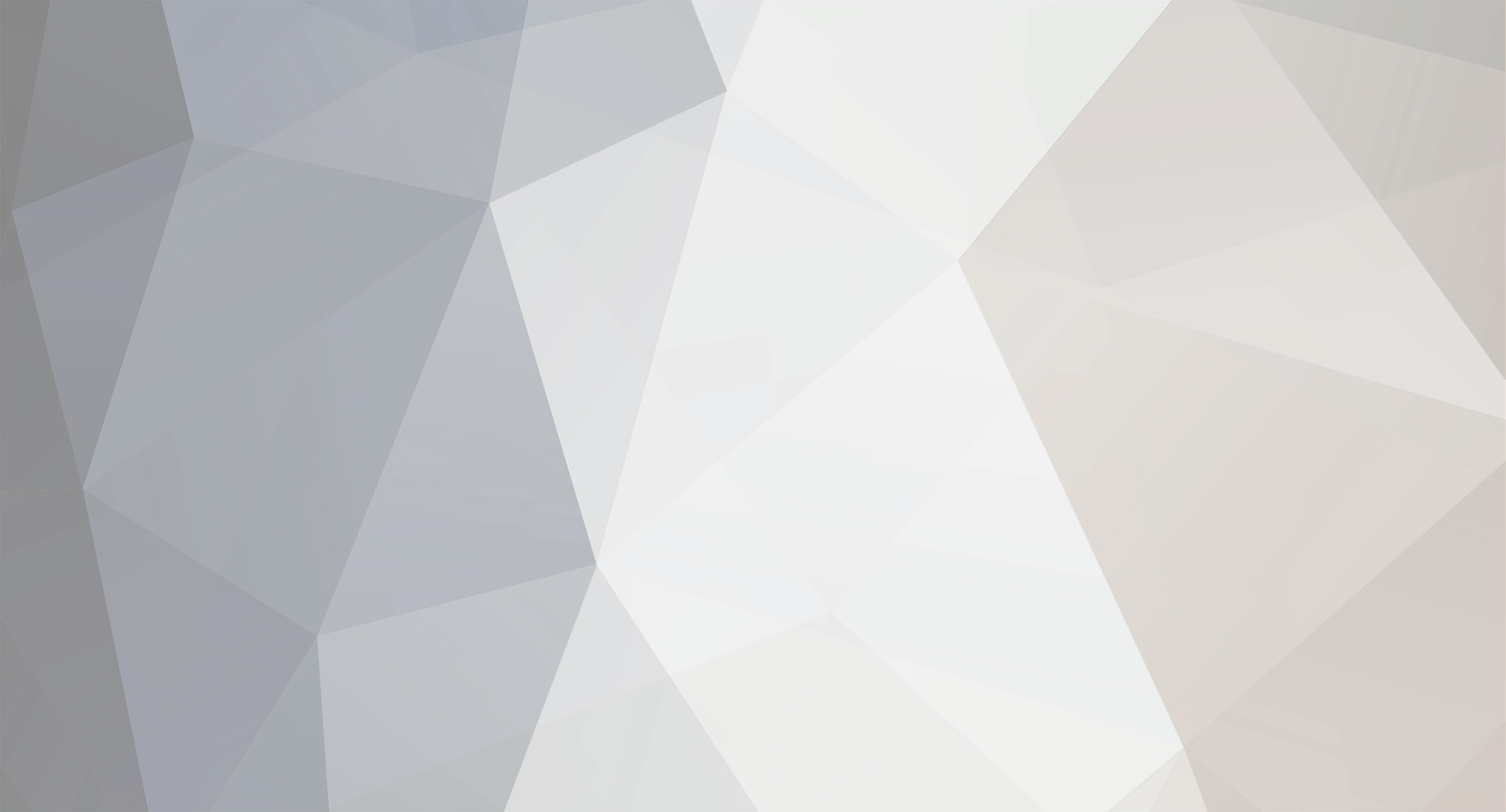
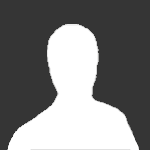
-0303-
Members-
Posts
849 -
Joined
-
Last visited
Content Type
Profiles
Forums
Events
Everything posted by -0303-
-
Rudder trim speed has changed with DCS 2.5.5.31917 Open Beta
-0303- replied to -0303-'s topic in DCS: Spitfire L.F. Mk. IX
If by visor you mean Gun Sight, others have noted this also. -
Just happened to me as well. About 5 min after takeoff (Caucasus, Hoggit map). Interestingly it came back after doing repair. I just checked that "random failures" wasn't checked and came here to post: "gun sight disappearing".
-
It looks like they actually fixed this bug. Yay.:) I bought the P51 January(?) among other things, eager to test the dreaded "rear tank full gravity displacement". Nope, stopped even trying after x number of patches. But now it looks fixed. Now, refueling at 100% does NOT go on forever, rear tank shows full, I loaded the drop tanks for the first time ever. Let's see if this works. This isn't mentioned in the DCS 2.5.5.31917 Open Beta change log. . Ed/Add: It is fixed. Can run on fuselage tank. Can run on drop tanks. Engine stops if on drop tank and drop tank is dropped. Fuselage tank meter visibly moves while being fueled.
-
Not happening to me. Never happened to me. Something in your setup? One thing to try: After repair. To also create a pristine "Saved Games\DCS" environment, rename the "DCS" folder in the "Saved Games" folder to "DCS_backup". Start game and a new "DCS" folder will auto generate. This would loose all corrupted files placed under "Saved Games\DCS". Obviously key bindings and such is also lost but you don't want or need them, you just want to test spawning. If bug is gone you can start copy/overwrite folders, one at a time, back from "DCS_backup" to "DCS" until bug reappears. If bug isn't gone you can easily go back again by just deleting the new "DCS" folder and renaming "DCS_backup" folder to "DCS" again. ~ This fixed a bug for me once. A different bug, the game refused to complete startup and just hang. ~ Sidenote, As I understand it, a good policy is to place all mods (if any) under "Saved Games\DCS" and never place them under "C:\Program Files\Eagle Dynamics\DCS World", the main program folder. I think the latter can cause integrity check problems and I also like that the main program folder remains completely pristine, so no problems of my own making can reside there. Anyone who knows, do correct me on this. I noticed that lots of mods directs to make changes in the main program folder but these mods are generally old and I often find ways to place them "Saved Games\DCS" instead. Then again I have very few mods. ~ Ed/add I'm on DCS Open Beta, like just about everyone else. I converted from stable with updater.exe and that's why my folder isn't named Open Beta.
-
Rudder trim speed has changed with DCS 2.5.5.31917 Open Beta
-0303- replied to -0303-'s topic in DCS: Spitfire L.F. Mk. IX
Two other things happened that never happened to me before that makes me wonder if damage model was changed. a) Tire blowout. Landing wasn't all pretty but no wing scraping. I've landed the Spit a lot so seems weird I've never seen this before. b) Ripped off wing tip in high speed snap roll. This could be I seldom (ever) do snap rolls. Was only yanking stick to verify the ASI AoA bug. -
This is a bug? The ASI indication drop (and increase) with AoA/G application was so obvious I figured it must be real, otherwise it would've been fixed.
-
Confirming this. The exhaust flames have now moved somewhere else. They're not visible anymore. An easy way to get exhaust flames is to just to prime it to much. ed/add: It's a bug. Nothing to do with night or day.
-
It is now moving in shorter steps. It takes longer time to move. People have wished for a shorter step and a user mod doing this exists. Spitfire isn't mentioned at all in the DCS 2.5.5.31917 Open Beta change log. The elevator trim speed seems unchanged. I wish the Spitfire had the same "speed increases if button held x secs" as the P51 does. It is tedious to switch between takeoff trim and landing trim. P51 trim works in three modes. a) single taps move small steps b) Held button moves slow for two seconds c) Held button moves fast after two seconds (estimate two seconds)
-
My opinion. After long practice and hair pulling I arrived at: this is the only way to land the Spitfire (or any tail dragger) consistently safely. Fly all the way down, real close to the runway and slow enough that it's close to the "sitting on ground attitude". One can then either let it drop by itself, or cut the power if one thinks it's close and slow enough. The feared "bounce" isn't really a bounce. It's the wings angling up when the tail goes down, making the plane take off again if the speed is to high. With tricycle planes you have no wing angle change on touch down and you can be more nonchalant about touchdown speed. ~ For taxiing (Spitfire), if getting into 'the zone' one can taxi long stretches without hitting the brakes, at about 1000-1200 rpm. After landing, one have to tap the brakes to go straight and not ground loop. Once in a blue moon one can roll all the way to stop with only rudder input. I did notice how ugly I used to land the P51 after learning the Spitfire because the P51 is so forgiving. ~ An additional thing is that you can't see shit over the long noose of the Spit (less so P51). So coming in long and straight is a no go. Either a curving approach or steep angle descent to keep RWY in sight.
-
It did have "pre flight stab trim" if you believe this. Real life aircraft was more convenient with the ability to fix trim on ground. I wonder how complicated it would be to implement this? Thinking in terms of validating the flight model for every setting which is a standard we expect from ED. I'm sure I'll get this plane eventually ground trim or not but I do think doing this (real life ground trim) is a good idea and worth the developers effort.
-
The four screws holding the four poles (see picture) from below must be tightened to eliminate any wiggle of the poles before anything else is reassembled. (reusing old image, the washers in the pic are unrelated) To get at the four screws from below the base plate must be removed. This gets access to three of the four screws. Remove the two small screws holding the circuit board and gently push it aside to get at the fourth. One can not get any good grip on the poles to tighten them well, nor does one need to. Just screw them enough so there no is wiggling of the poles. Put the top part together. Tighten both screws of each pole at the same time with two screw drivers. If tightened from only one end the other end (especially bottom) may rotate. Reassembling the whole thing without eliminating the wiggle first will not work. Also, if tightening them first before assembling the top, you'll know the resistance you'll get is real and there's less risk of threading. ~ Figured this out yesterday. I had a small wiggle, reassembled and now have zero wiggle. I can now not move the joystick ever so slightly without also seeing the virtual stick move. Solved this problem for me. I didn't understand how I could have wiggle given how the joystick is designed. No matter mechanical wiggle the sensors always see movement (unless the poles can move). I had reassembled it incorrectly when I had this wiggle and I believe the poles were moving a little.
-
- tm warthog
- hotas
-
(and 1 more)
Tagged with:
-
If you make a single player mission in mission editor you must make SKILL as "client" or "player" otherwise it will become an AI plane. I know "client" works, I read that "player" also works.
-
My broadloom mat is cleaner where the tape has been:music_whistling: I would be concerned about leaving stains too and with a hard floor (linoleum, wood) I would have used glued on rubber feet (or possibly screwed on rubber feet but I believe glued on's are very likely good enough, cheaper and simpler). Rubber feet has the advantage that the plate can be easily re-positioned an unlimited number of times *1). Rubber feet would've been my first choice for a hard floor. I searched extensively and read that rubber feet would work fine for the purpose of fixing a plate with rudders to a hard floor. You could also just let the plate rest against the wall, no further fixing required. For 'reasons' I couldn't do this. Note, you most likely want rubber feet distancing the plate a little bit from the floor because otherwise the four bolt heads holding the rudders will dig into and make marks on the floor. I had to have tape (double sided) for a broadloom mat I thought (still do), rubber feet would slide and I didn't want metal spikes digging into the mat. Note, no particular reason for 800x500x16 dimensions, it's just a plate I found at Bauhaus (euro vendor) and found no reason to cut it smaller (on the contrary I might mount a stick extension joystick to it). I am considering cutouts under the pedals though so I can angle up the pedals and have heels on the floor. ~ *1) Not that repositioning was/is big a problem with this kind of tape. A single length of 4 dm was enough, could be re positioned 3-4 times and I have 5-10 meters(?) tape for about $5 (?).
-
I found a wooden/epoxy (not sure exactly) plate 500x800x16 mm and drilled four holes. I used broadloom tape to fix it to the broadloom mat. Broadloom tape (double sided ed/add) is super strong, didn't know tape this strong existed. Broadloom tape is used to permanently fix broadloom's to the floor. Find it in a builders store (Bauhaus Europe). Anyway, broadloom tape is the absolute cheapest simplest fastest way to fix the plate (if you have a broadloom, for hard floors they work as well I imagine but some kind of rubber feet are more 'elegant').
-
I opened mine once and found this. Connectors sealed with something. Is that hot glue? Here's a thread with throttle inside pics.
-
I think I might have made a mistake in suggesting there's only between 3.2 - 4.8 mm available for fully compressed springs placed in tandem with the original springs. Taking a second look at a picture I took (below), I think something else might be going on. Two washers (1) are placed under the original springs (2) to stiffen them. The washers are 1.6 mm thick each (total 3.2 mm), outer diameter of 12.0 mm and an inner diameter of 6.4 mm. Notice the widest point of the gimbal, the 'brim' (3). I had made an experiment putting the washers on top of the springs instead of under and then I got slack. I interpreted this as the washers being to wide (12.0 mm) and touching the 'brim'. I just realized maybe this happens with the washers placed under the springs also if they rise higher than the black platform (4) at center. As mentioned 2 washers (1.6 x 2 = 3.2 mm) no slack, but 3 washers (1.6 x 3 = 4.8 mm) I get slack. Point being, if one could find washers with smaller outer diameter, they would not interfere with the 'brim' and maybe they could be 4.8 mm or more. I decided I really want a stick extension to be able to fly, especially the WW2 planes (which I'm into), with more ease and precision. The greater throw will also attenuate the spring force. So I will not pursue spring mods further for the moment. ~ Note 1, placing using two washers as in picture did not make much of a noticeable difference in perceived spring force. Note 2, The washers are white because they're nylon not metal (no particular reason, except something 'soft' felt safer). Note 3, If I were to pursue spring mods I like the idea of using a slightly larger diameter spring placed just outside the original springs. This would not have issues with limited compressed length and also no risk of springs in tandem getting entangled and damaged because of entanglement (this could be an irrational fear). Note, a washer between a tandem pair could be a safeguard against entanglement. Note 4, I find the four poles holding all this together as kind of weak and spindly. Also it's annoying that each time I loosen the screws on top, the screws in the base also get loose and need to be tightened. Because of the 'spindly-ness' I'm scared of threading each time I do this. But I think it's important to tighten all screws just enough but not more, because a) if they're allowed to move, this will increase wear significantly and b) there will be slack. I'm quite tired of disassembling and reassembling the base and each time be a little afraid of damaging this spindly construction. Note 5, I covet a VKB or Virpil base, adjustable springs, better quality (see this thread post1, post2).
-
It was reported at least 5 months ago, 20 dec 2018. https://forums.eagle.ru/showthread.php?t=227452 Fix it already:mad:
-
Where did you find the springs? What did they cost? I've been looking for cheap springs to do just that. I didn't want to order expensive springs from Thrustmaster (or from Sahaj). I've looked without success for springs of the right size. I measured the original springs with a slide gauge (see image): Length: 19.3 mm Outer diameter: 7.6 mm Wire diameter (difficult to get at to measure): 0.53-0.55 mm Compressed length: 3.7 mm The four poles they sit around are 6 mm diameter. I even tried to make my own. I don't have the tools or experience. 0.75 mm piano wire is to strong to shape without good tools. I have 0.5 mm piano wire I haven't tried yet. Seems modifying springs can be done in three ways. a) Replace original springs b) Put two springs in tandem c) Have a slightly larger spring outside the original springs (I tried to shape new springs around an 8 mm drill bit) I favor keeping the original springs in place because that's a surefire way of not loosing them. Compressed length is important (note, one should never compress springs fully). Adding 2 washers (3.2 mm) works, adding 3 washers (4.8 mm) introduces slack. I interpreted that as: There is only between 3.2 - 4.8 mm available (beyond 3.7 mm) for a fully compressed added tandem spring.
-
Warthog Throttle. New sound and movement. How normal is this?
-0303- replied to -0303-'s topic in Thrustmaster
The pin is as far away from the cylinder it can be. Still wiggle. It wouldn't make sense for it to magically become magnetic so that sounds plausible. I don't get why it needs to be magnetic though. So most likely wear has introduced a slack that allows it to wiggle while it couldn't wiggle when it was new. Ed/add: On second thought. The magnetism is probably to keep the throttles together and not have an ugly wiggle while they are connected.- 14 replies
-
- throttle
- thrustmaster
-
(and 3 more)
Tagged with:
-
Warthog Throttle. New sound and movement. How normal is this?
-0303- replied to -0303-'s topic in Thrustmaster
You are absolutely right. Both pin and cylinder are strongly magnetic. That would be a safe innocuous explanation for the wiggle (as opposed to something stuck in the mechanism). I can feel a force when the throttles are lined up that isn't there when the throttles are not lined up. Is it meant to be magnetic? Or did it become magnetic since I received it? If the latter how did that happen and can I safely demagnetize it I wonder?- 14 replies
-
- throttle
- thrustmaster
-
(and 3 more)
Tagged with:
-
Warthog Throttle. New sound and movement. How normal is this?
-0303- replied to -0303-'s topic in Thrustmaster
Just to note. There's two ground wires in my throttle. Another throttle thread with good pictures. I took pictures while I had it apart. Just now I labeled the screws A-F. =Panther= would you mind indicating which two screws you are referring to?- 14 replies
-
- throttle
- thrustmaster
-
(and 3 more)
Tagged with:
-
Need Helicopter Hotas recomendations.
-0303- replied to BranchPrediction's topic in PC Hardware and Related Software
For what's it's worth I talked with a real helicopter pilot who also flew simulation on his PC. He was of the opinion that there's no specialized helicopter controllers worth the prize buying. Meaning, he wouldn't shell out for any specialized helicopter controllers. That doesn't mean IMO (as gathered mainly on this forum) that you want a strong spring joystick for helicopters or that you want a Warthog for helicopters. -
While moving either of the dual throttles the other throttle moves a little when the throttle pass the other and a clicking sound occurs. Would've shown better with a non-handheld steady camera. Looks, sounds worse in reality than on video. Does anybody else's throttle act and sound like this? It's disturbing because I think it is new. I fear maybe the friction mechanism starts to break down. Throttle is 4 months old.
- 14 replies
-
- throttle
- thrustmaster
-
(and 3 more)
Tagged with:
-
Need Helicopter Hotas recomendations.
-0303- replied to BranchPrediction's topic in PC Hardware and Related Software
Your not wrong. It is exhausting to try to research everything. Been there. -
Need Helicopter Hotas recomendations.
-0303- replied to BranchPrediction's topic in PC Hardware and Related Software
Again for OP. I take back my statement about the throttle being fine. I wouldn't recommend either the TM joystick or the TM throttle. Bad design, low quality. Now my throttle started to exhibit a slight plastic "crunchy" sound when one of the dual throttles moves past the other. The non moved throttle wiggles slightly sideways when the other throttle moves past it. It's 4 months old. I got the feeling that, whatever the friction mechanism is, it's starting to "frazzle". I couldn't find a pic of it. What I suspect: This, makes me scared to even try to disassemble the throttle. I started to unscrew the screws underneath (before stopping) and noticed that the screws looks to be metal screws in plastic threads. Not a quality design. ~ About HOTAS being pricy. I wanted something with quality which would last me up to 5-10 years or more. An "investment" in the sense I wouldn't need anything else for a long time. I think I choose wisely with the MFG Crosswinds. I fell for the "charisma", the towering market position of TM Warthog and expected it to be good quality. I did read about the strong spring beforehand but rationalized it away to myself. It's true one gets used to the strong spring, but I'm also very sure I could fly with much better precision with a softer spring. In any matter, being able to adjust the spring is important, with the Warthog you can't. ~ I want to get into helicopters eventually. Most things I read (one needs a soft resistance) would dissuade me going for a Warthog for helicopters.