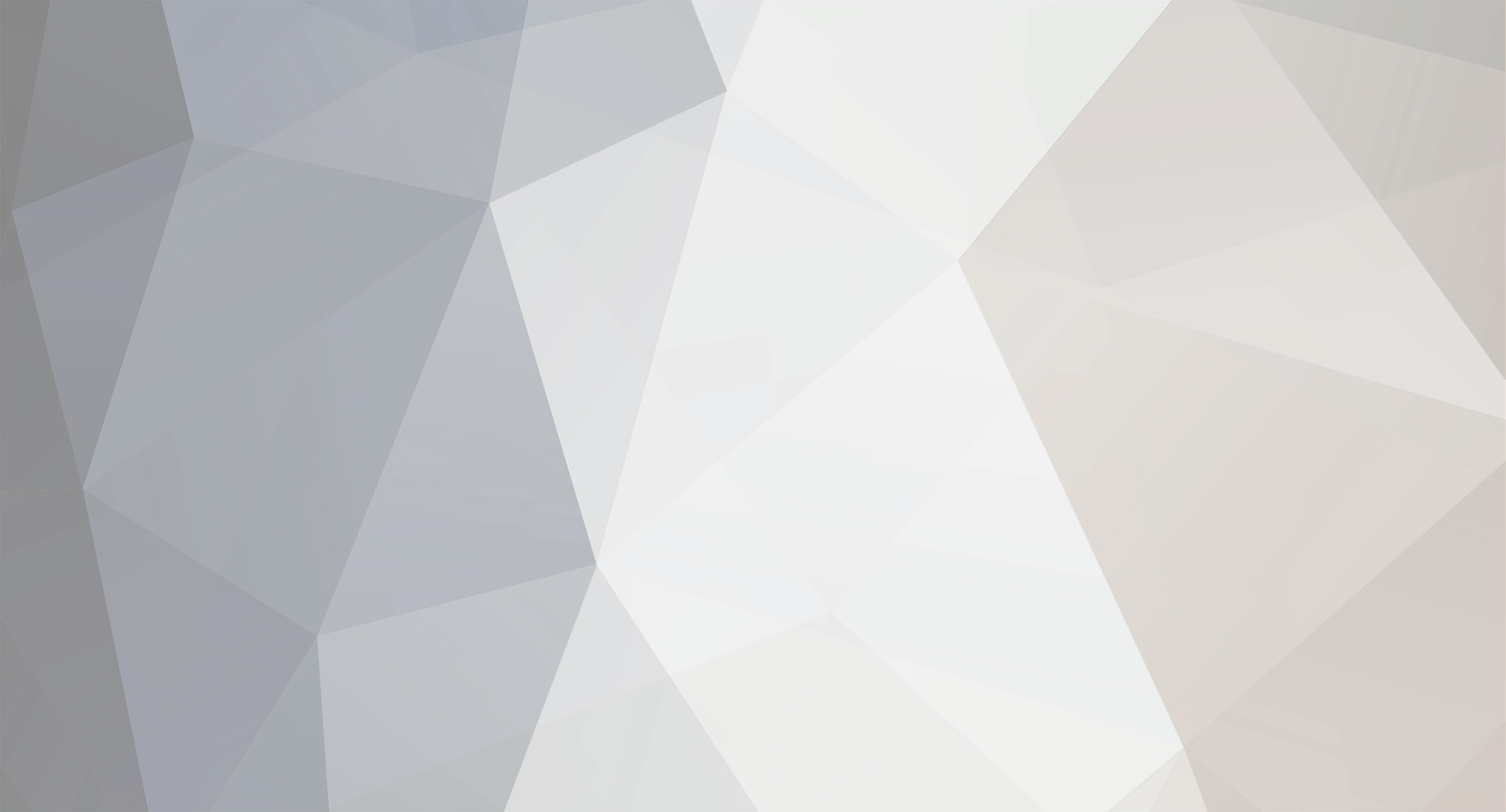
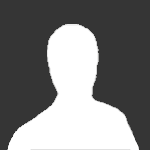
98abaile
Members-
Posts
717 -
Joined
-
Last visited
Content Type
Profiles
Forums
Events
Everything posted by 98abaile
-
Does it require the steam version of DCS?
-
-
I'll try and get some photos on Tuesday. If time allows I'll shoot a video.
-
One thing I did notice early on and solved very easily was the springs would creak as the moved within their housing during deflection and you could feel it through the stick. The problem was solved easily by smothering them with big gobs of thick grease (I used the molycoat I used to use on my warthog).
-
I noticed this on the original cams at release, although I didn't check on the replacements I got.
-
Debolestis Shapeways shop
98abaile replied to debolestis's topic in PC Hardware and Related Software
The one with the pots. I can make a remix for the one with the halls if you can tell me the measurements (body width (both X and Y), body depth, hall width and depth and the width of the push button, metric please), but I won't be able to do any test fitting. -
Debolestis Shapeways shop
98abaile replied to debolestis's topic in PC Hardware and Related Software
They were generic replacements from amazon. https://www.amazon.co.uk/gp/product/B00OEF8JJQ/ -
VKB/Virpil/Thrustmaster quick comparison
98abaile replied to Gman109's topic in PC Hardware and Related Software
Any comment about sticktion in the gunfighter? The dry clutches were a real turn off for me in the end because of the mere possibility of sticktion. -
IT IS DONE. https://www.thingiverse.com/thing:2900369 Had to make a modification to the bracket as I discovered last night that the assembly was rocking slightly in the Y axis. Should give you 20 degrees of throw in any direction. Creative commons attribution and sharealike license. Deltaalphalima1, if you want to print and sell these with your kits you are more than welcome to, but I'd ask that you give people the option to buy kits without 3d printed parts in case they want to save a bit of money and print their own.
-
I see. In that case I'll design the hat with that in mind.
-
It'll have to wait until Monday then. I have a second one spare but I'd rather test that first before I go soldering things again (apparently I don't have the knack for it).
-
Do you think I've cooked the replacement stick as well?
-
Okay, sorry for not getting back. The problem by the looks of it was that I'd cooked the pots soldering and heat shrinking them. In any case I've finished modelling the holder for the smaller sized replacement and it fits very snugly now. Keep in mind that adjustments were made based on my printer and its shrinkage; I've included links to the 360 files in case anyone needs to make their own adjustments. Just edit the first sketch, the dimensions for the collar diameter, the body width and the pot width should be at the top of it in the view. They are d1, d2 and d4 if that's useful to anyone. https://www.dropbox.com/s/ukgw424v23p8a6j/Slew%202%20elbow%20v4.stl?dl=0 https://www.dropbox.com/s/wpw51ct2qkalyep/Slew%20version%202%20v6.stl?dl=0 Fusion360: https://a360.co/2HRSS7M https://a360.co/2JRIj11 My parts were printed in 0.2 PLA+ 205/70 with supports and fit tight. Still need to model the hat though. The problem I have now is that when I move either axis to the limit of one side of its arc (past 0 according to raw data), it flips out and starts bouncing back and forth. Towards the other end is completely fine though. Vin and GND are connected to the outside pins on both pots with the axis connected to the centre pin.
-
I'll post the pictures later when I get home. X and Y went to the center pins on the pots, Vin and GND went to the outer pins (traced from the breakout board it was on orginally) on the X pot and were linked across to the respective pins on the Y pot.
-
Well that feels like a waste of my weekend (it wasn't, I learned a lot and now have most of the work done for the revised version), but I finally got round to designing a mount for a thumbstick. After multiple prints and a bit of frustration editing the wrong sketch, I assemble it all and it fits near enough perfectly without any destructive modding of the throttle handle. Before wiring it up, I decide to check the thread; only to notice that the thumbstick everyone else is posting is smaller than mine (I was using an arduino thumbstick I had lying around, I assumed it was the same). "Oh well at least I've got mine done now and it's sure to help someone else out" I say. So I get to wiring it all up, put it all together, run the calibration and go to test it out. Not working.... or at least it's not working properly. In one direction it maxes out before the full throw, in the other it rolls over to the opposite side of the axis. I recalibrate again hoping it'll solve the problem.... still no luck. Scratching my head, I wonder if I've wired it wrong, so I fish out the board it was originally mounted on to take a look...... 5V I assume this is the problem since the pinout Deltaalphalima1 provided says 3.3V. Gonna order the proper one now. Will edit the design and post files when I get it. Still need to design a hat though.
-
Is there any specification for what kind of foams you use?
-
The real ones are much more contoured I believe, but yeah, I like the idea but like many other projects of this kind, I can't imagine sitting in it for any length of time; certainly not without some very padded cushions.
-
As the title suggests, (before I dive into it) I want to know if it's feasible to use a raspberry pi with a touchscreen and a helios style interface with DCSbios. The idea being to have a single plug and play device that allows you to select the module you are flying and control the cockpit with a helios style touch interface rather than having to make multiple panels for every single module you want to fly. Connecting via USB would be preferred but not a priority.
-
I'd love one too.
-
Yes please. If I can get it to work with a thumb stick I'd be happy to try modeling a drop in mount. Would your PCB and code have support for the center click?
-
I don't think you'll find anything similar. The visible part is actually not a switch, it's just a lever that acts on regular tactile switches soldered to 2 boards behind it.
-
Is this plug and play or does it require coding?
-
Cool.
-
Open Source Joystick FFB / DIY FFB Joystick
98abaile replied to Berniyh's topic in PC Hardware and Related Software
If the gear ratios need to be increased so we can use a higher RPM, so be it, pulleys and belts are cheap. If I have to put up with a tiny amount of cogging that'll be damped somewhat by the backlash in the belts anyway, that's ok. I'm not saying you can't burn money if you want to, but consider the rest of us in your design. Because ultimately accepting some very minor flaws to get decent force feedback is far more reasonable than not having any force feedback because a very small number of people are happy to throw large sums of money chasing diminishing returns. Excessive amounts of money are what make it a non starter long before any minor inconveniences, so please consider the what is achievable to us with less money to spend in your design. https://www.xsimulator.net/community/threads/diy-ffb-steering-wheel-mmosffb-in-progress.7769/ If these guys can build better than commercial racing wheels with $35 motors there shouldn't be any reason why we can't do similar. -
Open Source Joystick FFB / DIY FFB Joystick
98abaile replied to Berniyh's topic in PC Hardware and Related Software
There's that word again. Spending $400 on motors before anything else is not reasonable for most people.